Rockwell Automation 8520 9/Series CNC Integration Maintenance Manual Documentation Set User Manual
Page 188
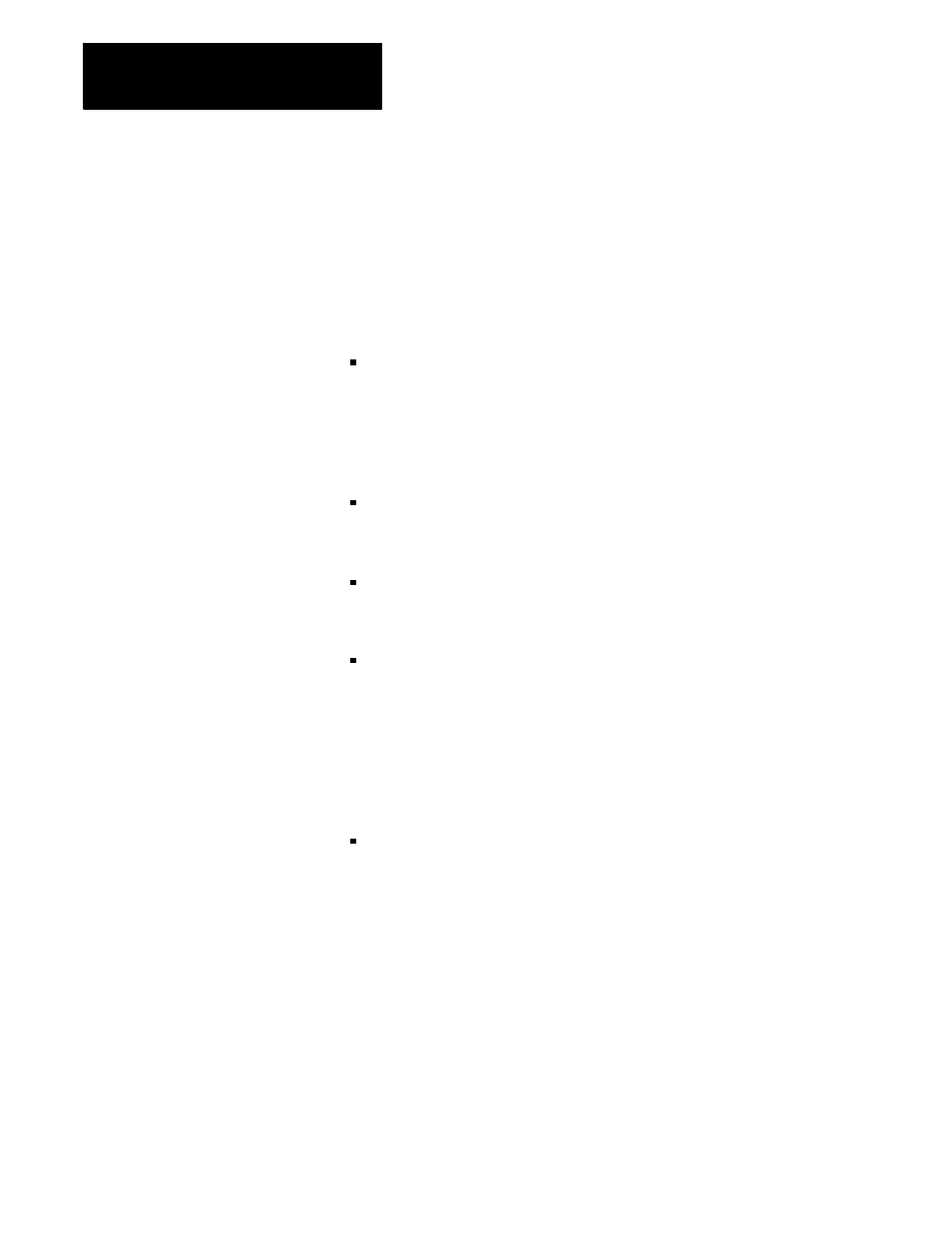
Section 4B
Connecting the 3-axis Servo Module
4B-42
This section discusses encoder feedback devices that are compatible for
both analog and digital servo systems. The servo module supplies these
devices with either +5V or +15V power. Feedback devices on all the
CNCs must return a 5V compatible output signal to the control (1326
motor mounted resolvers have their signals converted by the system
module to be compliant with this requirement).
For analog systems this feedback device can be used to provide:
velocity feedback (used only if your system does not provide tachometer
velocity feedback to the drive) In this case, the analog servo amplifier
must be configured to run in “torque mode” with no tachometer.
Tachless servo configurations work best if an encoder type feedback
device is used and mechanically coupled directly to the servomotor
shaft.
position feedback (can be the same device as used to close the velocity
loop if the velocity loop is closed by the CNC, or an additional feedback
device, as discussed in this section, can be used for the position loop)
spindle feedback
For digital systems this feedback device can be used to provide:
position feedback (digital systems require the motor mounted feedback
device, provided on our standard digital servo motors, be used for
velocity loop feedback. This motor mounted feedback device can also
be used to close the position loop or an additional feedback device, as
discussed in this section, can be used for the position loop.) You can not
replace or bypass the motor mounted feedback device. The motor
mounted feedback device must be used for velocity feedback and to
attain proper motor commutation on digital servo systems.
spindle feedback
Only the 8520 digital drive system supports absolute feedback.
4B.8
Compatible
Feedback Devices