Monitoring time – Festo Кабели и принадлежности User Manual
Page 319
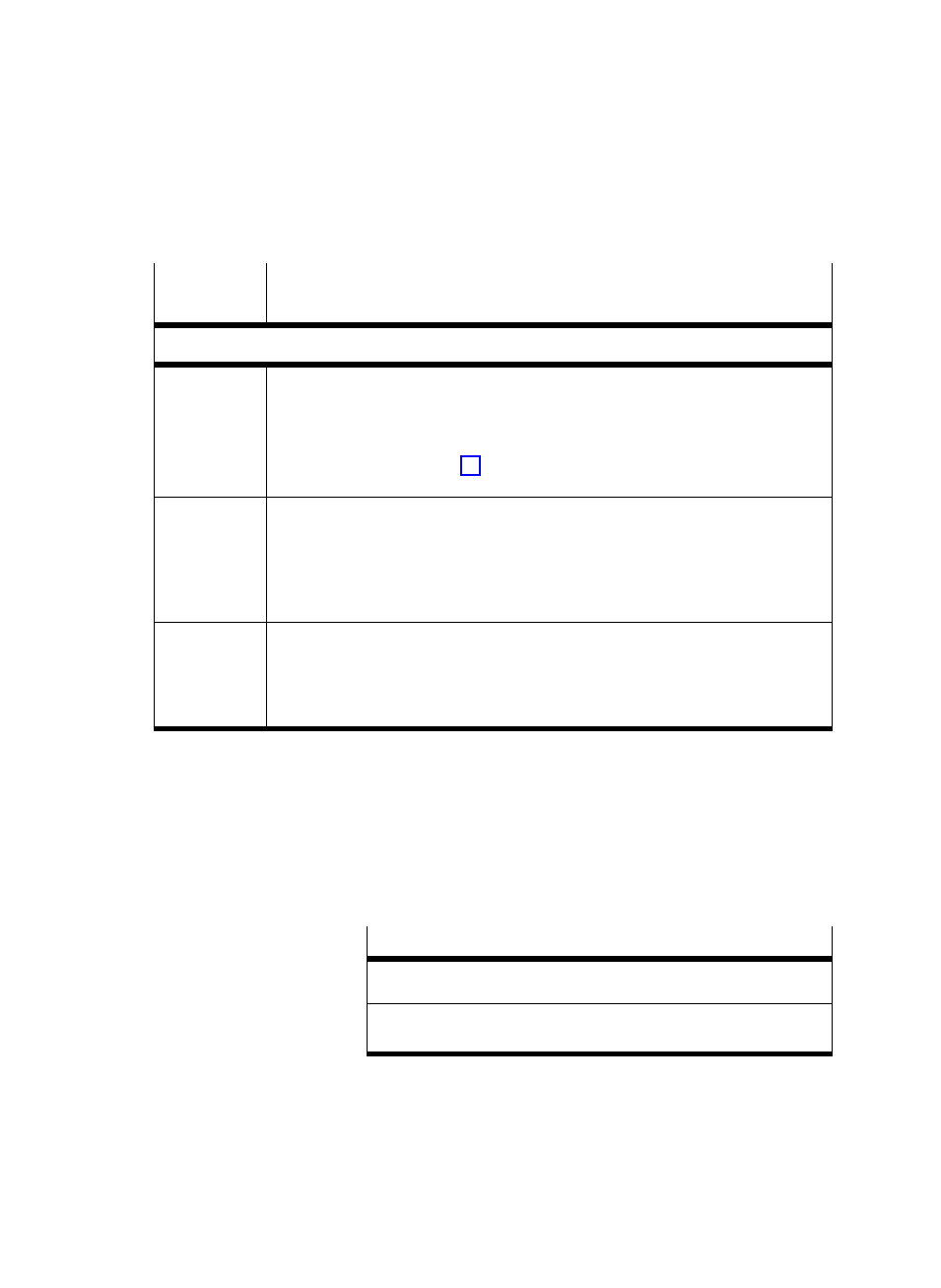
7. Description of the commands
7−53
Festo P.BE−SPC200−EN en 0901d
G60
Exact stop without damping time
ć pneumatic axis; ć permitted in operating mode: Start/Stop, Record Select
Nn G60 X [Y, Z, U]
Effect
Switches the specified axis to exact stop without damping time (positioning quality
class 3, see also under G61).
Output MC_A/MC_B or RC_A/RC_B always supplies a 1−signal when the specified
axis is within the range of the positioning tolerance for the complete duration of
the monitoring time (see also Fig. 7/13). If the axis leaves the tolerance range
before the monitoring time expires, the monitoring time will be reset.
Example
N000 G60 X
N001 G00 X100
;Activate exact stop without damping time
;Move to position X100
(example: Positioning tolerance = 0.2 mm): When moving to position 100 mm,
output MC_A/MC_B or RC_A/RC_B always supplies a 1−signal when the X−axis is
within the range of the positioning tolerance (between 99.8...100.2 mm).
Remark
This command has a saving effect. It remains effective until a switch is made to
Fast Stop with command G62 or to any other positioning quality class with
command G61.
With nominal value modes 0 and 1, the set positioning quality class has no effect
(see NC command M13).
Monitoring time
With the rotary module and with linear drives with a length of
< 300 mm the monitoring time is 20 ms. For linear drives with
a length of > 300 mm the monitoring time can be calculated
as follows:
Formula for linear drives over 300 mm in length
T
monitoring
+
ǒ
L
drive
) 100
Ǔ
B 20
T
monitoring
= monitoring time
in [ms]
L
drive
= stroke length of linear drive in [mm]
Example linear drive (stroke length 500 mm):
Monitoring time in [ms] = (500 + 100) / 20 = 30