Festo Кабели и принадлежности User Manual
Page 325
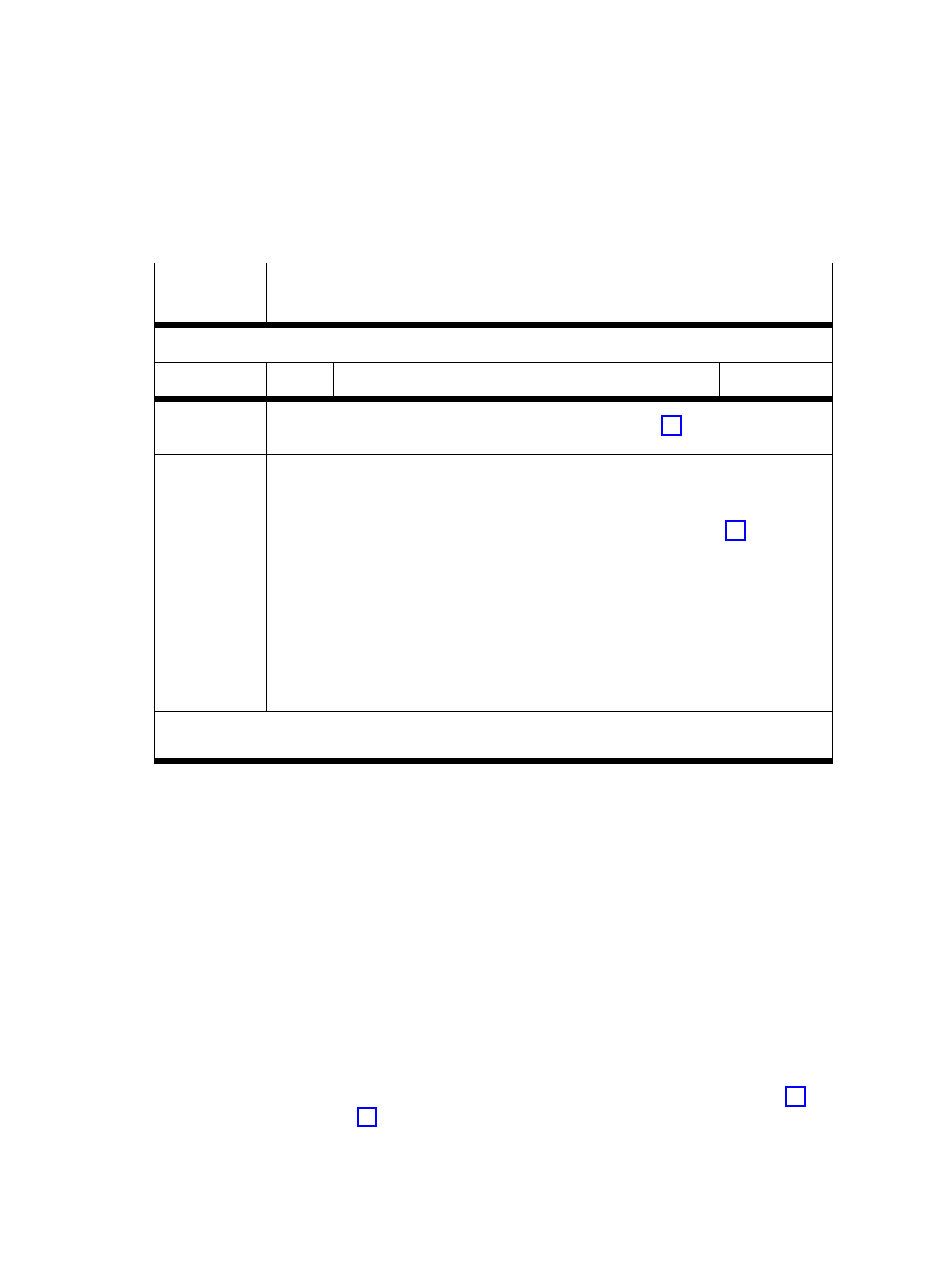
7. Description of the commands
7−59
Festo P.BE−SPC200−EN en 0901d
G74
Start reference travel
1)
ć pneumatic axis; ć permitted in operating mode: Start/Stop, Record Select
Nn G74 X
n
Reference travel mode
n = 0, 5, 6, 7
Effect
Starts reference travel of the axis in the mode specified (see Fig. 7/15).
After successful reference travel the status flag REF is set.
Example
N000 G74 X5
;Move to reference point, direction:
;retracted piston rod"
Remark
Ĉ Defining the reference point and the reference position see chapter 3.4.
Ĉ The reference mode is defined in the application data when each pneumatic axis
is configured. If a different mode is selected with command G74, fault zzz1Ax06
will be generated (zzz = program line, x = axis number) at the beginning of the
execution of the command. Exception: Reference travel mode 7 can always be
used irrespective of the definition in the application data.
Ĉ If the modes 1, 2, 3 and 4 are activated for a pneumatic axis, fault zzz1Ax06 will
be generated (zzz = program line, x = axis number).
Ĉ A pneumatic axis cannot execute positioning commands without successful
reference travel. Exception: NC command M39 or reference travel with mode 7.
1)
This function is only effective as from operating system version 4.82. It is not supported by the
control panel.
In the case of a pneumatic axis with an incremental measurĆ
ing system, referencing is always carried out against a fixed
stop. Depending on its position, it will be approached from
the left or the right. This stop can be fitted externally or it can
be the end stop of the cylinder itself.
The reproducibility of the reference point depends exclusively
on the accuracy of the stop.
For commissioning, the offset of the reference position and
reference travel mode must be defined in the application
data. The offset reference position specifies the offset of the
axis zero point from the reference point. It is always a posiĆ
tive variable. This offset value also influences the controller
optimization of the SPC200, even small values (a few mm)
must be specified as accurately as possible (see chapter 3.4,
Fig. 3/5).