6 stiction – HEIDENHAIN TNC 407 (243 020) Technical Manual User Manual
Page 158
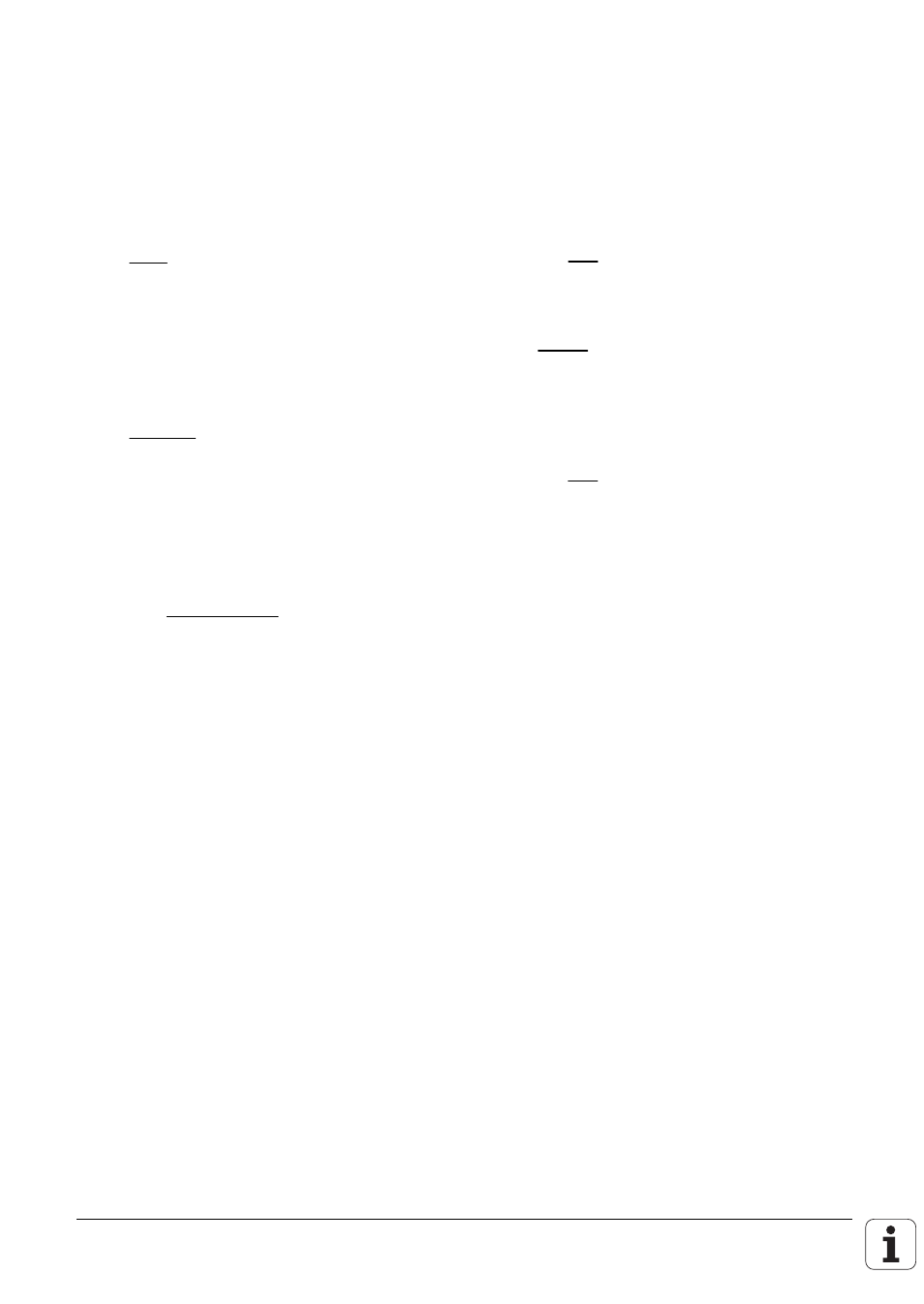
1.6.6 Stiction
Guideways with a relatively high level of stiction can cause servo lag at low feed-rates, even when
using feed precontrol. A servo lag can be detected using, for example the TNC's integral
oscilloscope, and the TNC can also compensate the error. This is done by entering an axis-specific
factor to compensate the stiction in machine parameter 1511 (guideline factor: 5 000 to 10 000). A
higher nominal value based on this factor is then output while traversing.
F
add
=
∆
s
t
a
C
×
k
v
×
MP1511
F
add
= Additional feed rate [
m
min
]
∆
s
a
= Servo lag difference after one control loop cycle [mm]
t
C
= Control loop cycle time [
µ
s]
k
v
= Position loop gain [
m/min
mm
]
MP1511 = Factor for stiction compensation [
µ
s]
V
add
=
MP1050
MP1010
×
F
add
V
add
= Additional analog voltage [V]
MP1050 = Analog voltage for rapid traverse [V]
MP1010 = Rapid traverse [
m
min
]
This increase in nominal value is limited by MP1512. If this limit is set too high then the machine will
oscillate at standstill (guideline: < 50). MP 1512 limits the value
∆
s
a
in the above formula.
MP1512 =
∆
s
GP
a
it
lim
256
×
MP1512 = Limit to the amount of stiction compensation
[counting steps]
∆
s
alimit
=
Limit value for
∆
s
a
[
µ
m]
GP =
Grating period of the measuring system [
µ
m]
Compensation may only be active at low feed rates as the increased nominal value would cause
oscillation at high speed. The feed-rate limit for stiction compensation is defined in MP1513.
Stiction compensation is effective only during operation with feed precontrol. If stiction
compensation is to be in effect in the manual operating modes as well, feed precontrol (MP1391)
must be activated for manual operation in each axis.
MP1511
Factor for stiction compensation
Entry: 0 to 16 777 215 [µs]
MP1511.0
X axis
MP1511.1
Y axis
MP1511.2
Z axis
MP1511.3
4th axis
MP1511.4
5th axis