Position control required parameters – Yaskawa Large Capacity Sigma II Series User Manual
Page 214
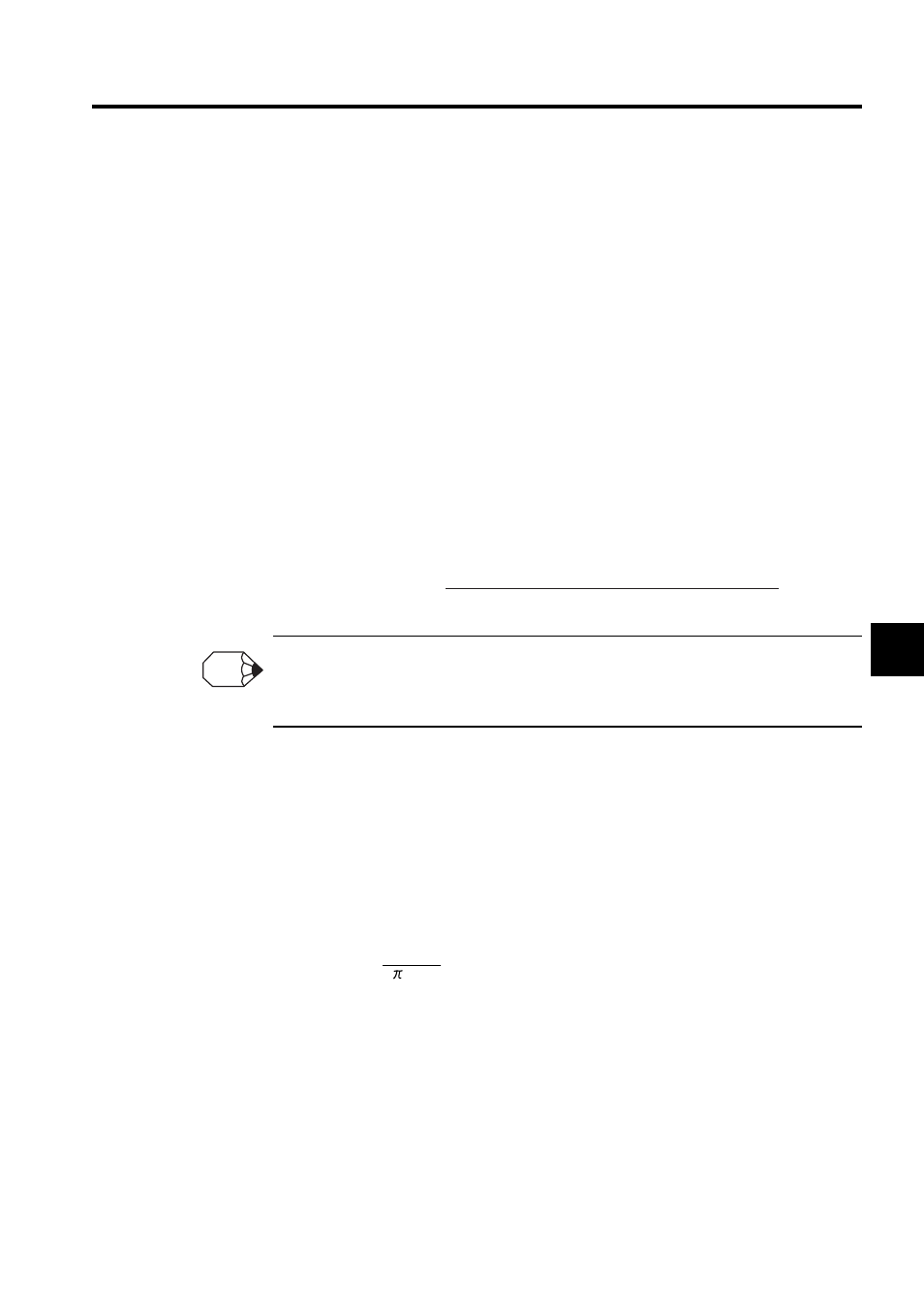
5.4 Servo Gain Adjustments
5-31
5
a larger value.
5. Finally, progressively make fine adjustments to parameters such as the position loop
gain, speed loop gain, and integral time constant to find the optimal points.
Position Control
Required Parameters
The following parameters are used.
• Speed Loop Gain (Pn100)
This parameter is used for determining the response speed of the speed loop. The
response speed increases if the constant is set to a large value provided that the mechan-
ical system does not vibrate. The value of speed loop gain is the same as the set value of
Pn100 if the inertia ratio set in Pn103 is correct.
Speed loop gain Kv = Set value of Pn100 (Hz)
Set Pn103 to the following value.
In the case of manual adjustments of parameters, the user must set the value of parameter Pn103. The
inertia ratio can be obtained if the servo gain constant is written with parameter Fn007 after autotuning
has been performed. For details regarding Fn007, refer to 5.3 Autotuning.
• Speed Loop Integral Time Constant (Pn101)
The speed loop has an integral element so that the speed loop can respond to minute
inputs. This integral element delays the operation of the servo system, so a longer posi-
tioning setting time is required with slower response speed as the value of the time con-
stant increases.
If the load moment of inertia is large or the mechanical system is likely to vibrate, make
sure that the speed loop integral time constant is large enough; otherwise the mechanical
system will vibrate. The following formula is the standard.
Ti: Integral time constant [s]
Kv: Speed loop gain (calculated from the above) [Hz]
• Torque Reference Filter Time Constant (Pn401)
If the mechanical system uses ball screws, torsion resonance may result, in which case
the oscillation noise will be a high-pitched tone. The oscillation may be stopped by
increasing the time constant of the torque reference filter. Like the integral time con-
stant, this filter causes a delay in the operation of the servo system. Therefore, this con-
stant must not be set to an excessively large value.
Pn103 set value =
Motor axis conversion load moment of inertia (J )
Servomotor rotor moment of inertia (J )
M
L
× 100 (%)
INFO
Ti
≥ 2.3 ×
1
2
× Kv