Positive/negative software overtravel faults, Positive/negative hardware overtravel faults, Position error fault – Rockwell Automation 1784-PM16SE SoftLogix Motion Card Setup and Configuration Manual User Manual
Page 370: Feedback 1 or feedback 2 fault
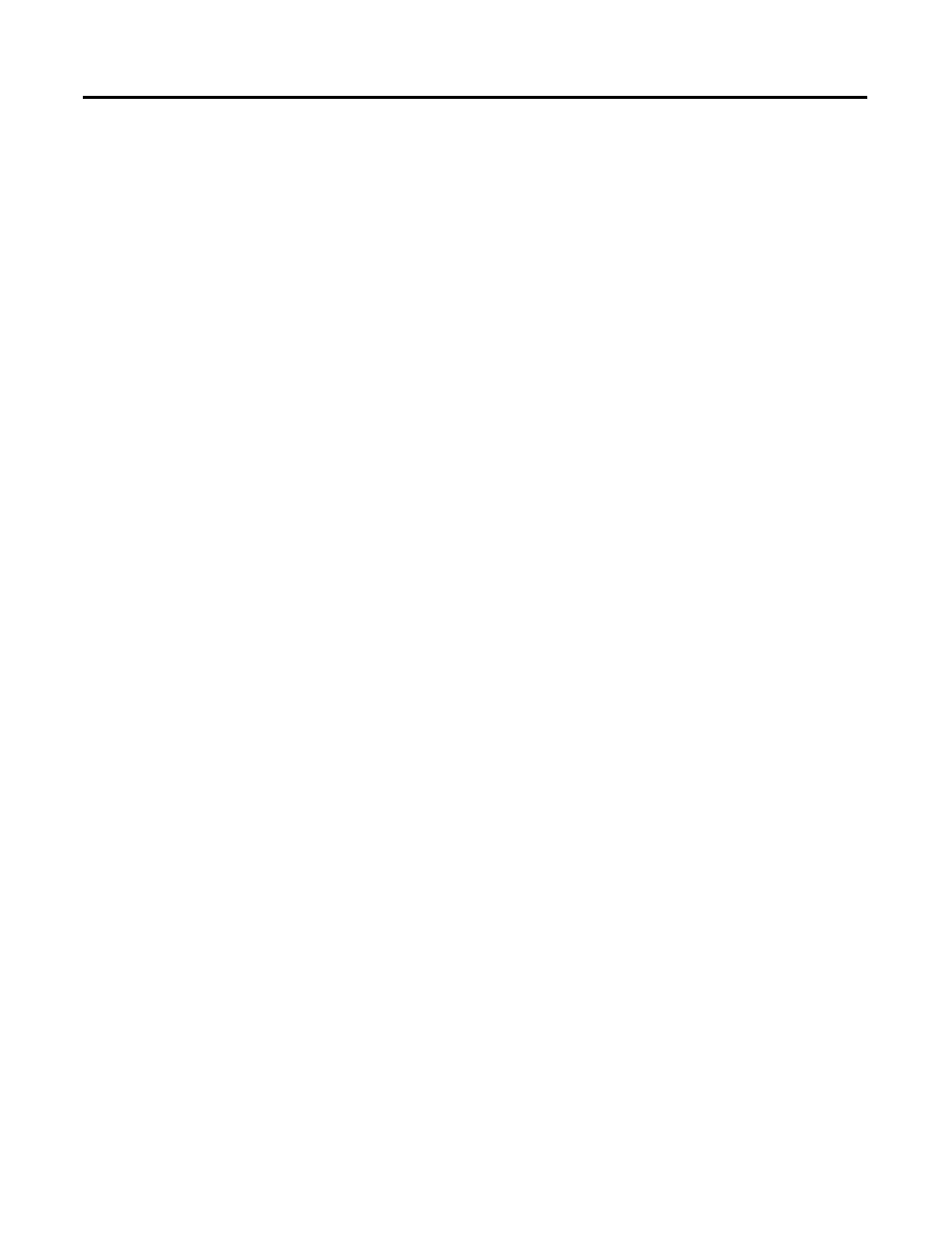
Publication 1784-UM003A-EN-P – June 2003
362 Motion Object Attributes
Positive/Negative Software Overtravel Faults
If either the Positive Soft Overtravel Status or Negative Soft Overtravel Status
bit attributes are set it indicates that the axis has traveled, or attempted to
travel, beyond the current configured values for Maximum Positive Travel or
Maximum Negative Travel, respectively. As soon as the axis is moved back
within these travel limits, the corresponding Overtravel Status bit is cleared.
Positive/Negative Hardware Overtravel Faults
If either the Positive Hard Overtravel Status or Negative Hard Overtravel
Status bit attributes are set it indicates that the axis has traveled beyond the
current position limits as established by hardware limit switches mounted on
the machine. To recover, the axis must be moved back with normal operation
limits of the machine and the limit switch reset. This fault condition is latched
and requires execution of an explicit MAFR (Motion Axis Fault Reset) or
MASR (Motion Axis Shutdown Reset) instruction to clear.
Position Error Fault
If the Position Error Fault bit attribute is set it indicates that the servo has
detected that the axis position error has exceeded the current configured value
for Position Error Tolerance. This fault condition is latched and requires
execution of an explicit MAFR (Motion Axis Fault Reset) or MASR (Motion
Axis Shutdown Reset) instruction to clear.
Feedback 1 or Feedback 2 Fault
If the Feedback Fault bit is set for a specific feedback source, it indicates that
one of the following conditions occurred:
• The differential electrical signals for one or more of the feedback
channels (e.g., A+ and A-, B+ and B-, or Z+ and Z- for an encoder) are
at the same level (both high or both low). Under normal operation, the
differential signals are always at opposite levels. The most common cause
of this situation is a broken wire between the feedback transducer and
the servo module or drive.
• Loss of feedback “power” or feedback “common” electrical connection
between the drive and the feedback device.
This fault condition is latched and requires execution of an explicit MAFR
(Motion Axis Fault Reset) or MASR (Motion Axis Shutdown Reset)
instruction to clear.