Motion conversion configuration, Conversion constant – Rockwell Automation 1784-PM16SE SoftLogix Motion Card Setup and Configuration Manual User Manual
Page 296
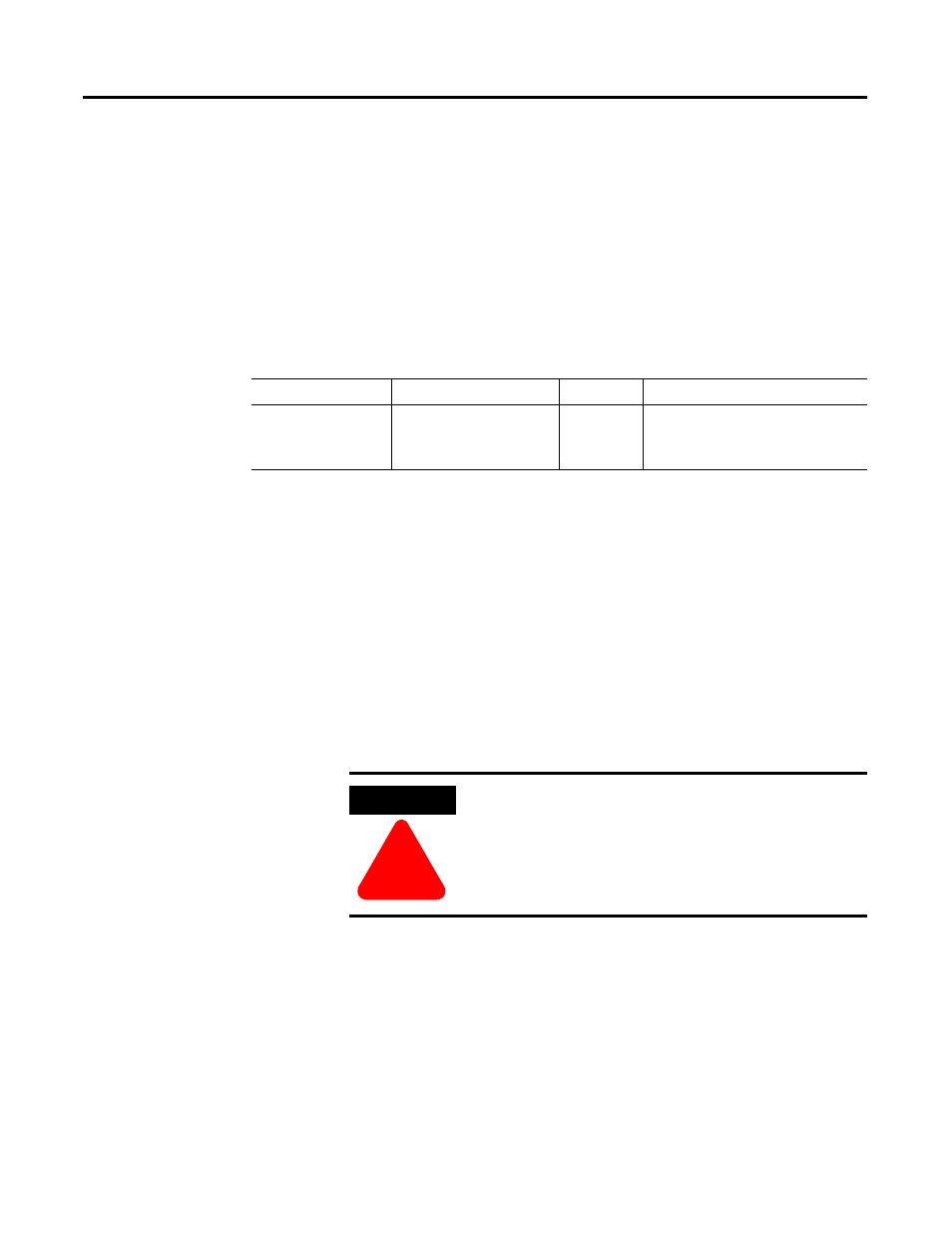
Publication 1784-UM003A-EN-P – June 2003
288 Motion Object Attributes
Motion Conversion
Configuration
Conversion Constant
To allow axis position to be displayed and motion to be programmed in the
position units specified by the Position Unit string attribute, a Conversion
Constant must be established for each axis. The Conversion Constant,
sometimes known as the K constant, allows the Axis Object to convert the
axis position units into feedback counts and vice versa. Specifically, K is the
number of feedback counts per Position Unit.
Note that the 1784-PM02AE encoder based servo module uses 4X encoder
feedback decoding (both edges of channel A and B are counted). The count
direction is determined from both the direction of the edge and the state of
the opposite channel. Channel A leads channel B for increasing count. This is
the most commonly used decode mode with incremental encoders, since it
provides the highest resolution.
For example, suppose this servo axis utilizes a 1000 line encoder in a motor
coupled directly to a 5 pitch lead screw (5 turns per inch). With a user defined
Position Unit of Inches, the conversion constant is calculated as shown below:
K = 1000 Lines/Rev * 4 Counts/Line * 5 Revs/Inch = 20,000
Counts/Inch.
GSV/SSV Access
Attribute Name
Data Type
Values
SSV/GSV
Conversion Constant
REAL
Counts / Position Unit
Range: 0.1 - 1e
12
Default: 8000.0
ATTENTION
!
If ‘Conversion Constant’ is changed it invalidates all of the
settable attributes with “Position Unit” conversions in
“Values” column. To be valid the ‘Conversion Constant’
must be set to the desired value prior to setting (including
defaulting) any of the affected attributes.