Yaskawa MP940 User Manual
Page 418
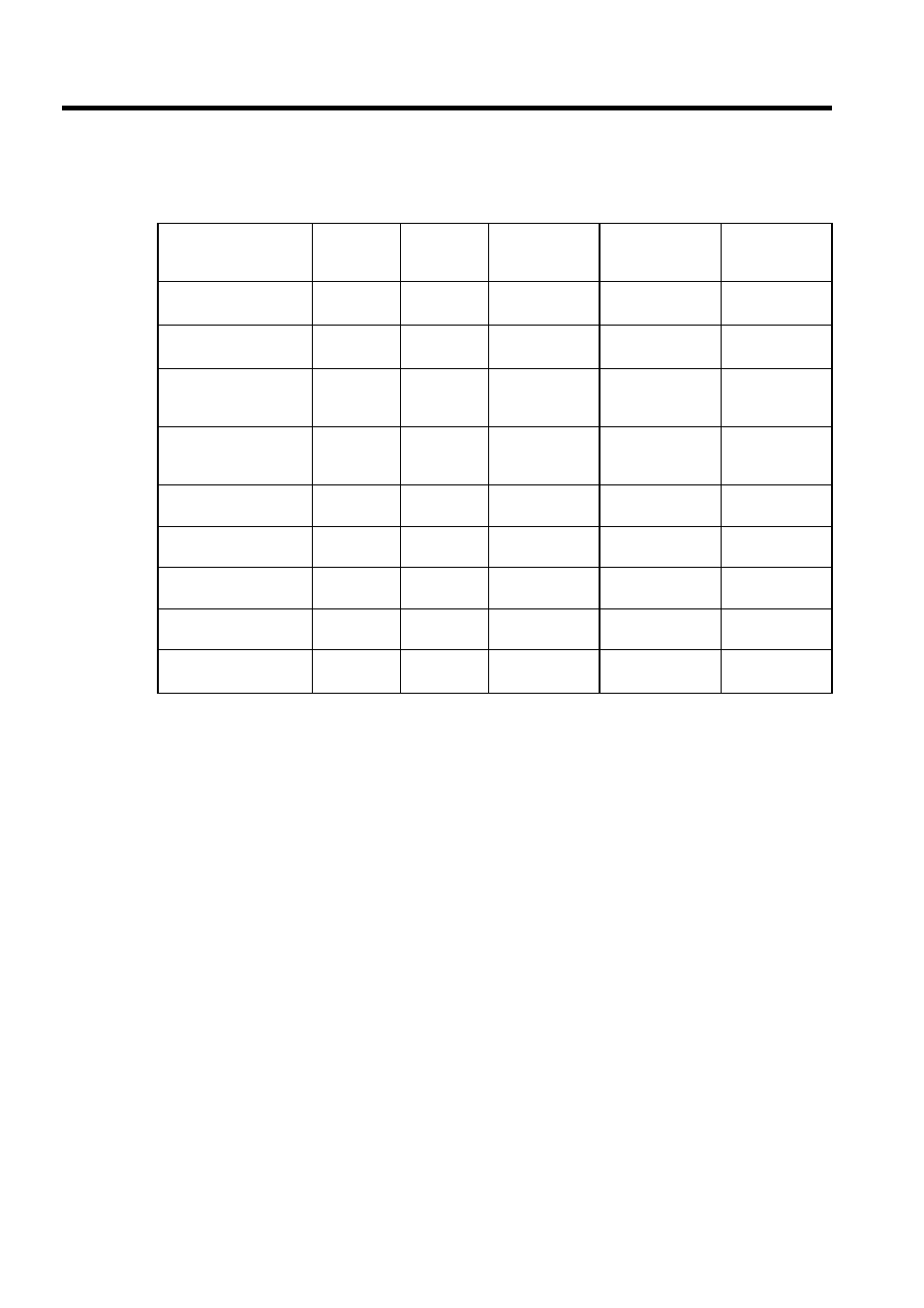
Motion Control
11.2.4 Phase Control Mode
11-16
The following table shows the related parameters when the phase control mode is used.
Table 11.3 Examples of Setting Parameters
2. Select the Phase Control Mode (PHCON) (bit 3 of OWC000).
At this time, also set Phase Reference Disable (PHREFOFF: bit 7 of OWC000). Nor-
mally, this bit is set to OFF for electronic shaft applications, and it is set to ON for elec-
tronic cam applications.
3. Set the Servo ON (RUN) to ON (bit 0 of OWC001).
Phase control will be performed for the axis according to the specified motion parame-
ters.
Even while phase control is being performed, the motion parameter settings can be
changed.
4. To stop operation, set the RUN command (RUN) and the phase control mode (PHCON)
to OFF.
Name
Register No.
Setting
Range
Meaning
Electronic Shaft
Setting Example
Electronic Cam
Setting
Example
Positive Torque Limit
Setting (TLIMP)
OWC002
-327.68 to
327.67
0.01 = 0.01%
1 = 1%
-100.00
(-100.00%)
-100.00
(-100.00%)
Positive Speed Limiter
Setting (NLIMP)
OWC004
0.00 to
327.67
0.01 = 0.01%
1 = 1%
130.00
(130.00%)
130.00
(130.00%)
Negative Speed
Limiter Setting
(NLIMN)
OWC005
0.00 to
327.67
0.01 = 0.01%
1 = 1%
130.00
(130.00%)
130.00
(130.00%)
Error Count Alarm
Detection Setting
(EOV)
OWC00F
0 to 65535
1 = 1 pulse
65535
65535
Speed Reference
Setting (NREF)
OWC015
-327.68 to
327.67
0.01 = 0.01%
1 = 1%
50.00 (50.00%)
Set by the ladder
logic program
Phase Bias Setting
(PHBIAS)
OLC016
-2
31
to 2
31
-1
1 = 1 pulse
Set by the ladder
logic program
Set by the ladder
logic program
Speed Compensation
Setting (NCOM)
OWC018
-327.68 to
327.67
0.01 = 0.01%
1 = 1%
0.00
0.00
Proportional Gain
Setting (PGAIN)
OWC019
0.0 to 3276.7 0.1 = 0.1 /s
1 = 1 /s
1.5
(1.5)
250.0
(250.0)
Integral Time Setting
(TI)
OWC01A
0 to 32767
1 = 1 ms
300
(300 ms)
0
(0 ms)