Tpv - t sv t e – Delta DVP-ES2 User Manual
Page 364
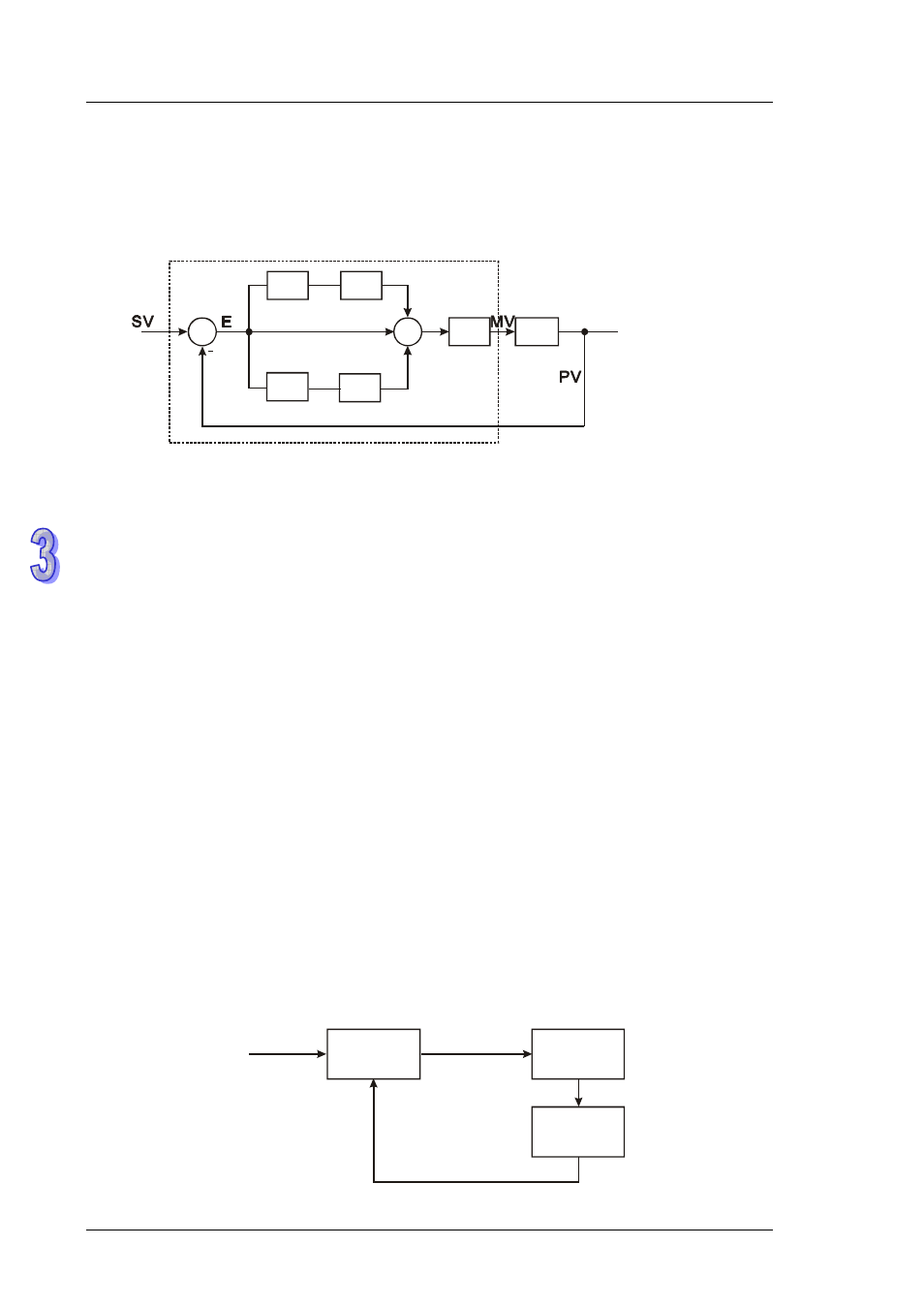
D V P - E S 2 / E X 2 / S S 2 / S A2 / S X 2 / S E O p e r a t i o n M a n u a l - P r o g r a m m i n g
3-248
Where
( )
( )
( )
t
PV
-
t
SV
t
E
=
y
Control diagram:
G(s)
S
1/S
1/T
I
T
D
+
+
+
PID operation is within dotted area
P
+
K
Notes and suggestion:
1.
S
3
+ 3 can only be the value within 0 ~ 30,000.
2.
There are a lot of circumstances where PID instruction can be applied; therefore, please
choose the control functions appropriately. For example, when users select parameter
auto-tuning for the temperature (S
3
+ 4 = K3), the instruction can not be used in a motor control
environment otherwise improper control may occur.
3.
When you adjust the three main parameters, K
P
, K
I
and K
D
(S
3
+ 4 = K0 ~ K2), please adjust K
P
first (according to your experiences) and set K
I
and K
D
as 0. When the output can roughly be
controlled, proceed to increase K
I
and K
D
(see example 4 below for adjustment methods). K
P
=
100 refers to 100%, i.e. the proportional gain to the error is 1. K
P
< 100% will decrease the
error and K
P
> 100% will increase the error
4.
When temperature auto-tuning function is selected(S
3
+ 4 = K3, K4), it is suggested that
store the parameters in D register in latched area in case the adjusted parameters will
disappear after the power is cut off. There is no guarantee that the adjusted parameters are
suitable for every control requirement. Therefore, users can modify the adjusted parameters
according to specific needs, but it is suggested to modify only K
I
or K
D.
5.
PID instruction has to be controlled with many parameters; therefore care should be taken
when setting each parameter in case the PID operation is out of control.
Example 1: Block diagram of application on positioning (S
3
+4 = 0)
PID
MV
Encoder
PV
Position instruction
(SV)
Controlled
device