Library: l_sm3_driveutil.lib, Function block l_smc_settorquelimit (for ethercat), L-force | plc designer – Lenze PLC Designer PLC Designer (R3-1) User Manual
Page 28
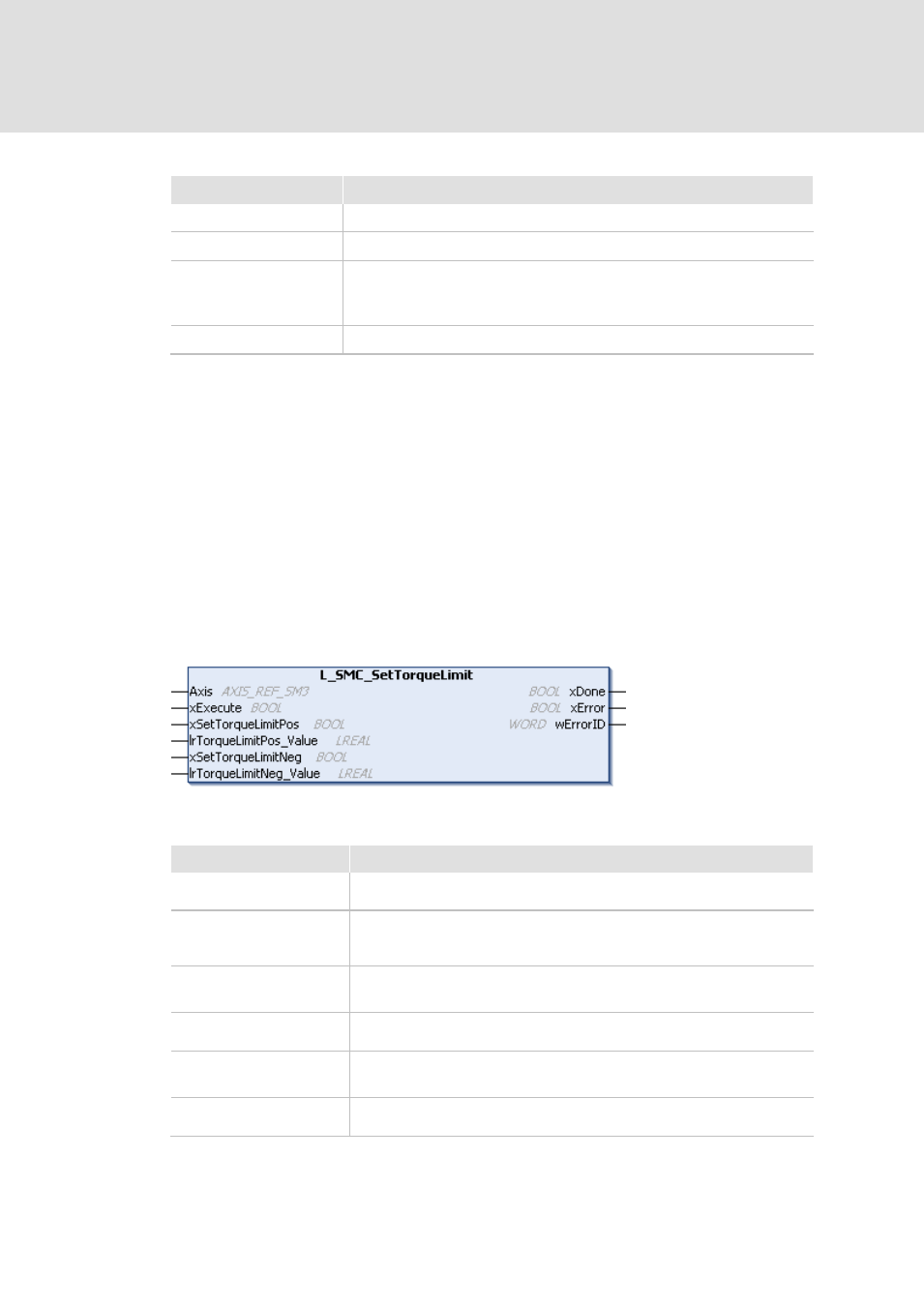
L-force | PLC Designer
Lenze Specific Functions
26
DMS 4.1 EN 03/2011 TD29
Error messages from the function block
Error number
Meaning
507
Incorrect format indicated during an instance of write access
531
Incorrect format indicated during assignment
532
Code contains float/double parameters (e.g. supply voltage C00205 or
rechargeable-battery voltage C00207); This format is not supported by the
block.
Other
Internal software error; Please contact your Lenze Service Centre.
2.1.3
Library: L_SM3_DriveUtil.lib
Function block L_SMC_SetTorqueLimit (for EtherCAT)
Function library: L_SM3_DriveUtil.lib
The torque limits of a drive in the positive and negative direction of rotation can be
prescribed by the control system. Previously, the limits were set by means of SDO
access. If the drives are controlled via an EtherCAT fieldbus, it is possible to transfer
these values as part of the cyclical process data. The advantage of this is considerably
faster transfer of the values to the drive.In order to use this, a corresponding mapping
that contains these torque limits as an item of process data must be selected in the
EtherCAT Configurator.
Access to the torque limits from the PLC takes place by means of the function block
L_SMC_SetTorqueLimit:
Inputs (VAR_IN)
Designator / Data type
Info / Setting options
Execute / BOOL
Activates the function.
SetTorqueLimitPos / BOOL Requests a positive torque limit
TorqueLimitPos_Value /
LREAL
Positive torque limit in the range 0 ... 100 % of the rated torque
SetTorqueLimitNeg / BOOL Requests a negative torque limit
TorqueLimitNeg_Value /
LREAL
Negative torque limit in the range 0 ... 100 % of the rated torque
Axis / AXIS_REF
Here, the axis structure to which these torque limits apply is transferred.