Positioning, L-force | plc designer – Lenze PLC Designer PLC Designer (R3-1) User Manual
Page 612
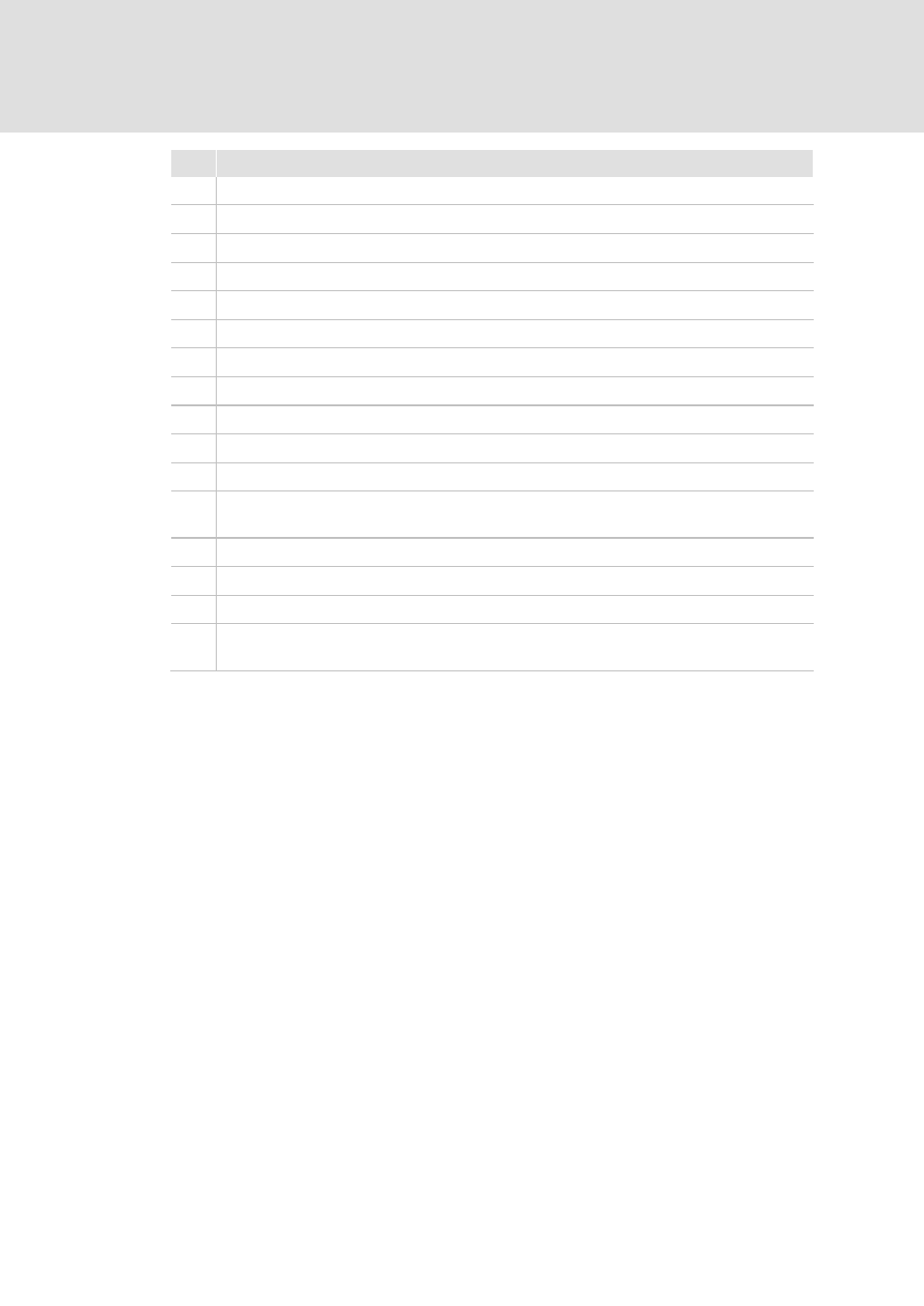
L-force | PLC Designer
General Editors
610
DMS 4.1 EN 03/2011 TD29
Letter Function
G42
Start the tool radius correction to the right of the workpiece
G50
End of RoundPath/SmoothPath function
G51
Start the SmoothPath function
G52
Start the RoundPath function
G53
End the shift coordinate function.
G54
Set offset of all following coordinates to the specified position
G55
Add the specified position to the current offset.
G56
Set the offset such that the current position equals the specified position
G60
End of the avoid-loop function
G61
Start of the avoid-loop function
G75
Time synchronisation with interpolator
G90
Start interpreting the following coordinate values (for X/Y/Z/P-W/A/B/C) as absolute values
(default)
G91
Start interpreting the following coordinate values (for X/Y/Z/P-W/A/B/C) as relative values
G92
Setting the position without move
G98
Start interpreting the following coordinate values of I/J/K as absolute values
G99
Start interpreting the following coordinate values of I/J/K as values relative to the starting point
(standard)
Please regard that the library "SM3_CNC " must be included to enable an error-free
compilation of the project.
Positioning
Command G0, G92
These commands are used for changing interpolator positions.
In case of G0 the changing is done by moving on a line to the next position. In
contrastto G1 the G0 elements aren't modulated with path-preprocessors like tool
radius, smooth path or round path correction.
With G92 the position of the interpolator is set by jump. The consequence is, that
these jumps are executed on the axes, except when programming features like
MC_ControlAxisByPos.bAvoidGaps:=TRUE prevent this. „smc_controlaxisbypos“. If G92
is applied in a CNC programm before the frirst positioning element, then it can have
the designed use of setting the start position.