4 gain setting reference values, Machines with high rigidity, Machines with medium rigidity – Yaskawa Large Capacity Sigma II Series User Manual
Page 217: Machines with low rigidity
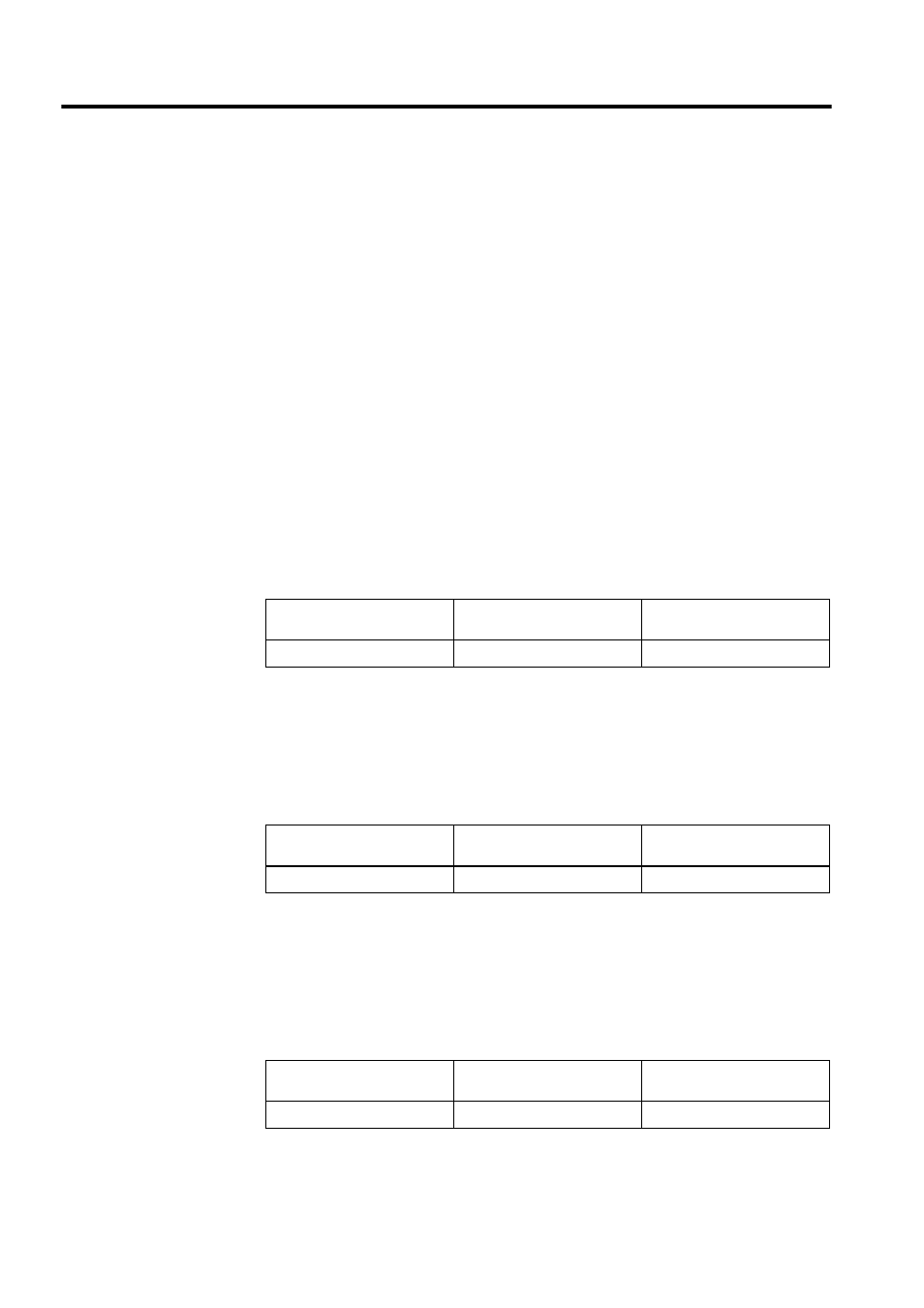
5 Servo Adjustment
5.4.4 Gain Setting Reference Values
5-34
5.4.4 Gain Setting Reference Values
This section describes information on servo gain values as reference for making gain adjust-
ments.
Refer to the following for standards for gain adjustments according to the rigidity of the
mechanical system. Refer to these values and use the previously mentioned methods to
make gain adjustments. These values are for reference only and do not mean that the
mechanical system has good response characteristics or is free from oscillation in the speci-
fied ranges.
Observe the response by monitoring the response waveform and make the optimum gain
adjustments. If the rigidity of the machinery is high, further gain increments exceeding the
described ranges are possible.
Machines with High Rigidity
These machines are directly connected to ball screws.
Example: Chip mounting machine, bonding machine, high-precision machine tool
Machines with Medium Rigidity
These machines are driven by ball screws through speed reducers or long-length machines
directly driven by screws.
Examples: General machining tool, transverse robot, and conveyor
Machines with Low Rigidity
These machines are driven by timing belts or chains or machines with wave reduction gears.
Example: Conveyor and articulated robot
Position Loop Gain (Pn102)
[1/s]
Speed Loop Gain (Pn100)
[Hz]
Speed Loop Integral Time
Constant (Pn101) [ms]
50 to 70
50 to 70
5 to 20
Position Loop Gain (Pn102)
[1/s]
Speed Loop Gain (Pn100)
[Hz]
Speed Loop Integral Time
Constant (Pn101) [ms]
30 to 50
30 to 50
10 to 40
Position Loop Gain (Pn102)
[1/s]
Speed Loop Gain (Pn100)
[Hz]
Speed Loop Integral Time
Constant (Pn101) [ms]
10 to 20
10 to 20
50 to 120