Commissioning status attributes, Test status – Rockwell Automation 1784-PM16SE SoftLogix Motion Card Setup and Configuration Manual User Manual
Page 377
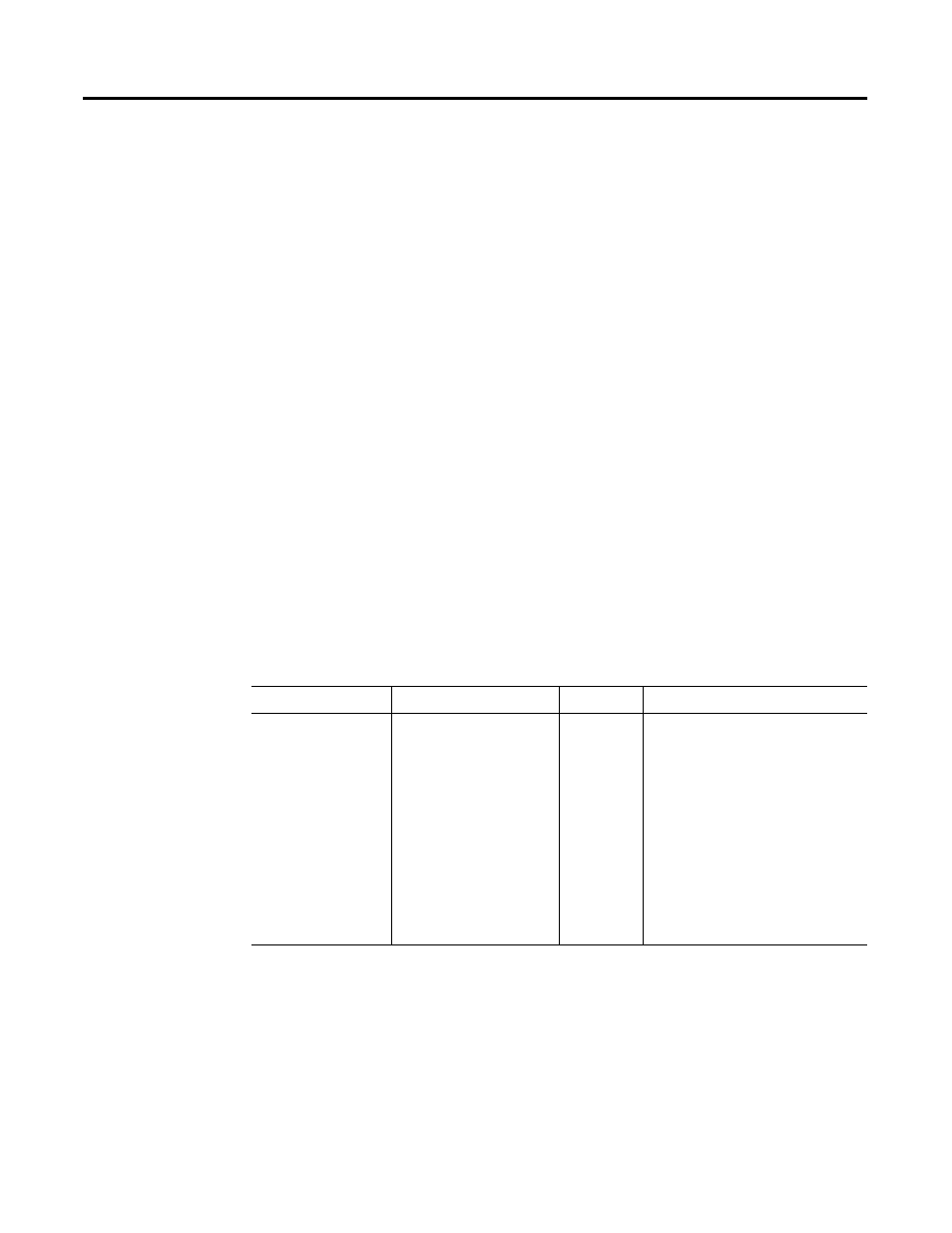
Publication 1784-UM003A-EN-P – June 2003
Motion Object Attributes 369
Commissioning Status
Attributes
The list of Commissioning Status Attributes associated with the Axis Object
provides access to attributes associated with the state of various motion
instruction generated commissioning processes. Motion instructions involved
in commissioning an axis are MRAT (Motion Run Axis Tune) and MRHD
(Motion Run Hookup Diagnostic) which are described in detail in the AC
Motion Instruction Specification. Commissioning Status Attributes are
primarily used by external software (e.g. RSLogix 5000) to implement the Test
and Tuning dialogs associated with the axis configuration tool. However, these
same attributes may also be used as part of the user program to implement a
“built-in” axis test and tuning procedure.
In order for position unit-based attributes to return a meaningful value, the
‘Conversion Constant’ Axis Configuration Attribute must be established.
Furthermore, attributes having time units (Position Units / Sec) must also
have a valid coarse update period which is established through association with
a fully configured Motion Group Object.
Test Status
The Test Status attribute returns status of the last run MRHD (Motion Run
Hookup Diagnostic) instruction that initiates a hookup diagnostic process on
the targeted SERCOS module axis. The Test Status attribute can, thus, be used
to determine when the MRHD initiated operation has successfully completed.
Conditions may occur, however, that make it impossible for the control to
properly perform the operation. When this is the case, the test process will be
automatically aborted and a test fault reported that is stored in the Test Status
output parameter. .
GSV/SSV Access
Attribute Name
Data Type
Values
GSV
Test Status
INT
0 = test process successful
1 = test in progress
2 = test process aborted by user
3 = test process time-out fault (~2
seconds)
4 = test failed – servo fault
5 = test failed – insufficient test
increment
6 = test failed – wrong polarity
7 = test failed – missing signal
8 = test failed – device comm error
9 = test failed – feedback config error
10 = test failed – motor wiring error