Virtual axis faults – Rockwell Automation GMLC Reference Manual User Manual
Page 710
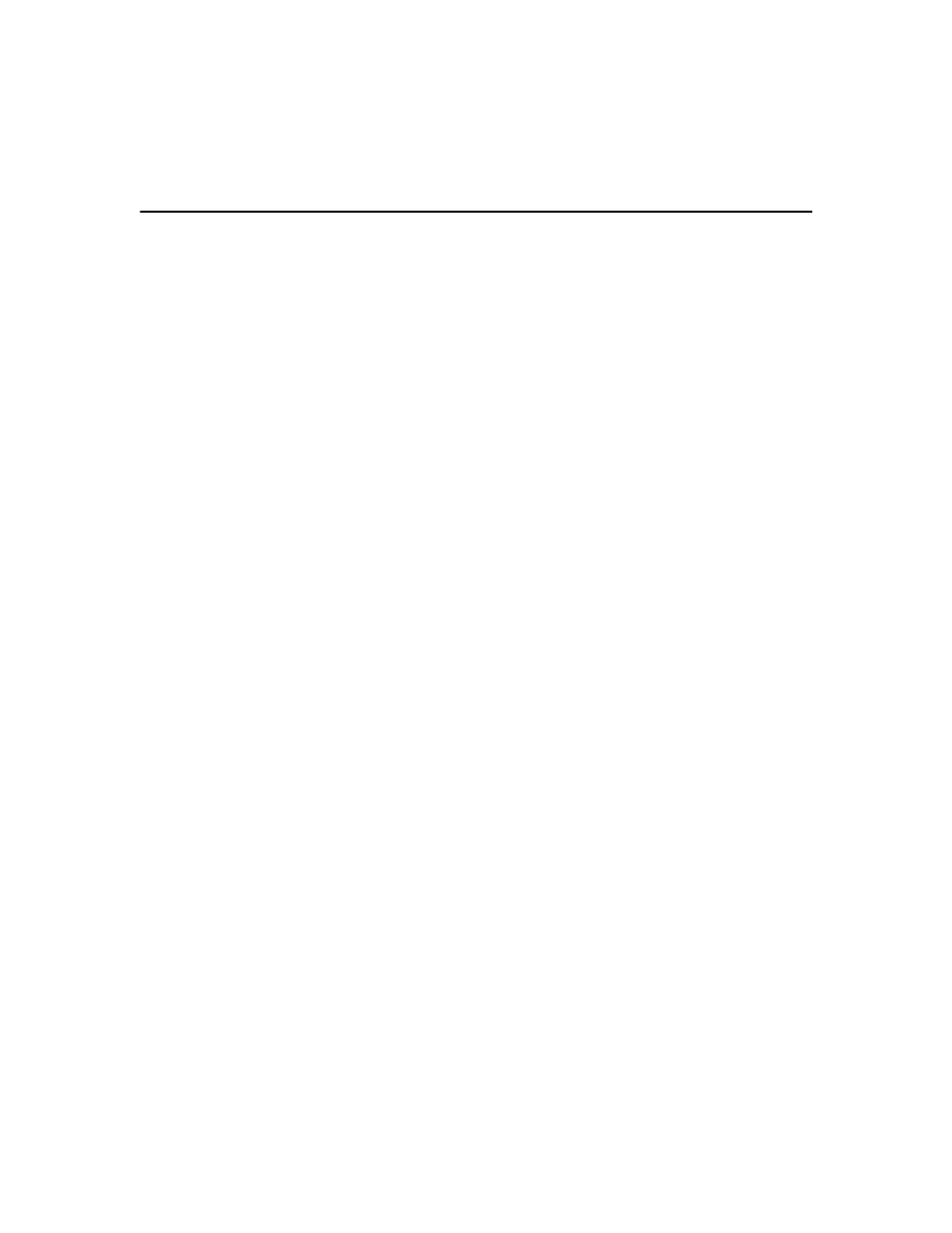
Publication GMLC-5.2 - November 1999
Handling Faults
673
In most applications, AxisLink faults should be handled as part of a
global fault handling task or routine in the diagram. See End Program in
the Function Blocks chapter of this manual for information on the
recommended global fault handler. Since an AxisLink fault in one motion
controller can also cause AxisLink faults in other motion controllers in
the chain, the fault recovery routine must consider the application
programs running in other motion controllers. The simplest solution is to
restart all the application programs via a hardware or software reset.
There are two types of AxisLink faults:
•
Virtual axis faults.
•
General faults associated with AxisLink I/O and the reading of data
values via AxisLink.
Virtual Axis Faults
When a fault occurs on a virtual axis, the Global_fault variable has a
value of 9, and the message “AxisLink Virtual Axis Fault” appears in the
General System Variable Watch window. A virtual axis fault
(Global_fault = 9) indicates that an AxisLink virtual axis connection has
failed or could not be established (timeout).
If a virtual axis link that had been operating properly fails to provide any
new information for at least 4 servo update intervals, the connection times
out. When this timeout occurs, the AxisLink_timeout = 1, Axis_fault = 7,
Axis_status = 14, and Global_fault = 9. In addition, the AxisLink LED on
the front panel flashes red.
The typical causes of an AxisLink timeout are:
•
The AxisLink cable has broken or become disconnected.
•
The motion controller or ALEC, containing the physical axis to which
the virtual axis is linked, has failed or has disabled AxisLink.