Explanation of all i/o signals in start/stop mode, Inputs – Festo Кабели и принадлежности User Manual
Page 197
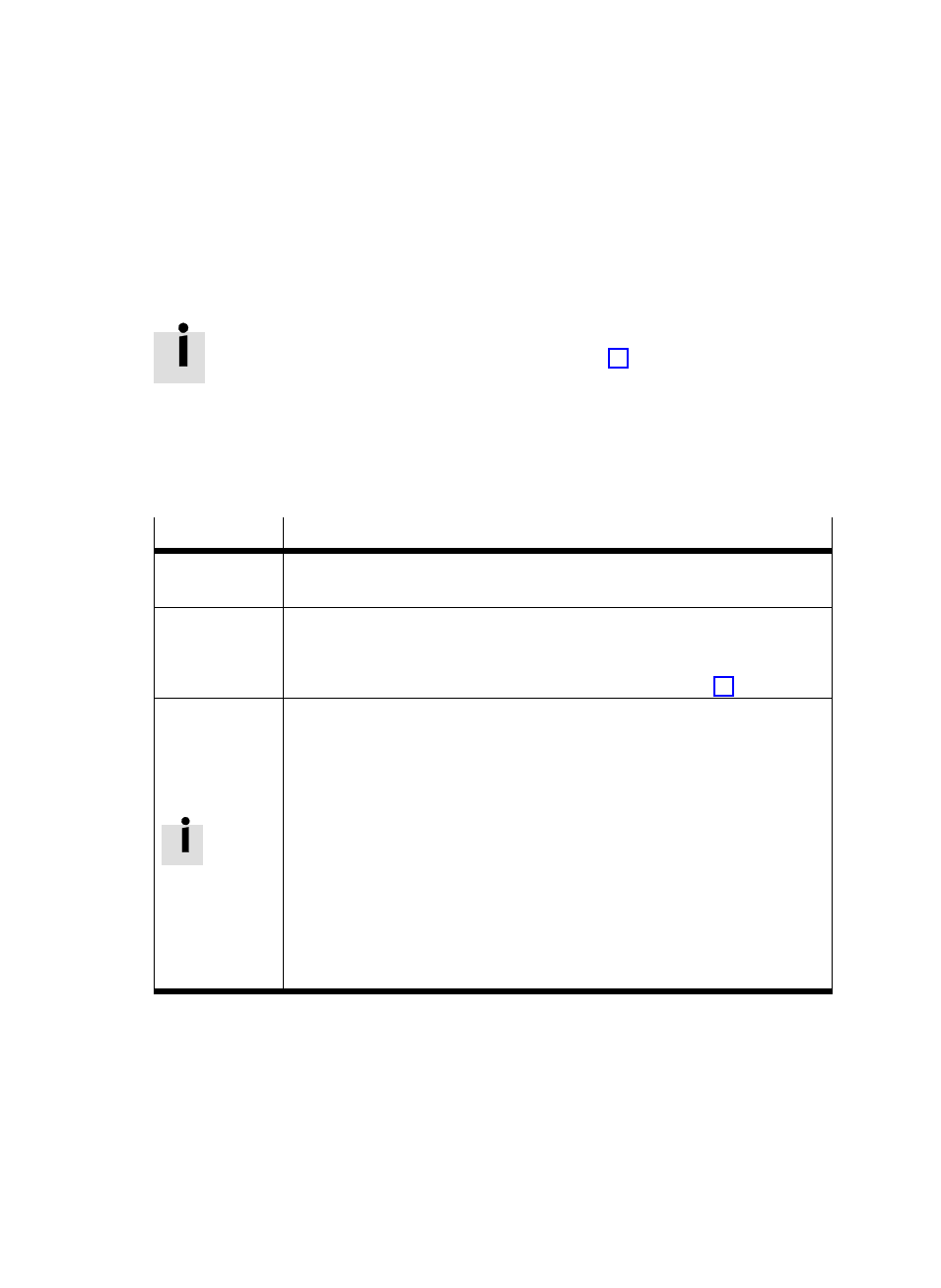
5. Controlling the SPC200
5−11
Festo P.BE−SPC200−EN en 0901d
5.2.1
Explanation of all I/O signals in Start/Stop mode
The connection assignment and I/O addresses of the I/O
modules can be found in chapter 3.5.3, field bus addresses in
the manual for the field bus module.
Inputs
Function
Description
SYNC_IB
Synchronization input for program B
(like SYNC_IA, but for program B)
SYNC_IA
Synchronization input for program A
This input supports synchronization of the SPC200 with external devices (e.g.
PLC/IPC). With a Programmed Stop (command M00) the SPC200 waits for a falĆ
ling edge at this input before it processes the next NC record (see Fig. 5/6).
STOP
Stop program sequence
A falling edge at this input causes:
Ĉ the program sequence and the axes to be stopped.
Ĉ Depending on the parameterisation, the axis is stopped (controlled stop):
Ĉ The position at the time of the stop signal becomes the setpoint position
(d f
lt) Aft
t
d till th
i
b
k t thi
iti
New feature
as from
OS 4.93
(default). After standstill, the axis runs back to this position.
Ĉ The current position at standstill becomes the setpoint position.
This function is only available as from firmware version 4.93 in combination
with WinPISA as from version 4.51.
If there is a 0−signal, a Program Reset can be triggered by a rising edge at the
START input (see under START input).
The program sequence is continued by:
1. a 1−signal at this input
2. a new start signal (Start on the control panel or a rising edge at the START
input).