Friction compensation, Velocity offset, Torque offset – Rockwell Automation 1784-PM16SE SoftLogix Motion Card Setup and Configuration Manual User Manual
Page 166
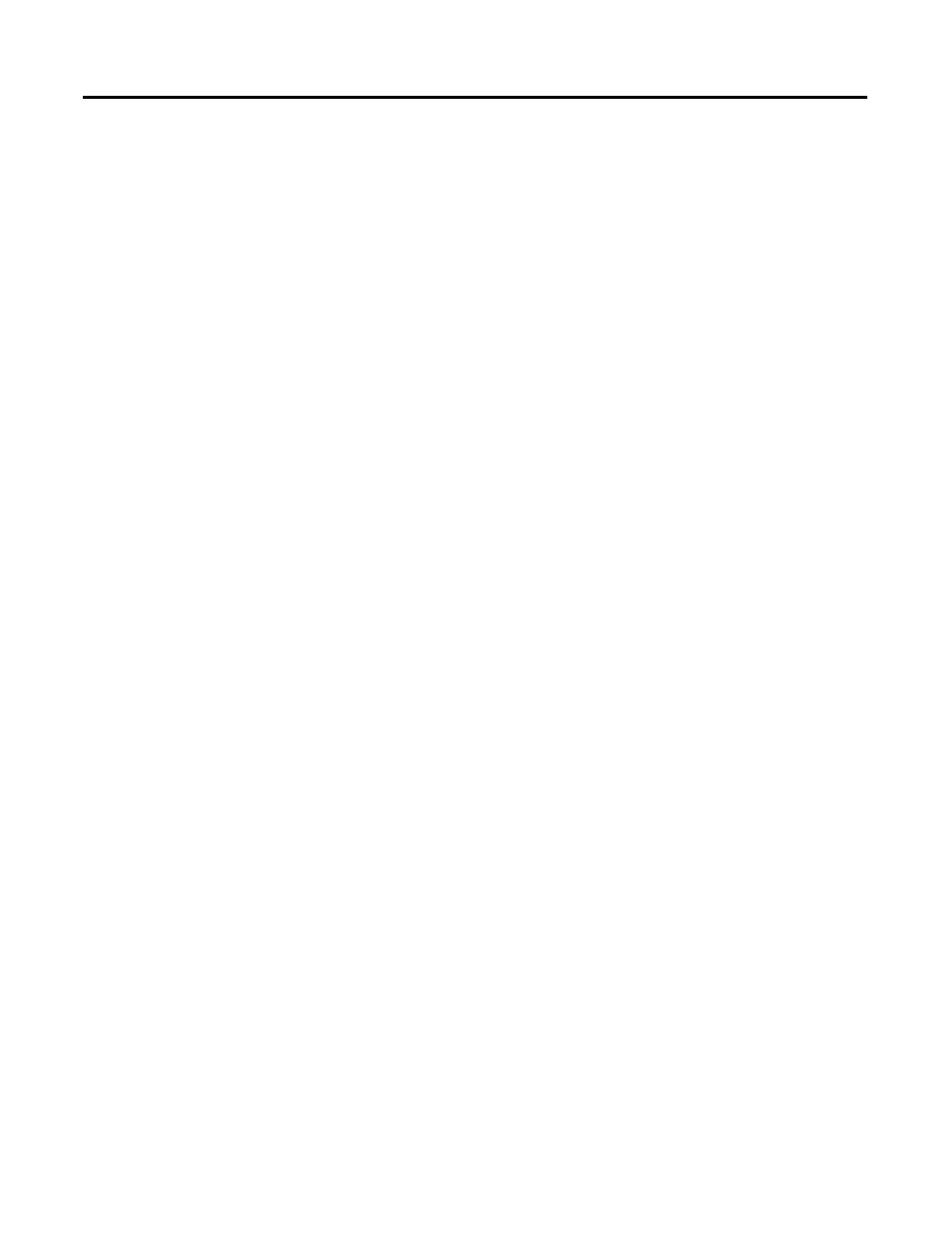
Publication 1784-UM003A-EN-P – June 2003
158 Naming & Configuring Your Motion Axis
When RSLogix 5000 is offline, the following parameters can be edited and the
program saved to disk using either the Save command or by clicking on the
Apply button. You must re-download the edited program to the controller
before it can be run.
Friction Compensation
The percentage of output level added to a positive current Servo Output value,
or subtracted from a negative current Servo Output value, for the purpose of
moving an axis that is stuck in place due to static friction.
It is not unusual for an axis to have enough static friction (called “sticktion”)
that, even with a significant position error, the axis refuses to budge. Friction
Compensation is used to break “sticktion” in the presence of a non-zero
position error. This is done by adding, or subtracting, a percentage output
level), called Friction Compensation to the Servo Output value.
The Friction Compensation value should be just less than the value that would
break the “sticktion”
A larger value can cause the axis to “dither”, i.e. move rapidly back and forth
about the commanded position.
Velocity Offset
Provides a dynamic velocity correction to the output of the position servo
loop, in position units per second. Because the position servo loop output
value is updated synchronously every Coarse Update Period, the Velocity
Offset can be tied into custom outer control loop algorithms using Function
Block programming.
Torque Offset
Provides a dynamic torque command correction to the output of the velocity
servo loop, as a percentage of velocity servo loop output. Because velocity
servo loop output is updated synchronously every Coarse Update Period, the
Torque Offset can be tied into custom outer control loop algorithms using
Function Block programming.