Rockwell Automation GMLC Reference Manual User Manual
Page 732
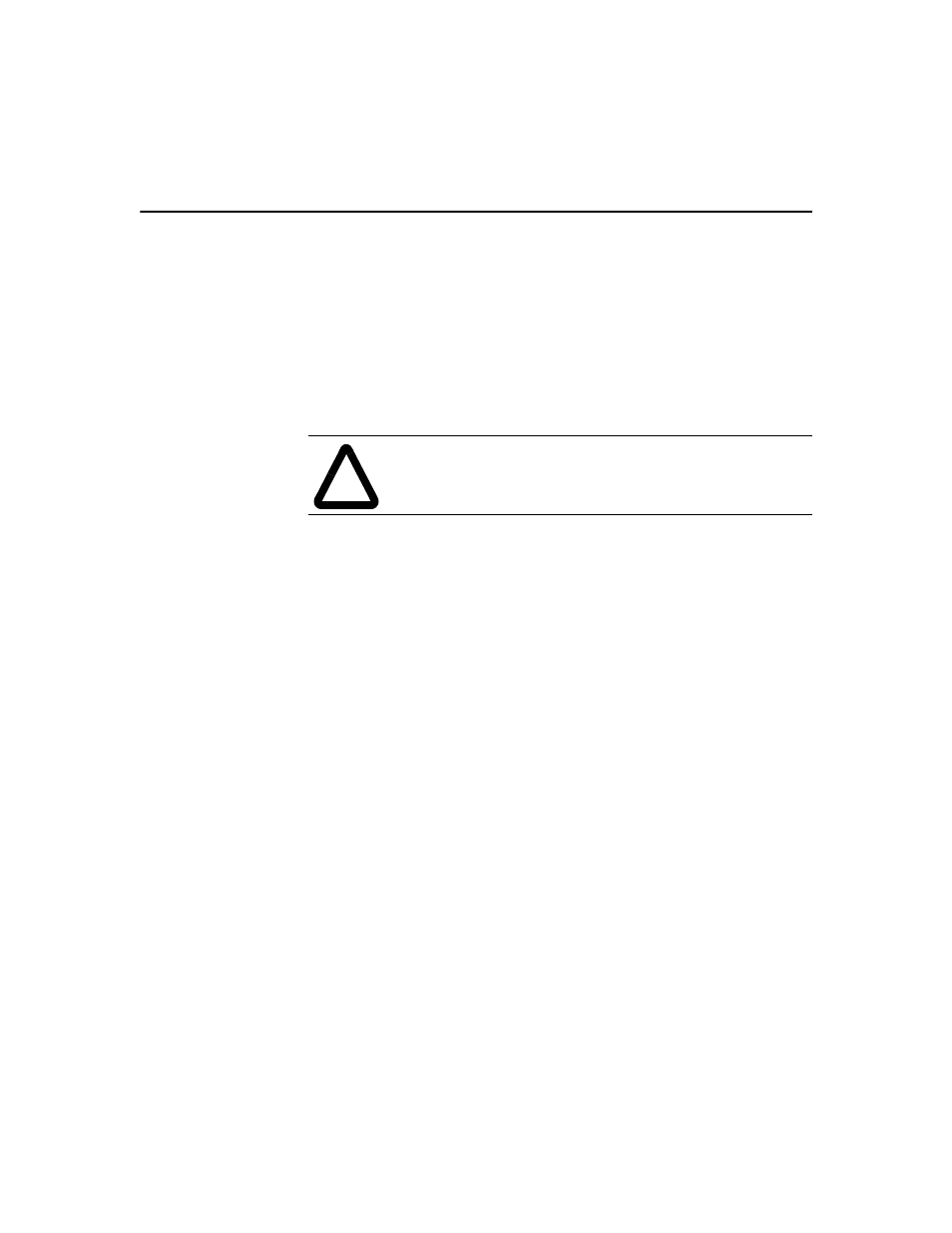
Publication GMLC-5.2 - November 1999
Using the Dedicated Discrete Inputs
695
Stopping Motion with Kill Control
Setting PLC or SLC bit 7 stops all motion on all axes, disables feedback
on all axes, sets all servo outputs to zero, de-activates all drive enable
outputs, aborts the program, and disables the CPU Watchdog. Use this bit
only in an emergency, when the motion controller must be disabled
quickly. The stopping rate of the axes depends on the type of amplifier
and the specific connections used, because the motion controller is no
longer in control of the axes after executing this block.
To re-enable the CPU Watchdog after it has been disabled by the Kill
Control bit, cycle power to the motion controller or press the front panel
RESET
button.
Running and Stopping the Program
Setting SLC or PLC bit 4 runs the application program in the motion
controller (generated from a GML Commander diagram and previously
downloaded). If the application program is already running, the motion
controller ignores this input.
Setting SLC or PLC bit 5 stops the application program. If the application
program is not running, the motion controller ignores this input.
While the program is running, the application program running dedicated
discrete RIO output from the motion controller (SLC input 8; PLC input
10) is set. When the program is not running, this bit is cleared. The PLC
should use this bit to verify that the program has started or stopped before
clearing the run or stop application program bits. If a runtime fault occurs
while the program is running, the program runtime fault discrete RIO
output from the motion controller (SLC input 9; PLC input 11) is set and
the application program running bit is cleared. See Dedicated Discrete
Outputs later in this section for more information on these bits.
!
ATTENTION: Do not use the Kill Control bit in place of
a hard-wired emergency stop circuit for your system.