3 position control, 1 prerequisites for position control, Overview of position control – Yaskawa MP940 User Manual
Page 430
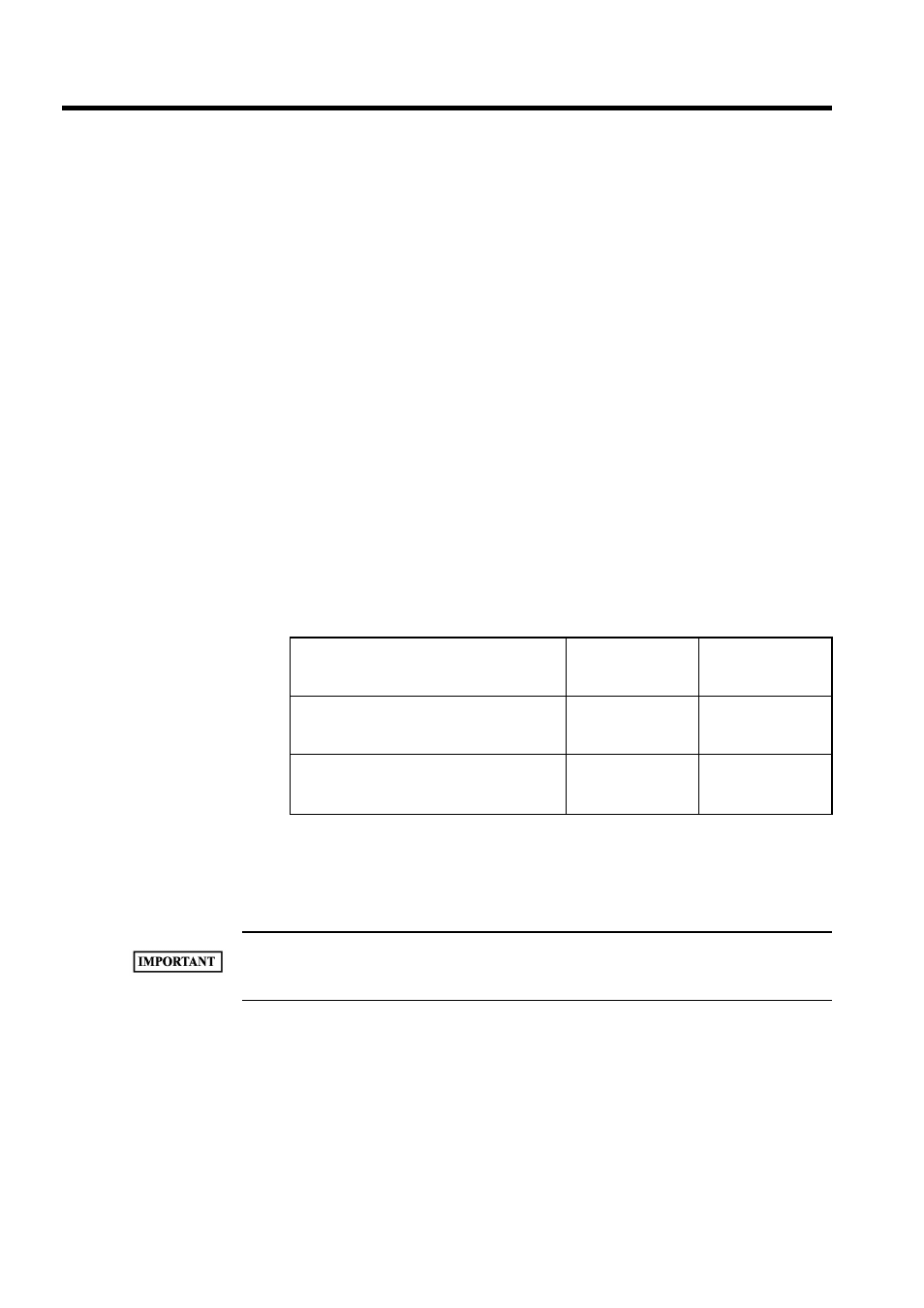
Motion Control
11.3.1 Prerequisites for Position Control
11-28
11.3 Position Control
This section describes the prerequisites for position control, and position control without using
motion commands.
11.3.1 Prerequisites for Position Control
Overview of Position Control
With position control, the axis is moved to the target position, stops there, and holds that
position (servo clamp).
An incremental encoder or a Yaskawa absolute encoder is used as the position detector.
When a Yaskawa absolute encoder is used, the absolute position is stored, even when the
power for the machine (positioning device) is disconnected. Therefore, when the power is
turned ON again, the zero point return operation is not required.
There are two position control methods. One method uses motion commands (OWC020),
and the other method does not use motion commands.
Whether or not motion commands (OWC020) are to be used is set in the motion parameters
shown in the following table.
Note: When bit 7 (motion command selection) of motion fixed parameter
No. 14 (Additional Function Selections) is not selected for use and bit
8 (motion command code enable) of the RUN Mode Settings
(OWC000) motion setting parameter is set to “1” (= enabled), the
axis is controlled without motion commands (OWC020).
Be sure to set the motion set parameter OWC001 bit 14 (Position Reference Type) to l ( = incremental
addition mode) when using the motion program.
Motion Parameter
Motion Command
(OWC020) Not
Used
Motion Command
(OWC020) Used
Motion fixed parameter No. 14
Bit 7 of Additional Function Selections
(Motion Command Selection)
0 (= Not used)
1 (= Used)
Motion setting parameter
Bit 8 of RUN Mode Settings (OWC000)
(Motion Command Code Enable/Disable)
0 (= Disabled)
1 (= Enabled)