Rockwell Automation 8520 9/Series CNC Integration Maintenance Manual Documentation Set User Manual
Page 862
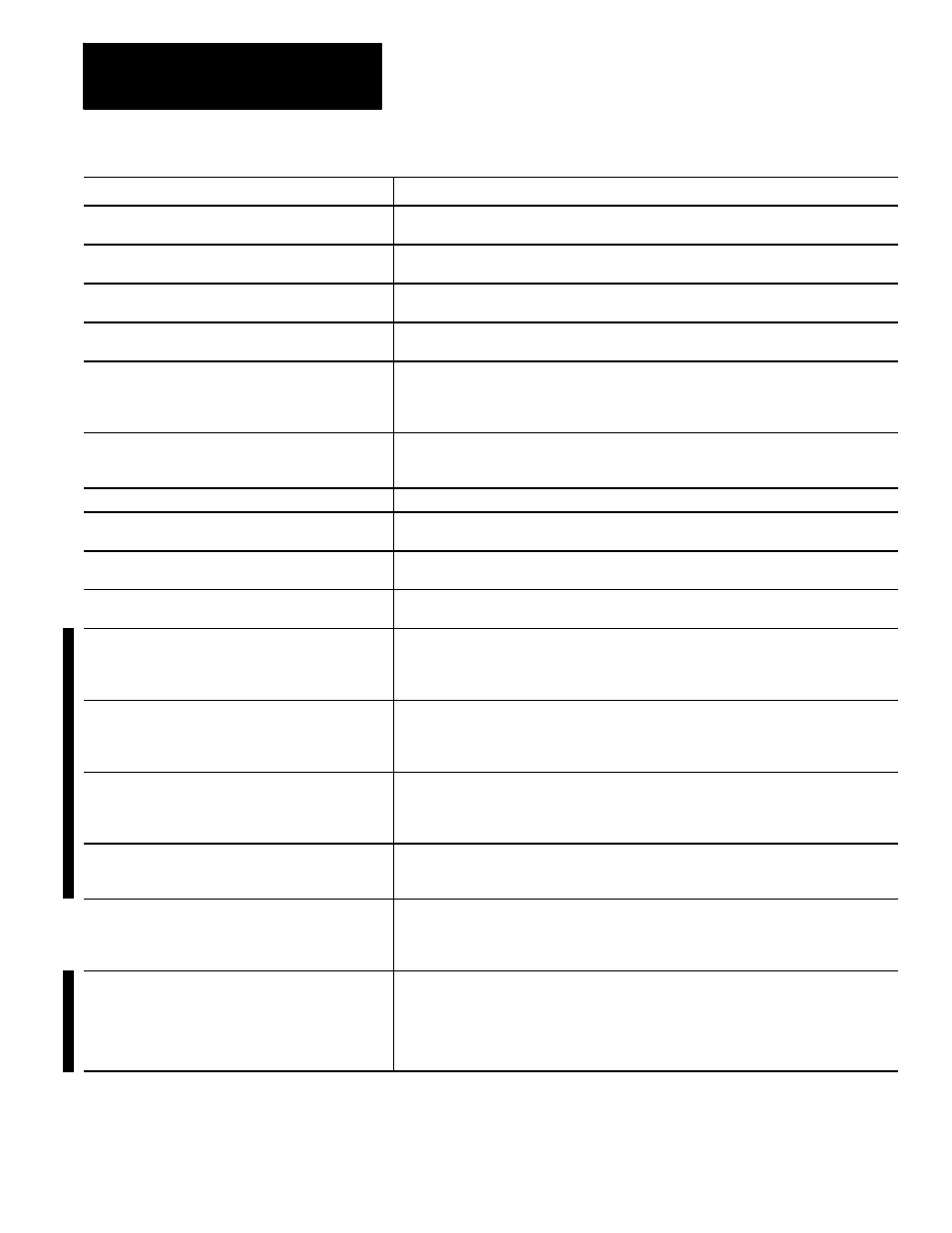
Error and System Messages
Section 16
16-42
Message
Description
STORING TO BACKUP - PLEASE WAIT
This message appears whenever AMP or axis calibration data in RAM is being stored in backup
memory.
SYMBOL NAME FORMAT ERROR
Check the remote symbol and CNC symbol to make sure they exist on both remote and CNC.
Check the table of the read only or write only variables.
SYMBOL NOT FOUND
Check the remote symbol and CNC symbol to make sure they exist on both remote and CNC.
Check the table of the read only or write only variables.
SYNCHRONIZATION DEADLOCK
A synchronization code is activated and caused the activating process to wait on a process that
is already waiting.
SYNCH SPINDLES MISCONFIGURED
Causes for this could be: only one spindle (either controlling or follower) was defined in the
synchronized spindle pair, you exceeded the simple feedback ratio limitation of 10 (e.g., 11:1 or
2:13), or on a multiprocess system, one (or both) of the spindles in the synch pair is currently not
available to the process making the synchronization request.
SYNCH SPINDLES REQUIRE FEEDBACK
One or both of the spindles, configured in AMP as a member of a synchronized pair, did not
have feedback. Both spindles in a synchronized pair must be equipped with an AMP configured
feedback device.
SYNTAX ERROR (COMMA)
A missing comma or an extra comma was found in the program block.
SYSTEM DIAGNOSTIC #1
An illegal parameter was passed into a switch statement (mid-program start) in the control
software. Contact Allen-Bradley customer support services.
SYSTEM DIAGNOSTIC #2
An illegal parameter was passed into a switch statement (ASCII buffer task) in the control
software. Contact Allen-Bradley customer support services.
SYSTEM DIAGNOSTIC #3
An illegal parameter was passed into a switch statement (ASCII buffer task) in the control
software. Contact Allen-Bradley customer support services.
SYSTEM MODULE CONFIG ERROR
In the “Smart “1394 power supplies, the CNC sends configuration data to the power supply.
These values are read back by the CNC for verification. This fault message indicates a
mismatch between the two values. This mandates that the system module power supply be
replaced.
SYSTEM MODULE GROUND FAULT
The 1394 system module has detected a ground fault. The system generates a ground fault
when there is an imbalance in the DC bus of greater than 50 A. This drive error can be caused
by incorrect wiring (verify motor and ground wiring), motor malfunction, or an axis module IGBT
malfunction.
SYSTEM MODULE CURRENT LIMIT WARNING
The system module has reached 80% of it’s RMS Bus current capabilities. You may need to
reduce the acc /dec profiles or increase the size of the system module. The CNC system will
not take action based on this fault, However the machine logic (PAL) can take action based on
this status.
SYSTEM MODULE MIS MATCH
This error indicates an AMP value is set in error on a 1394 “smart”power system module. You
may have set some of the “system wide” parameters differently between two axes that exist on
a single 1394 platform.
SYSTEM MODULE OVER CURRENT
The system module has reached the limit of its current capabilities. The total motoring and
regeneration current produced has exceeded the current capability of the system module by 5%
or more. You may need to reduce the acc /dec profiles or increase the size of the system
module.
SYSTEM MODULE OVER TEMP
The 1394 contains a thermal sensor which senses the internal ambient temperature. Causes
could be that : The cabinet ambient temperature is above the 70 deg C rating. The machine
duty cycle requires an RMS current exceeding the continuous rating of the controller. The
airflow access to the 1394 is limited or blocked. An axis module or a system module FAN has
failed. This does not necessarily indicate a motor over temperature. Motor over temperture
sensors should be wired directly into the E-Stop string.