2 ) holding, 3 ) aborting – Yaskawa MP2000 Series: Built-in SVB or SVB-01 Motion Module User Manual
Page 167
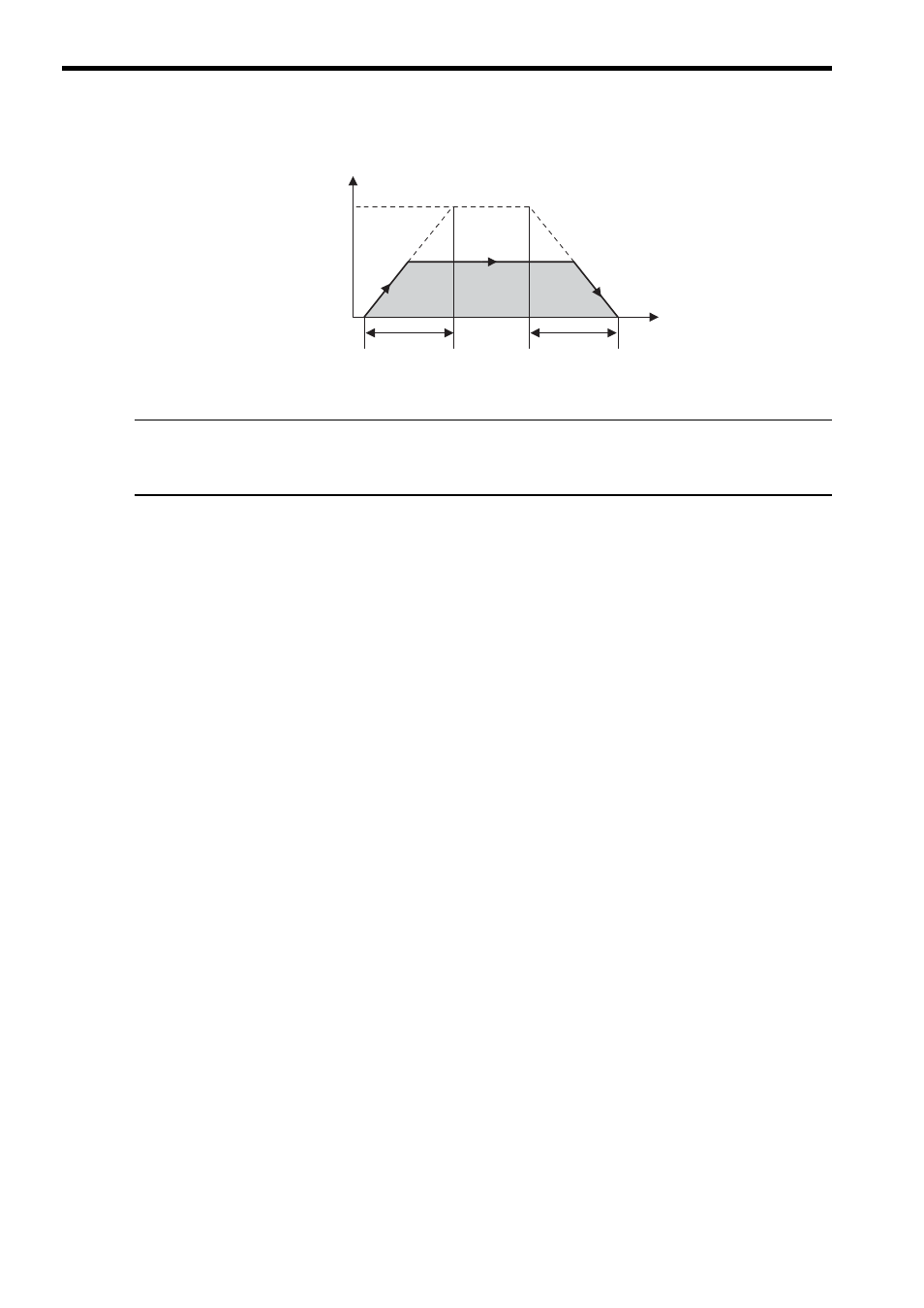
6.2 Motion Command Details
6.2.1 Position Mode (POSING) (Positioning)
6-6
5.
Set OW
08 to 0 to execute the NOP motion command to complete the positioning operation.
Terminology: Command execution
When a command code is stored in the motion command register (OW
08), execution of the motion command correspond-
ing to that code is started. Used in describing motion command operations.
( 2 ) Holding
Axis travel can be stopped during command execution and then the remaining travel can be restarted. A command is
held by setting the Holds a Command bit (OW
09, bit 0) to 1.
• Set the Holds a Command bit (OW
09, bit 0) to 1. The axis will decelerate to a stop.
• When the axis has stopped, the Command Hold Completed bit (IW
09, bit 1) will turn ON.
• Reset the Command Pause bit (OW
09, bit 0) to 0. The command hold status will be cleared and the
remaining portion of the positioning will be restarted.
( 3 ) Aborting
Axis travel can be stopped during command execution and the remaining travel canceled by aborting execution of a
command. A command is aborted by setting the Interrupt a Command bit (OW
09, bit 1) to 1.
• Set the Interrupt a Command bit (OW
09, bit 1) to 1. The axis will decelerate to a stop.
• When the axis has stopped, the remaining distance to be travelled will be canceled, and the Positioning Com-
pleted bit (IW
0C, bit 1) will turn ON.
• The positioning will restart if the Interrupt a Command bit (OW
09, bit 1) is reset to 0 while the command
is being aborted.
This type of operation will also be performed if the motion command is changed during axis movement.
Precautions
Be careful to stop the movement during an axis operation by limiting the torque at OL
14 (Positive Side Limiting
Torque Setting at the Speed Reference). When the movement is stopped, the torque is no longer limited and may rap-
idly increase just after stopping. To abort positioning while the torque is limited, use one of the following settings.
• Set the speed reference to 0
• Set bit 0 of OW
09 (Motion Command Control Flag) to 0 and set OW
08 (Motion Command) to 0 for a
No Operation (NOP) command when the axes stop or turn ON the abort request.
For more information on the maximum allowable value for acceleration and deceleration, refer to Changing the max-
imum value of acceleration and deceleration for SGDV SERVOPACKs of 4.4.2 ( 23 ).
Speed
(100%)
0
Positioning
speed
Rated speed
(%)
Position
Reference
Straight Line
Acceleration Time
Constant
(t)
Time
Straight Line
Deceleration Time
Constant
POSING Operating Pattern