Rockwell Automation 8520 9/Series CNC Integration Maintenance Manual Documentation Set User Manual
Page 656
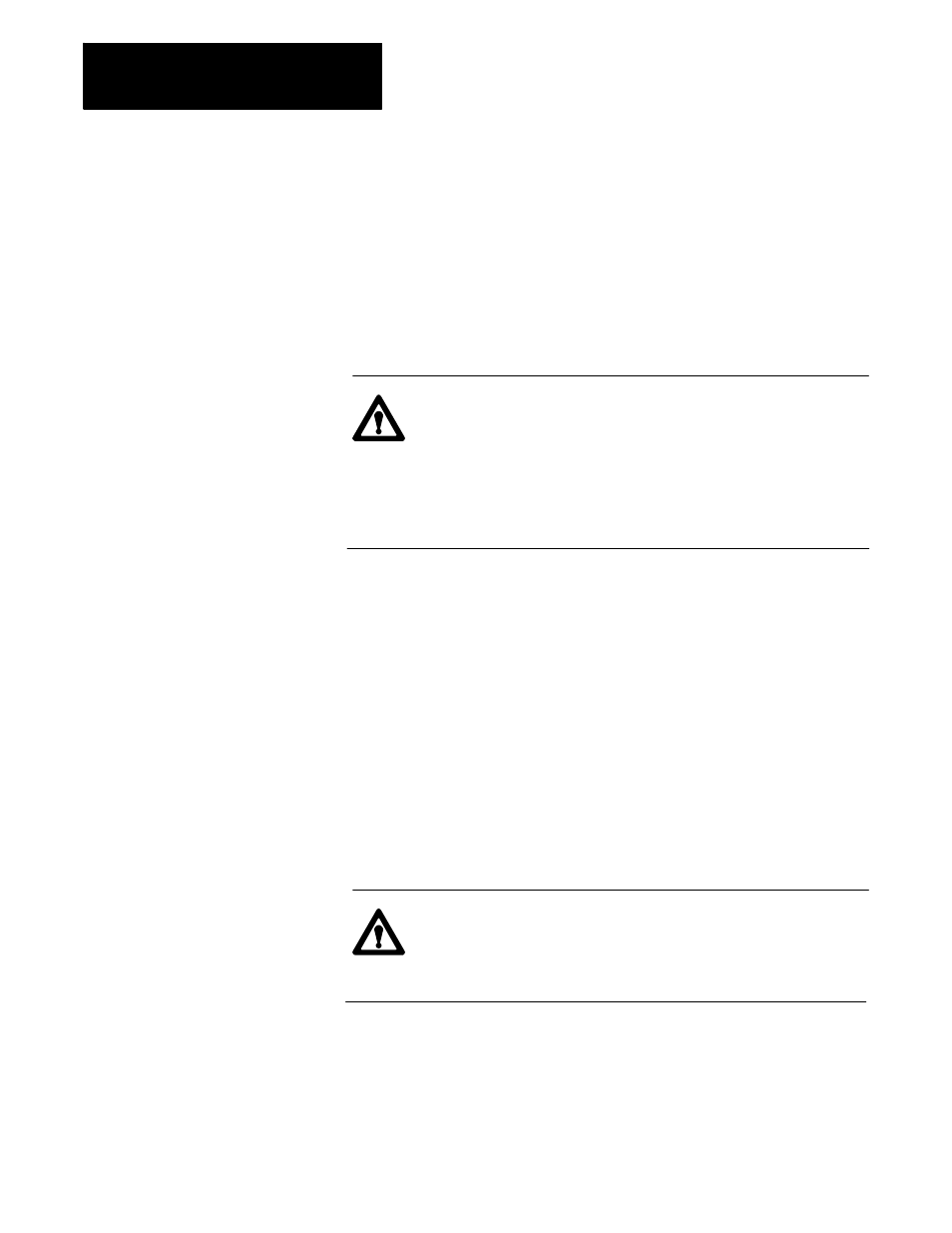
Section 13A
Connecting 8520 Digital Drive Systems
13A-22
Normally-closed contacts must be installed as shown in Figure 13A.10 and
Figure 13A.11. These four contacts should be held open whenever the
8520 digital servo amplifier is energized and should be closed by the
emergency stop circuitry. You must wire at least four contacts in series to
safely break this connection. Allen-Bradley 100-A30ND3 contactors with
added deck 195-FAD4 are recommended. Refer to a 1389 transformer
manual for special requirements and additional information on the
normally-closed contactor. Details on emergency stop wiring start on
page 6-1.
ATTENTION: The four normally closed contacts shown in
Figure 13A.10 and Figure 13A.11 should not be used on
machines with large non-counter balanced vertical axes. No
contacts are required. Under a normal shut down, leaving these
contacts out allows the drive to maintain torque for a longer
period of time. This provides more time for holding brakes to
set.
Important: Jumpers on the 8520 digital servo amplifier circuit boards
must be set for internal or external shunt resistor. These jumpers control
the duty cycle (amount of continuous “on” time) for the shunt resistors.
Important: The external shunt resistor should be mounted in an area
where the heat it generates will not adversely affect other components of
the control.
Important: The shunt contacts should not be closed while 3-phase power
is applied to the drive amplifier. The shunt circuitry is sized to dynamic
braking of the axis when E-stop is applied and 3-phase power is removed
from the amplifier.
ATTENTION: To guard against electrical shock hazards, never
make connections or disconnections at the ac distribution
network unless the main ac disconnect switch is open and
locked.
Figure 13A.1 shows how power is distributed from the supply to the
transformer and amplifier.
13A.7
8520 Drive Power
Distribution