5 mains phase failure monitoring, 6 maximum current monitoring, Maximum current monitoring – Lenze 8400 motec User Manual
Page 179: Mains phase failure monitoring, 5motor control (mctrl)
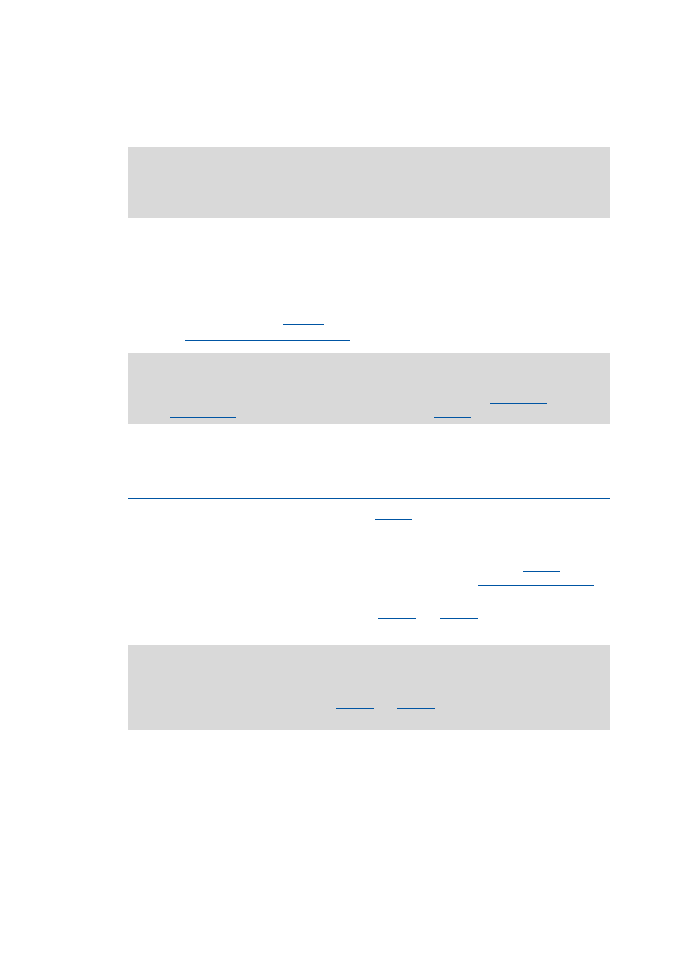
Lenze · 8400 motec · Reference manual · DMS 4.1 EN · 08/2013 · TD05
179
5
Motor control (MCTRL)
5.14
Monitoring
_ _ _ _ _ _ _ _ _ _ _ _ _ _ _ _ _ _ _ _ _ _ _ _ _ _ _ _ _ _ _ _ _ _ _ _ _ _ _ _ _ _ _ _ _ _ _ _ _ _ _ _ _ _ _ _ _ _ _ _ _ _ _ _
5.14.5
Mains phase failure monitoring
The drive controller has a simple mains-phase failure detection function with which a mains phase
failure can be detected under load.
• In the case of power-adapted machines, approx. 50 % of the rated motor power must be
exceeded so that a main-phase failure can be detected.
• If the mains phase failure monitoring is tripped:
will be carried out (Lenze setting: "Warning").
• The "
Su02: Mains voltage switched-off
" error message is entered into the logbook.
5.14.6
Maximum current monitoring
This function extension is only available from version 03.00.00!
The ultimate motor current to be parameterised in
is a limit value to protect the motor from
destruction, influence of the rated data and demagnetisation.
• This limit value must not be travelled cyclically in the drive process.
• If the instantaneous value of the motor current exceeds the limit value set in
, the error
response "Fault" occurs to protect the motor and the error message "
" is
entered into the logbook.
• The maximum currents to be parameterised in
and
should have a sufficient
distance to this limit value.
Stop!
Under load, the mains input of a three-phase controller can be destroyed if the device is
only supplied by two phases (e.g. if a mains phase fails).
Note!
The failure of a mains phase can also generate an error message "
". This error cannot be parameterised by
.
Note!
If a Lenze motor is selected from the catalogue whose plant parameters are transferred
into the controller, the settings in
and
will automatically be adapted to
the selected motor.