8 plc axes – HEIDENHAIN TNC 407 (243 020) Technical Manual User Manual
Page 163
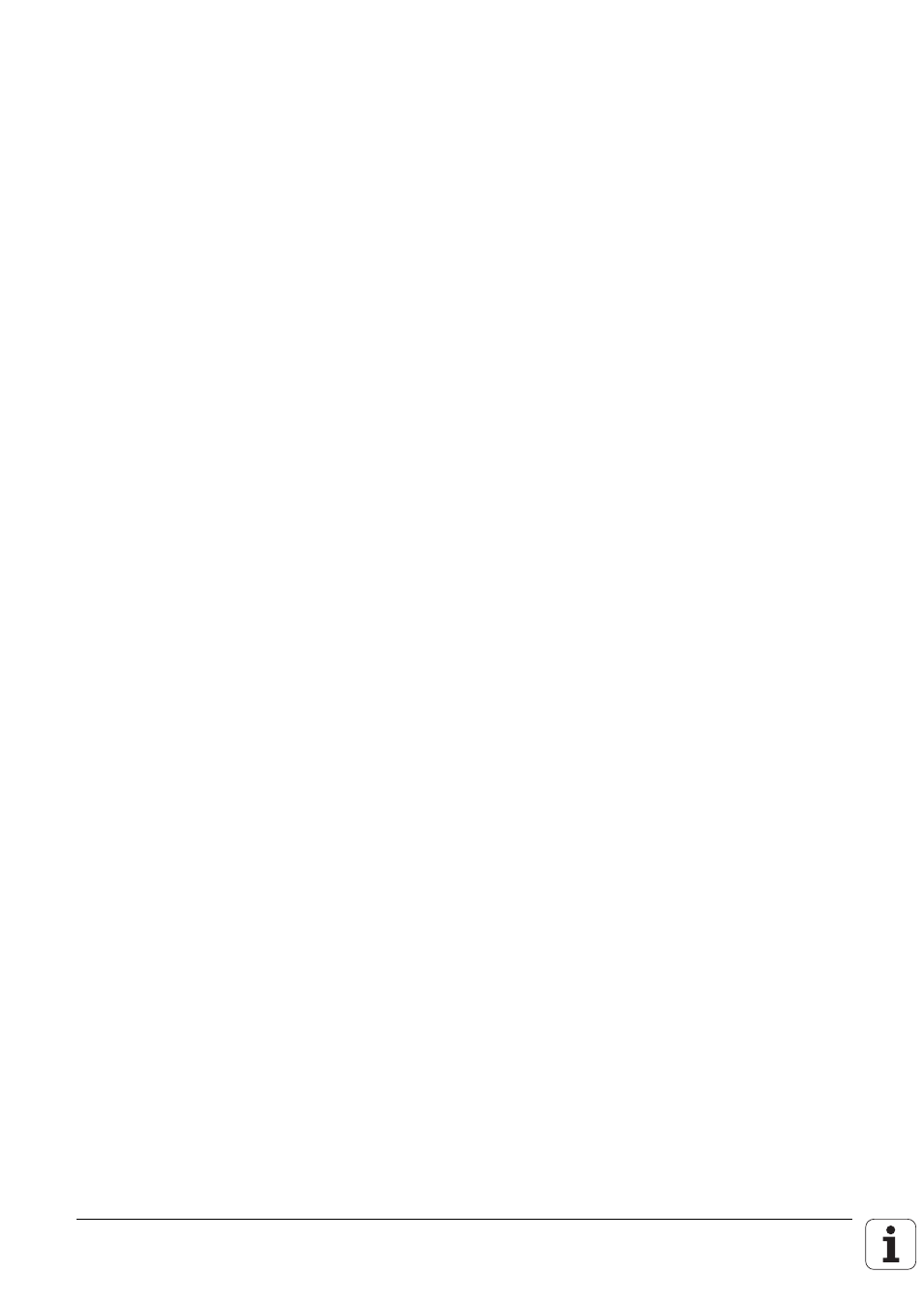
1.8 PLC axes
The controlled axes can be assigned to the PLC individually. On a machine with four NC axes for
example, the 5th axis could be used to position the tool changer independently of the four NC axes.
Machine parameter MP60 defines the axes to be controlled by the PLC.
In the PLC program the positioning of the PLC axes is controlled by modules:
Module 9120: Start positioning a PLC axis
Module 9121: Stop positioning a PLC axis
Module 9122: Interrogate status of a PLC axis
Module 9123: Traverse the reference marks of a PLC axis
These modules are described in the chapter "PLC Programming".
PLC axes are always traversed in the servo lag mode.
Several PLC axes can be started simultaneously. They are not interpolated together however.
A modulo value for the counting mode of the axes can be entered in MP810 (see section "Display
and operation").
MP60
PLC auxiliary axes
Input: %xxxxx
Bit 0
Axis X
0 = NC axis
Bit 1
Axis Y
1 = PLC axis
Bit 2
Axis Z
Bit 3
4th axis
Bit 4
5th axis
Example:
A tool sequence is to be pre-positioned with TOOL DEF. The tool sequence is driven by a controlled
axis. The acknowledgement for the TOOL DEF block is given when positioning starts.
The feed-rate for positioning with TOOL DEF is filed in MP 4210.0 and the feed-rate for reference
traversing the tool sequence is filed in MP 4210.1.
Machine parameters:
MP 10
:%1XXXX
;activate 5th axis
MP 60
:%1XXXX
;declare 5th axis
MP 410.4
: 2
;declare 5th axis as axis of rotation C
MP 810.4
: 360
;modulo value of tool sequence
MP 960.4
: XX
;datum shift
MP 7261
: XX
;number of tools with pocket number
MP 7480.1
: 1 to 3
;output tool and pocket no. with TOOL DEF
MP 4210.0
: XX
;(D768) feedrate of PLC axis with TOOL DEF
MP 4210.1
: XX
;(D772) feedrate of PLC axis with
reference traverse
Auxiliary addresses:
D 168
;desired position
W 230
;number of tools in sequence (=MP 7261)
D 232
;length of sequence (=MP 810)
B 236
;status of PLC axis
B 238
;Identifier Submit job
M 544
;reference traverse
M 599
;logic one