Phase loss protection – Rockwell Automation 592- E300 Overload Relay User Manual User Manual
Page 87
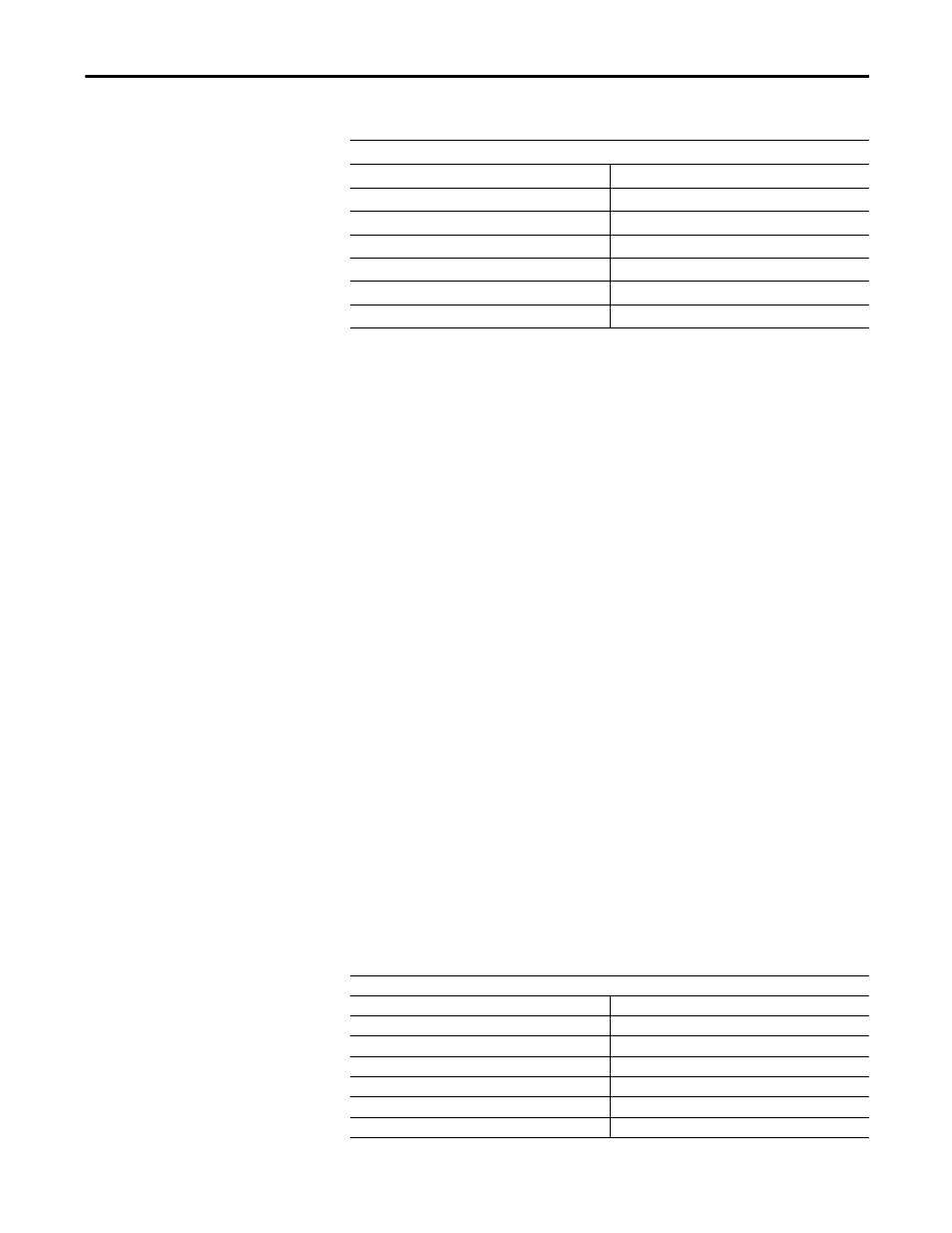
Rockwell Automation Publication 193-UM015B-EN-P - June 2014
87
Protective Trip and Warning Functions Chapter 5
Table 66 - Overload Time to Reset (Parameter 3)
Non-Volatile Thermal Memory
The E300 Electronic Overload Relay includes a non-volatile circuit to provide
thermal memory. The time constant of the circuit corresponds to a Trip Class 20
setting. During normal operation, the thermal memory circuit is continuously
monitored and updated to accurately reflect the thermal capacity utilization of
the connected motor. If power is removed, the thermal memory of the circuit
decays at a rate equivalent to the cooling of a Trip Class 20 application. When the
power is re-applied, the E300 Electronic Overload Relay checks the thermal
memory circuit voltage to determine the initial value of % Thermal Capacity
Utilized (Parameter 1).
Phase Loss Protection
A high current imbalance, or phase failure, can be caused by defective contacts in
a contactor or circuit breaker, loose terminals, blown fuses, sliced wires, or faults
in the motor. When a phase failure exists, the motor can experience an additional
temperature rise or excessive mechanical vibration. This may result in a
degradation of the motor insulation or increased stress on the motor bearings.
Rapid phase loss detection helps to minimize the potential damage and loss of
production.
Phase Loss Inhibit Time
Phase Loss Inhibit Time (Parameter 239) allows the user to inhibit a phase loss
trip from occurring during the motor starting sequence. It is adjustable from
0…250 seconds.
Table 67 - Phase Loss Inhibit Time (Parameter 239)
Overload Time to Reset (Parameter 3)
Default Value
0
Minimum Value
0
Maximum Value
9999
Parameter Type
UINT
Size (Bytes)
2
Scaling Factor
1
Units
Sec
Phase Loss Inhibit Time (Parameter 239)
Default Value
0
Minimum Value
0
Maximum Value
250
Parameter Type
USINT
Size (Bytes)
1
Scaling Factor
1
Units
Sec