Position lock tolerance, Manual adjust – Rockwell Automation 1784-PM16SE SoftLogix Motion Card Setup and Configuration Manual User Manual
Page 162
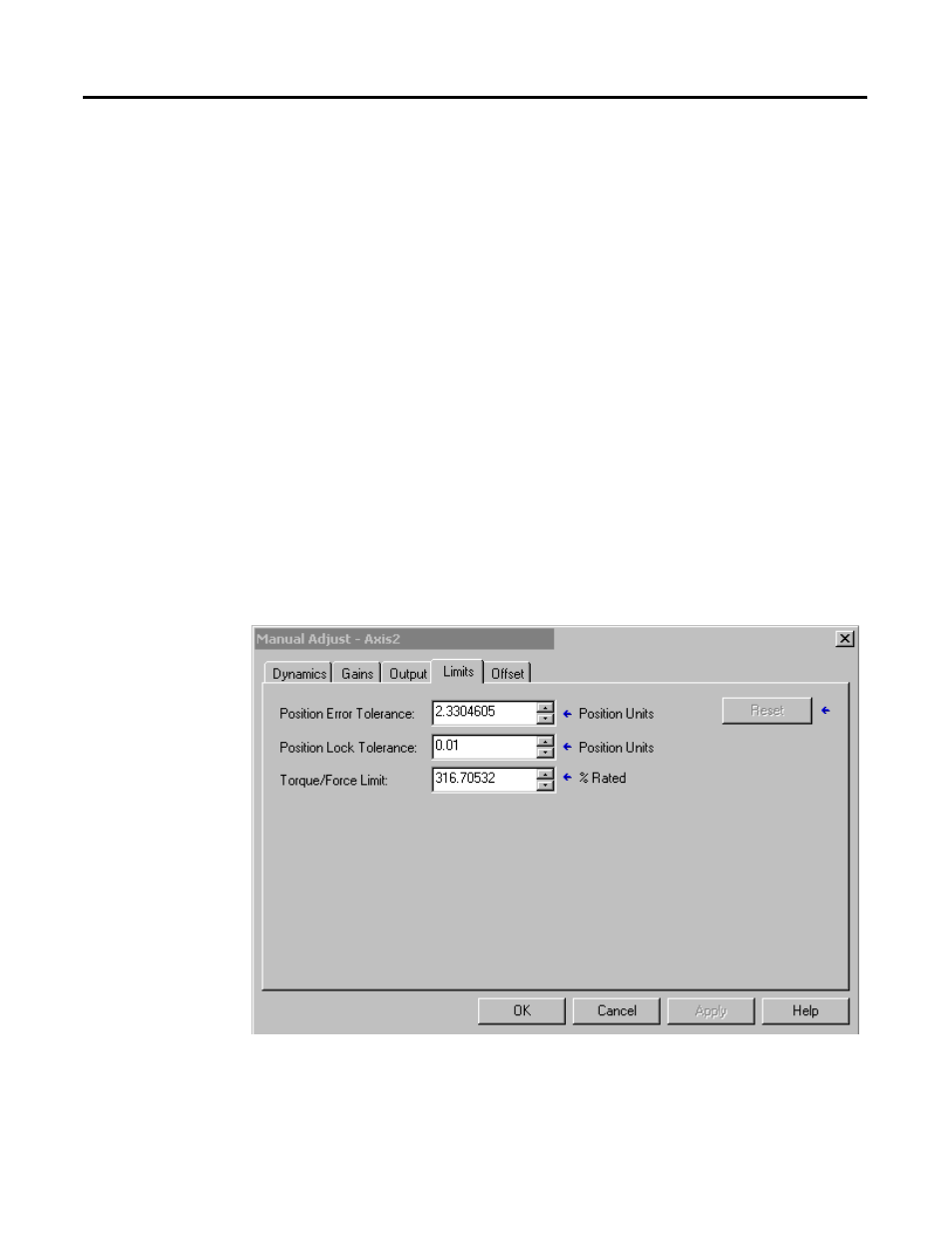
Publication 1784-UM003A-EN-P – June 2003
154 Naming & Configuring Your Motion Axis
Note: This value is set to twice the following error at maximum speed
based on the measured response of the axis, during the autotuning
process. In most applications, this value provides reasonable protection
in case of an axis fault or stall condition without nuisance faults during
normal operation. If you need to change the calculated position error
tolerance value, the recommended setting is 150% to 200% of the
position error while the axis is running at its maximum speed.
Position Lock Tolerance
Specifies the maximum position error the servo module accepts in order to
indicate the Position Lock status bit is set. This is useful in determining when
the desired end position is reached for position moves. This value is
interpreted as a +/- quantity.
For example, specifying a lock tolerance of 0.01 provides a minimum
positioning accuracy of +/- 0.01 position units, as shown here:
Manual Adjust
Click on this button to open the Limits tab of the Manual Adjust dialog for
online editing of the Position Error Tolerance, Position Lock Tolerance, and
Output Limit parameters.
Figure 6.38 Axis Properties - Limits Tab for Axis_Servo_Drive
Note: The Manual Adjust button is disabled when RSLogix 5000 is in
Wizard mode, and when offline edits to the above parameters have not
yet been saved or applied.