Control valve settings, Liquid product control valve configuration options, Liquid product – Ag Leader InSight Ver.8.0 Users Manual User Manual
Page 287
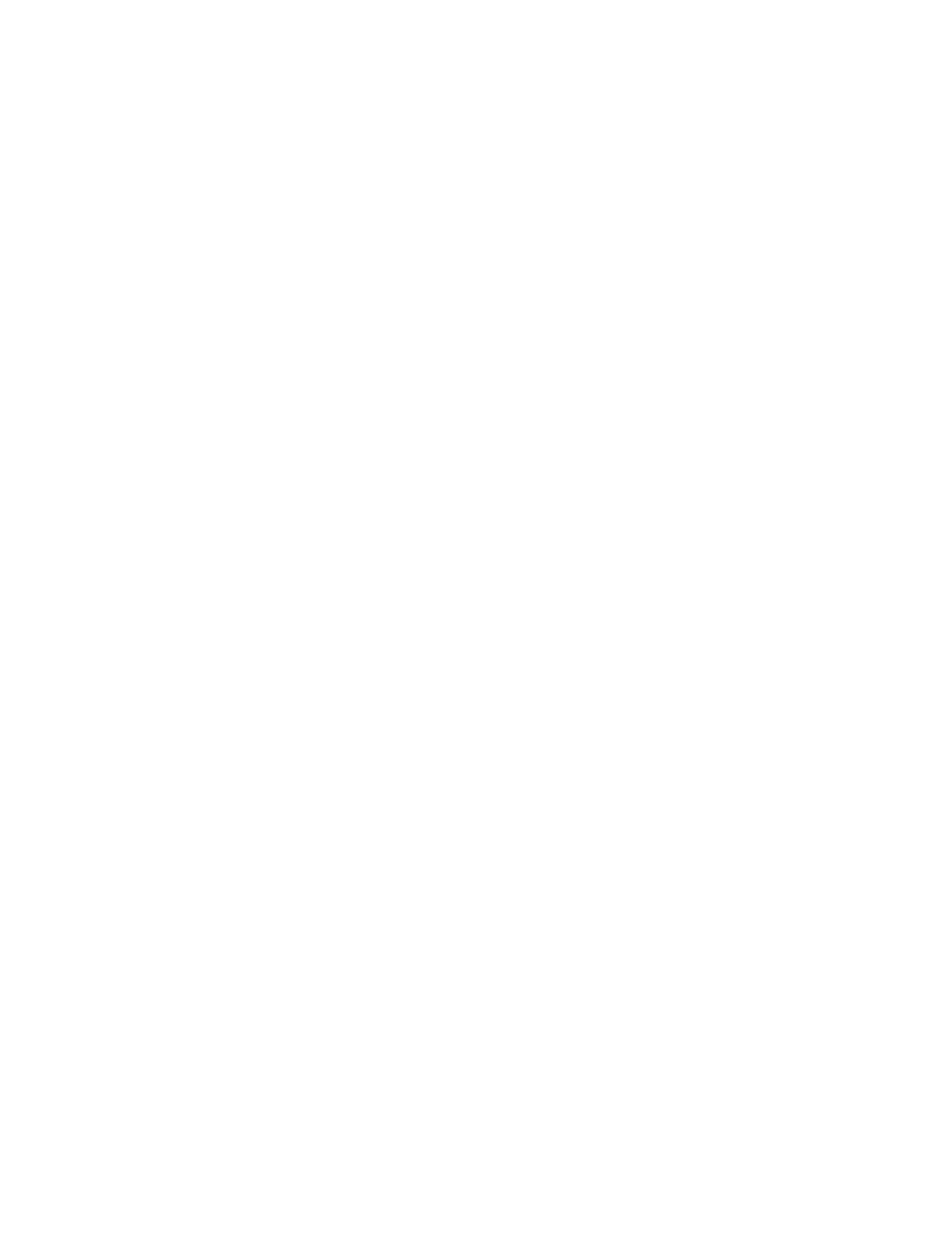
273
A
PPLICATION
1. Enter a target rate into the display
2. Turn the foot pedal master switch on
3. Turn all boom switches on
4. Boom indicators on the display Run Screen must be blue showing that boom valves are on
C
ONTROL
V
ALVE
S
ETTINGS
Liquid Product Control Valve Configuration Options
There are six different common ways of controlling liquid product application, which can be accessed
under the Control Valve Configuration list on the Controller Settings window, which is shown on
DirectCommand Controller Settings” on page
• Inline Servo
Rate control is achieved through actuating a butterfly or ball valve found in the solution hose that goes to
the booms. When the valve opens, the flow increases and when the valve closes, the flow decreases.
• Bypass Servo
Rate control is achieved through actuating a butterfly or ball valve found in the return line to the solution
tank. When the valve opens, the flow decreases and when the valve closes the flow increases.
• PWM 12 volt
Rate control is achieved through speed changes to the solution pump. The PWM 12 Volt setting is
programmed to pulse the power to an electric solenoid valve used to adjust the hydraulic flow to the solution
pump.
• Pump Servo
Rate control is achieved through speed changes to the solution pump. The pump servo setting is
programmed to control an electric motor used to actuate a hydraulic valve to adjust the hydraulic flow to the
solution pump.
• PWM Ground
Rate control is achieved through speed changes to the solution pump. The PWM Ground setting is
programmed to pulse the ground to an electric solenoid valve used to adjust the hydraulic flow to the
solution pump.
• Calibrated Reflow
Three-way boom valves are used to return product back to the tank in the off state. The returned flow is
calibrated with adjustment at each valve. Calibration is required any time the nozzles are changed.