Using axislink, Chapter – Rockwell Automation GMLC Reference Manual User Manual
Page 692
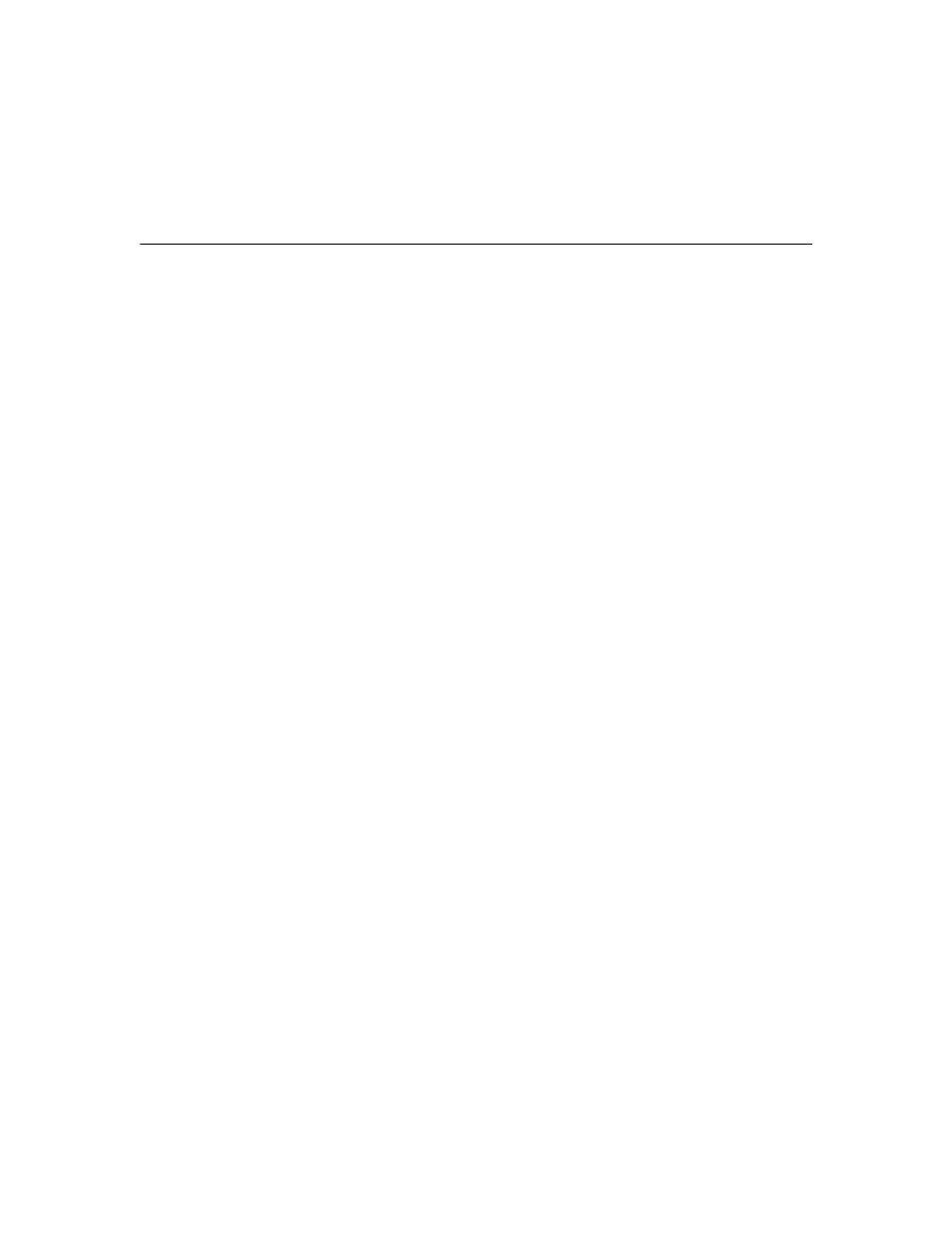
Publication GMLC-5.2 - November 1999
Chapter
33
Using AxisLink
The AxisLink option for your motion controllers lets you use axes on
other motion controllers (also with the AxisLink option) or an ALEC
(AxisLink Encoder Converter) as master axes for electronic gearing and
cams. This means that axes on different motion controllers can be
synchronized, providing real-time coordination for distributed, multi-axis
systems in electronic gearing, cam, and lineshaft applications. Sixteen
discrete inputs and outputs per motion controller are available to other
motion controllers via AxisLink for sequencing and program
synchronization.
Important: Be sure to set all motion controllers and ALEC modules, on
the AxisLink network, to the same servo update rate.
You can connect up to either of the following:
•
Eight modules (motion controllers or ALECs), using only AxisLink,
allowing a maximum of 32 coordinated or synchronized axes, if all
modules are four-axis motion controllers.
•
16 modules (motion controllers or ALECs), if Extended AxisLink is
enabled in the General page of the Configure Control Options dialog
box, allowing a maximum of 64 coordinated or synchronized axes, if
all modules are four-axis motion controllers.
These modules can be placed as needed along the AxisLink cable,
provided the total length of the cable does not exceed 85 feet (25 meters)
in normal operation. For 1394 and Compact motion controllers, total
cable length can extend up to 410 feet (125 meters) if operating in
extended length mode. In any case, the cable length between any two
modules must be 1 meter or more. Refer to Connecting the AxisLink
Cable later in this section.