Festo Кабели и принадлежности User Manual
Page 231
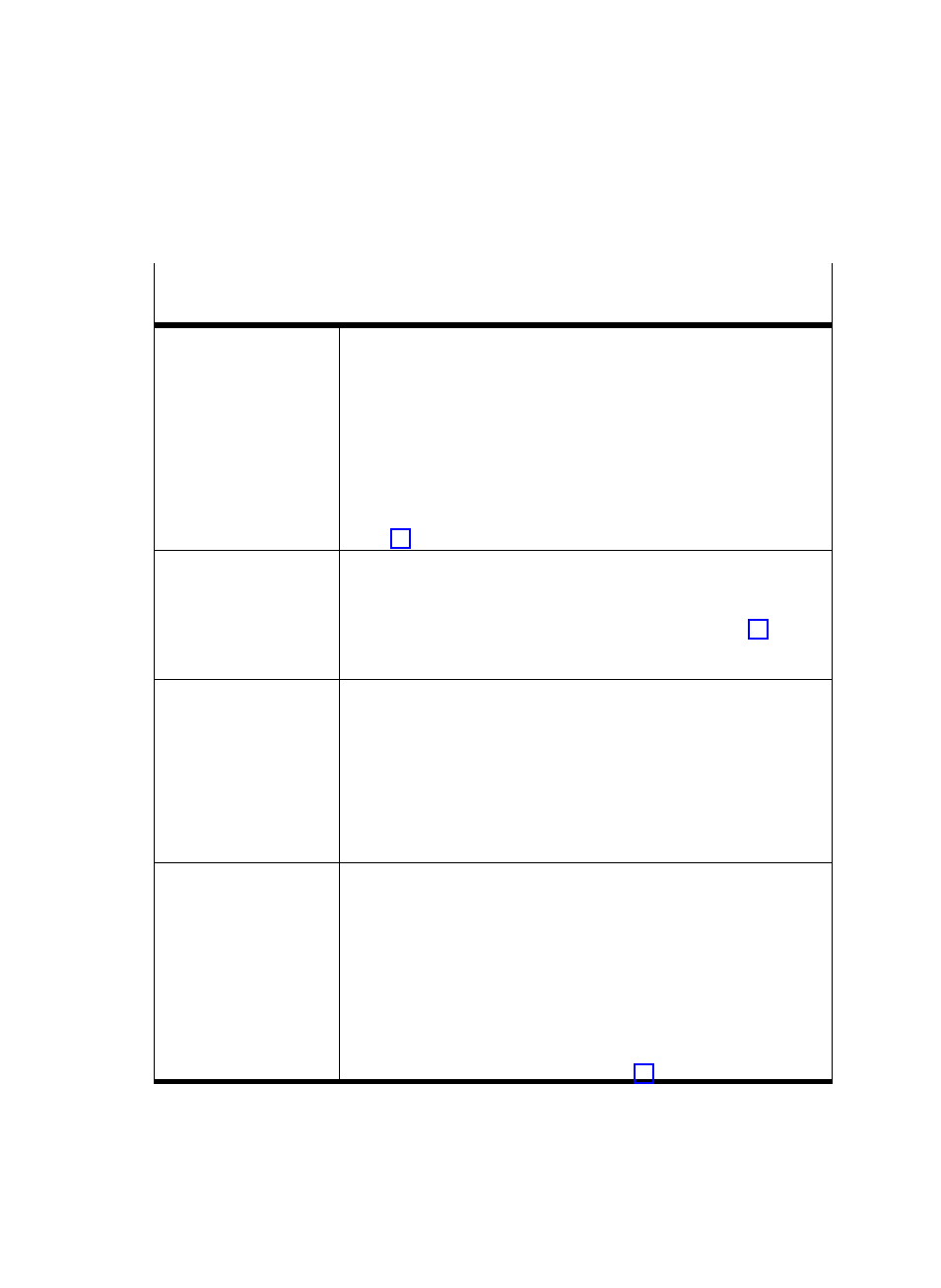
6. Operating the SPC200 with the control panel
6−19
Festo P.BE−SPC200−EN en 0901d
Menu APPLIC. PARAM (application data)
Pneumatic axis
TOOL LOAD
X:+0000.00
Total mass to be moved by the positioning axis, or mass moment of
inertia, in each case without the workpiece.
0.1 ... 2000 [kg] or [kgm
2
* 10
−4
]
In the case of the pneumatic axis describes the total weight or the mass
moment of inertia of the following components:
Ĉ slide and piston
Ĉ fastening plate
Ĉ Tool
The maximum permissible total load and the maximum permissible
total mass moment of inertia depends on the drive type used, see
chapter 3.2.9.
WORK LOAD
X:+0001.00
Maximum mass or mass moment of inertia of the workpiece
0 ... 2000 [kg] or [kgm
2
* 10
−4
]
You can modify this value via the control panel, if at the same time the
Workpiece mass in initial state" is also modified, see chapter 3.2.9.
Recommendation: Use NC command M37 if you wish to position with
different loads.
PRESSURE
X:+0000.00
Supply pressure
3 ... 10 bar
Specifies the prepared supply pressure. For good positioning
behaviour:
Ĉ fluctuations in pressure of max. 1 bar in front of the proportional
directional control valve during positioning
Ĉ minimum supply pressure 4 bar.
Please note the permitted pressure range of the components used
(e.g. DGP...−... max. 8 bar).
FITTING POS.
X:+00
Mounting position
In the case of linear drives and drives with piston rod: −90 ... +90 [
°]
In the case of the rotary module: Parameter is not evaluated.
In the case of linear drives and drives with piston rod specifies the
mounting position and the direction in which the drive and the measurĆ
ing system should preferably be fitted.
− 0
° horizontally
+ 90
° vertically upwards (zero of measuring system at bottom)
− 90
° vertically downwards (zero of measuring system at top)
In the case of the rotary module the parameter is not evaluated
(permitted mounting positions see Appendix A.4).