2 reference marks – HEIDENHAIN TNC 407 (243 020) Technical Manual User Manual
Page 177
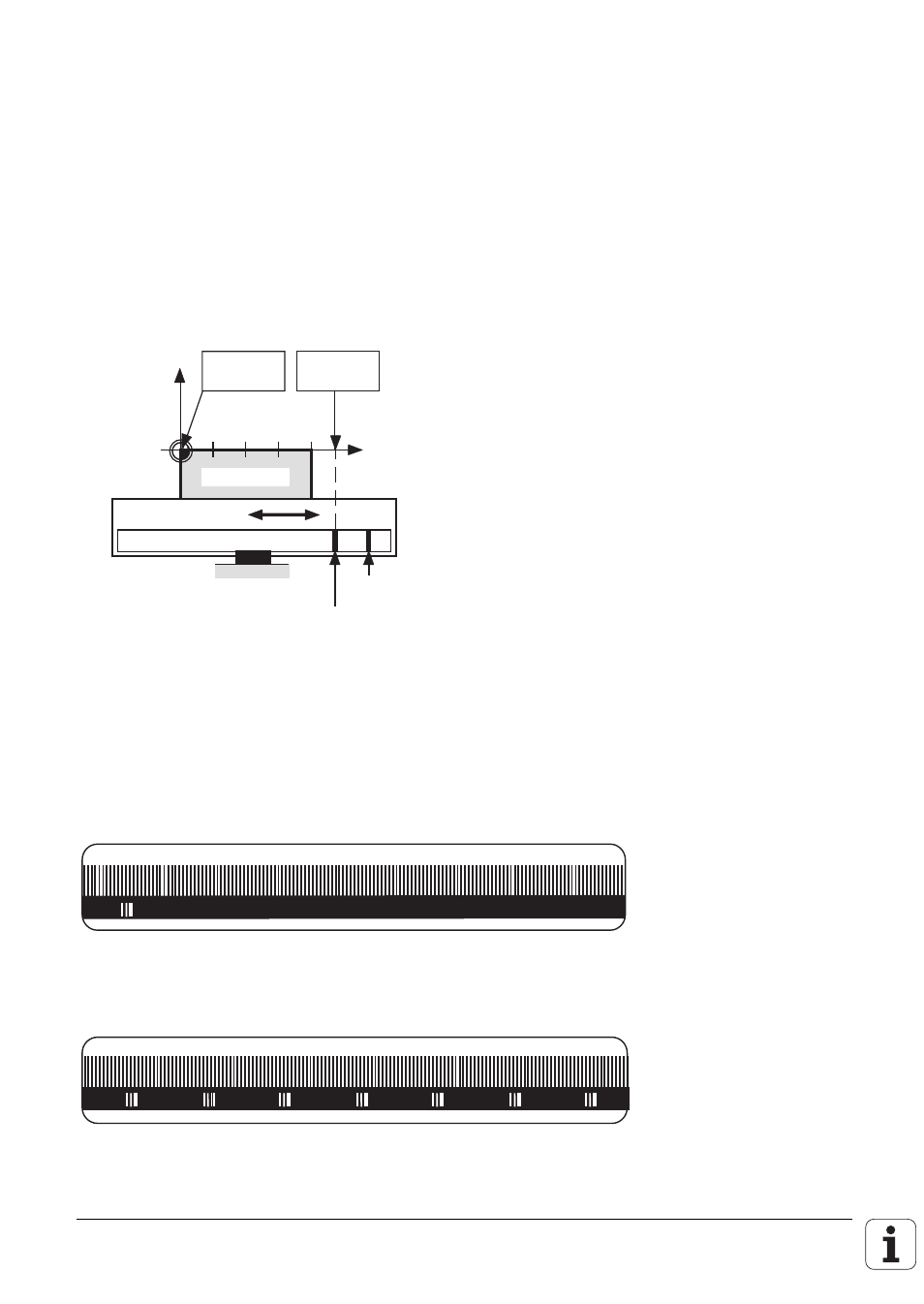
4-52
TNC 407/TNC 415/TNC 425
2 Reference marks
01.98
4
2 Reference marks
By setting a datum point, a definite positional value (coordinate) is assigned to each axis position for
the machining of the workpiece. Since the actual-position value is established incrementally by the
measuring system, this correlation between axis positions and positional values must be re-
established after every power interruption.
The HEIDENHAIN linear measurement systems are therefore equipped with one or more reference
marks. On passing a reference mark a signal is generated which identifies the particular position as a
reference point. By passing over the reference marks after a power interruption, the relationships
between the axis positions and positional values (and, at the same time, the fixed machine
relationships) which were most recently determined by the datum point setting are re-established.
Position encoder
Machine table
REF value
0
10 20 30 40
Machine datum
+Z
+X
0
Workpiece
datum
Workpiece
Reference mark
REF value
–44.985
Since it is often inconvenient to re-establish the reference points by traversing large distances after
switching on, HEIDENHAIN recommends the use of measuring systems with distance-coded
reference marks. With this kind of measuring system the absolute position is available after crossing
two reference marks.
Scale with distance-coded reference marks
The scale graduation consists of the line grating and a reference mark track which runs parallel to it.
The distances between any two consecutive reference marks are defined differently, so that the
absolute position of the machine slide can be determined from this distance.
Scale with distance-coded reference marks
Scale with one reference mark