Introduction, Appendix c, Appendix c • tuning pid settings – Basler Electric DGC-2020 User Manual
Page 583
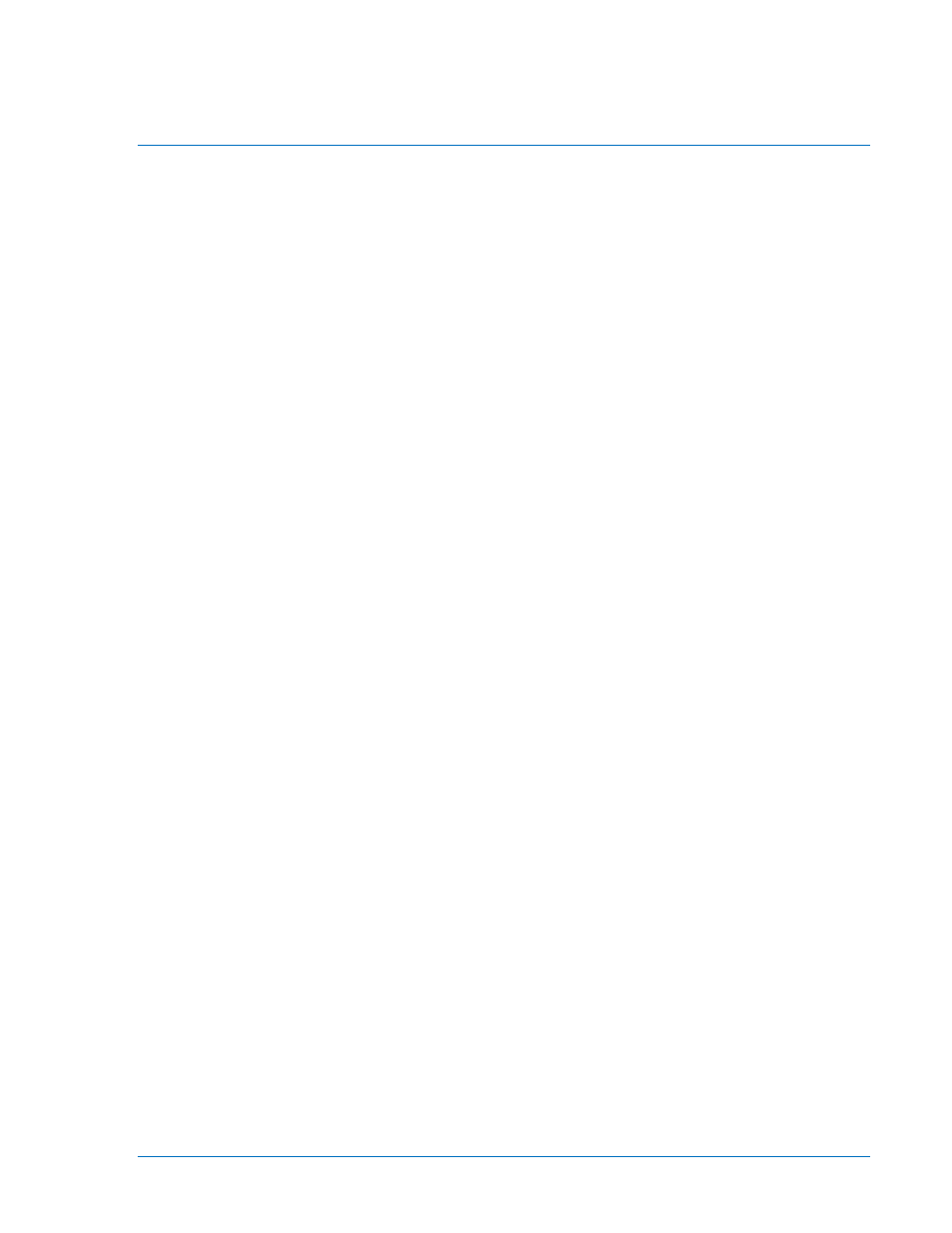
APPENDIX C
• TUNING PID SETTINGS
Introduction
The LSM-2020 (Load Share Module) and DGC-2020 utilize four controllers to accomplish
synchronization, load sharing, reactive power sharing, speed trim, and voltage trim functions. The
controllers are a voltage controller, a var/PF controller, a speed controller, and a kW load controller. The
voltage and speed controllers are in effect when the DGC-2020 is synchronizing the generator to a bus.
When synchronizing, these controllers adjust the speed and voltage output of the generator to match that
of the bus. After the generator is paralleled to a bus that is not connected to utility power, the kW load
controller controls the kW output of the machine to share real power equally on a percentage basis with
the other generators on the bus. All generators participating in load sharing are connected together with
analog load share lines or Ethernet inter-genset communications which are used to communicate load
share information between the machines. When the generator is not paralleled to the utility, the var/PF
controller utilizes inter-genset communications to accomplish reactive power sharing where each machine
shares reactive power equally on a percentage basis with the other generators on the bus. When the
generator is paralleled to the utility, the kW load controller causes the unit to produce wattage at a level
equal to the base load set point. The var/PF controller can operate in either var or PF control mode when
the generator is paralleled to the utility. When operating in var control mode, the machine will produce
reactive power at a level equal to the kvar Setpoint setting. When in PF control mode, the var/PF
controller will regulate the reactive power output of the machine to maintain the power factor specified by
the PF Setpoint setting. The kW base load set point, the kvar set point, and the PF set point can be
derived from either a user setting, or an analog input.
When the generator is paralleled to an islanded bus and load sharing is enabled, the speed trim function,
if enabled in all machines on the bus, will ensure that the bus frequency is maintained at the frequency
set by the speed trim setting. Speed trim is in effect only in the situation where the generator breaker is
closed to an islanded bus and load control and speed trim are enabled. Speed trim is not in effect when
the breaker is open, since the default mode when the breaker is open is droop, and speed trim would
counteract droop. Speed trim is not in effect when the breaker is closed unless load control is enabled.
When load control is enabled, it is possible that integral action in PID controller for kW Load control could
cause the system frequency to drift, and speed trim can be employed to counteract the drift.
When the generator is paralleled to an islanded bus and the kvar controller is enabled to accomplish kvar
sharing, the voltage trim function, if enabled in all machines on the bus, will ensure that the bus voltage of
the system is maintained at a voltage equal to the Rated Voltage Setpoint of the machines. Voltage trim is
in effect only in the situation where the generator breaker is closed to an islanded bus and kvar control
and voltage trim are enabled. Voltage trim is not in effect when the breaker is open, since the default
mode when the breaker is open is droop, and voltage trim would counteract droop. Voltage trim is not in
effect when the breaker is closed unless kvar control is enabled. When kvar control is enabled, it is
possible that integrator action in PID controller for kvar control could cause the system voltage to drift,
and voltage trim can be employed to counteract the drift.
The load share module utilizes PID (Proportional, Integral, Derivative) Control to accomplish kW and kvar
load sharing, speed control, and voltage control. A brief description of the three 3 main tuning parameters,
and their effects on system behavior, is presented below.
•
K
p
- Proportional Gain - The proportional term makes a change to the output that is proportional to
the current error value. The proportional response can be adjusted by multiplying the error by a
constant K
p
, called the proportional gain. Larger K
p
typically means faster response since the
larger the error, the larger the feedback to compensate. An excessively large proportional gain
will lead to process instability.
•
K
i
- Integral Gain - The contribution from the integral term is proportional to both the magnitude of
the error and the duration of the error. Some integral gain is required in order for the system to
achieve zero steady-state error. The integral term (when added to the proportional term)
accelerates the movement of the process towards the set point and eliminates the residual
steady-state error that occurs with a proportional only controller. Larger K
i
implies steady state
errors are eliminated more quickly. The tradeoff is larger overshoot: any negative error integrated
during transient response must be integrated away by positive error before reaching steady state.
•
K
d
- Derivative Gain - The derivative term slows the rate of change of the controller output and is
used to reduce the magnitude of the overshoot produced by the integral component and improve
9400200990 Rev X
DGC-2020 Tuning PID Settings
C-1