HEIDENHAIN TNC 407 (243 020) Technical Manual User Manual
Page 192
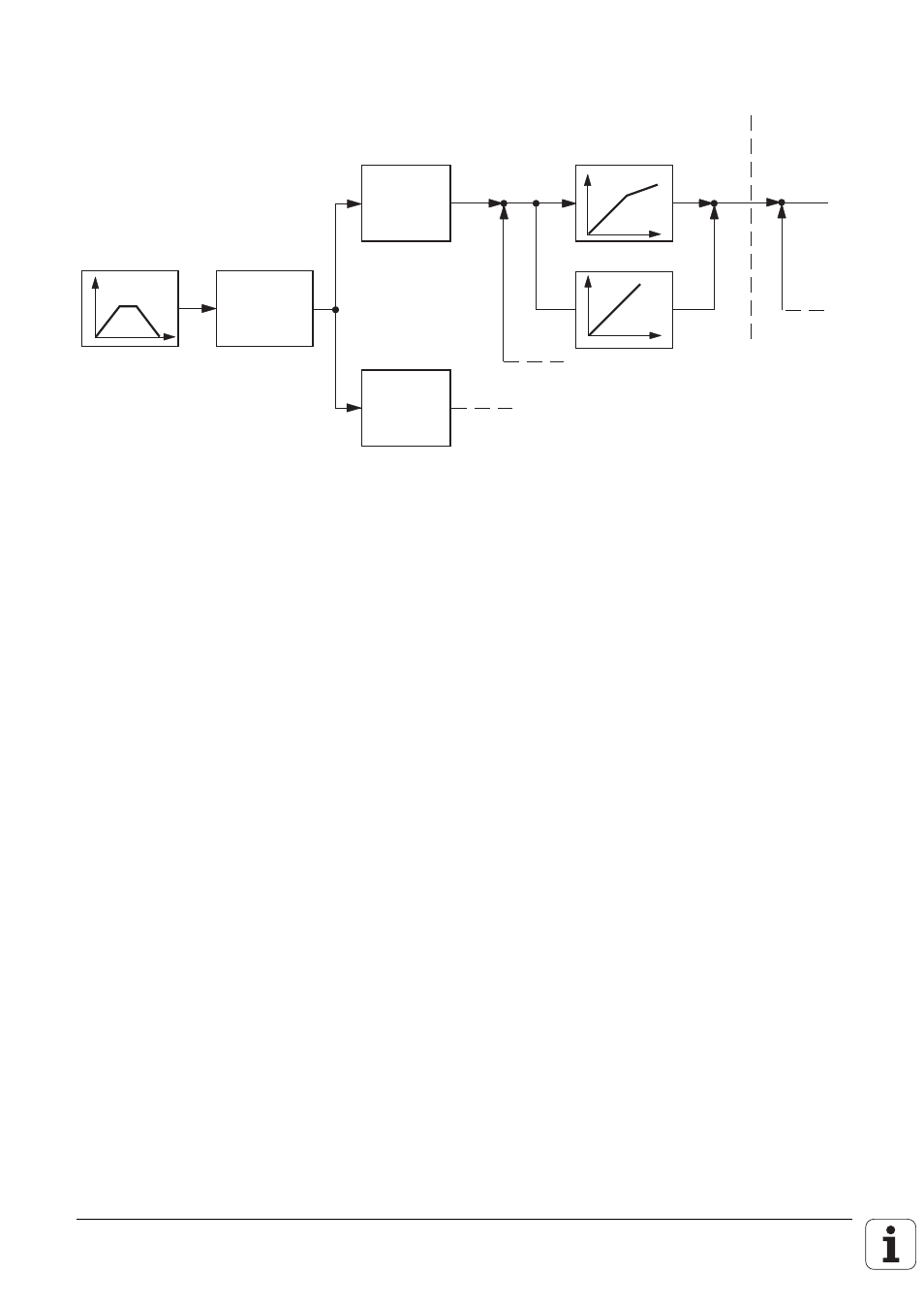
3 Servo positioning of the NC-axes
Y
S
v
t
➀
➁
➂
X
S
Vx
sax
s
ax
+
➃
➄
➅
v
x
Noml+
Servo
amplifier
+
-
v
x
Actl
Acceleration:
MP1060
Integral factor
MP1080
kv factor: MP1810
Kinkpoint: MP1830
Multiplication factor: MP1820
s=s
0
+v·
∆
t
X
Actl
X
Noml
-
v=
a·
t
v
=
k
v
·s a
x
U
t
➀ The control calculates a velocity value every 3 ms (TNC 415) or every 6 ms (TNC 407) from the
feed rate programmed in the NC-program and the final position, allowing for the acceleration
which has been stored (MP1060). The stored acceleration is valid for the rising as well as the
falling slope. If several axes are traversed simultaneously, then the smallest value for
acceleration is effective.
➁ Every 3 ms (6 ms) a nominal position value is derived from the calculated velocity.
s = s
o
+ v ·
∆
t
s
= Nominal path value
s
o
= Previous nominal path value
v
= Calculated velocity
∆
t
= Cycle time 3 ms
➂ The nominal path value is resolved into the individual axis components, depending on which
axes have been programmed.
➃ The axis-dependent nominal path value is compared with the actual value of the positions and
the lag s
a
is calculated.
s
ax
= x
Noml
- x
Actl
s
ax
= Lag for X-axis
x
Noml
= Nominal path value for X-axis
x
Act l
= Actual path value for X-axis
➄ The lag is multiplied by the k
v factor
MP1810 and passed on to the drive amplifier as a nominal
velocity value (analogue voltage).
v
x
= k
v ·
s
ax
v
x
= Nominal velocity-value for X-axis
➅ If the axes are stopped, the integral factor MP1080 is effective as well. It causes an offset