2 servo positioning in tnc controls, 1 control with servo lag – HEIDENHAIN TNC 407 (243 020) Technical Manual User Manual
Page 191
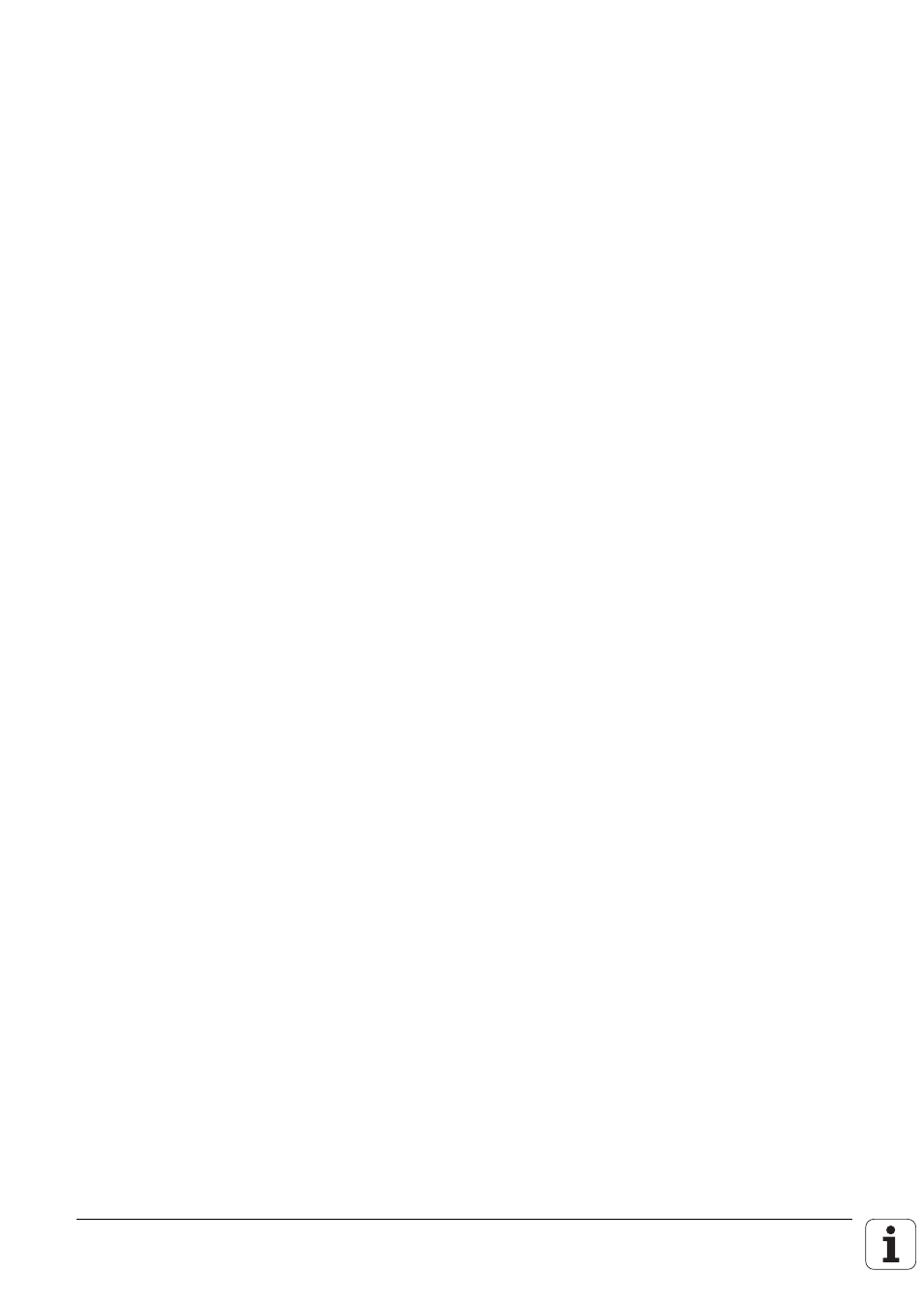
3 Servo positioning of the NC-axes
01.98
3.2 Servo positioning in TNC controls
Two control methods are possible with the control. They can be used alternatively.
1. control with lag (Section 3.2.1)
2. control with feedforward control (Section 3.2.2)
The choice of control method is determined by machine parameters MP1390 and MP1391.
The machine adjustment must always be carried out for both methods of control.
MP1390
Velocity feedforward control in the operating modes "Positioning with MDI",
"Program run, single block", and "Program run, full sequence"
Input:
0 or 1
0 = operation with feedforward control
1 = operation with servo lag
MP1391
Velocity feedforward control in the operating modes "Manual" and "Handwheel"
Input:
%xxxxx
Bit 0
Axis X
0 =
operation with servo lag
Bit 1
Axis Y
1 =
operation with feedforward control
Bit 2
Axis Z
Bit 3
Axis 4
Bit 4
Axis 5
3.2.1 Control with servo lag
Servo lag refers to the difference (lag) between the nominal position which is defined by the NC and
the actual position of the axes. Control would not be possible without this lag.
The advantage of operation with servo lag lies in the "softer" control, which is especially suitable for
machining 3D-contours, since corners and radii are smoothed out, depending on the Kv factor
(position loop gain factor) and the machining feed rate.
Depending on how far these "contour errors" can be tolerated, the machine operator or manufacturer
must decide and choose either operation with servo lag or with feedforward control.
Operation with servo lag is depicted in a simplified form in the following block diagram for the X axis.
It shows a part of the cascade control mentioned previously.
All machine parameters which influence the control characteristic are shown here.