Rockwell Automation 8520 9/Series CNC Integration Maintenance Manual Documentation Set User Manual
Page 824
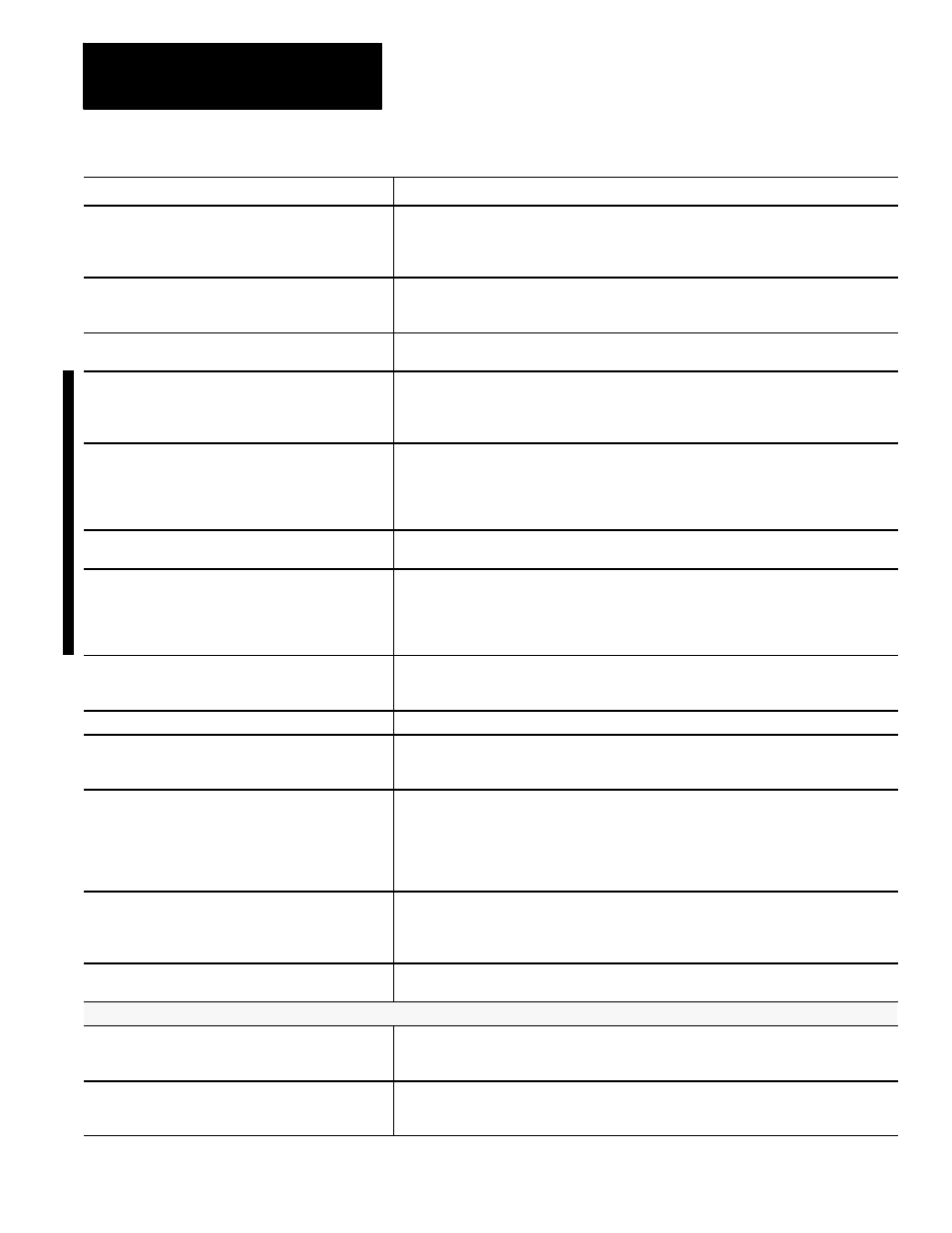
Error and System Messages
Section 16
16-4
Message
Description
AXIS IN PLANE DOES NOT EXIST
At least one of the axes assigned to a plane that was defined in AMP does not exist. An
example of when this error would occur is if an axis was renamed in AMP, but that new name
was not entered into the AMP plane definition. Another example would be if an unfitted axis
was assigned to that plane.
AXIS INVALID FOR G24/G25
The programmed axis was not AMPed for software velocity loop operation, and can not be used
in a G24 or G25 block. To use these features the axis programmed must be configured for
tachless operation (or be a digital servo).
AXIS IS HARD STOPPED, CANT ADJUST SERVO
The torque limit of the servo can not be adjusted because, either the axis is in a hard--stopped
state, or some other axis on the same servo card is in a hard--stopped state.
AXIS MODULE POWER FAULT
The axis module hardware has faulted from a short duration over current condition. If the output
current exceeds a fixed level (Over 200% of axis module rating for the 10 and 15 Kw modules
and Over 300% for the 2, 3 and 5 Kw modules) this fault will appear. Typical causes are a
shorted lead, motor malfunction, or malfunctioning power IGBTs.
AXIS MODULE OVER CURRENT
One of the axis modules of your 1394 drive has been requested to provide too much current
over an extended time period. This is typically caused by: Accel/Decel command from the CNC
is requiring peak current for an excessive amount of time, the machine friction or inertial/viscous
load is excessive, the motor has been improperly sized, a short circuit exists across the drive
output terminals, logic supply circuits have malfunctioned, or AC input is incorrectly wired.
AXIS MODULE BUSS VOLTAGE LOSS
The DC bus supply was lost to the axis module. Check slider connections/termination strip or
there could be a blown link fuse. This condidtion also occurs in a systemE--stop state.
AXIS MODULE OVER TEMP
The 1394 contains a thermal sensor which senses the internal ambient temperature. Causes
could be: that the cabinet ambient temperature is above rating. The machine duty cycle
requires an RMS current exceeding the continuous rating of the controller. The airflow access to
the 1394 is limited or blocked. This does not necessarily indicate a motor over temperature.
Motor over temperture sensors should be wired directly into the E-Stop string.
AXIS MOVER CONFLICT WITH G16.3/G16.4
You have requested a PAL axis mover function on an angled wheel grinder. You can not use the
PAL axis mover in one of the angled wheel modes unless the PAL axis mover has control of
both the axial and the wheel axes.
AXIS NAME DUPLICATE
Two or more axes have been assigned the same name in AMP.
AXIS NOT IN PROCESS
You attempted to read/write a paramacro parameter for an axis that is not currently in the
process requesting the data. To access paramacro parameter data for an axis, that axis must
be in the process making the request.
AXIS POSITION INCORRECT
Using the mid-start program function, you have searched to a block that does not create the
programmed contour if started from your current axis position. Be aware the mid-start operation
may have searched thru a offset operation that is not readily apparent to determine your axis
position. The mid-start operation is aborted. You must re-perform the mid-start operation and
either position the axes to the correct axis position, or use the {MOVE & EXIT} softkey to find the
correct axis position.
AXIS SELECT NOT ALLOWED
The {AXIS SELECT} softkey was pressed when no axis select option is available. Axis select is
only available on large screens and normal character size screen for systems that contain more
then 9 axes total or dual process systems with more than 8 axes in a process. It is not available
when the small screen (showing all system AMPed axes) is being viewed.
AXIS TYPE-POSITION LOOP ERROR
In patch AMP, an axis was assigned a position loop type that is illegal for the axis type assigned
to that axis.
B
BACKUP VERSION OF AMP WAS COPIED TO RAM
The AMP in RAM was erased (battery backup failed) or corrupted, so the control automatically
copied the version of AMP in backup memory into RAM memory. (The control stores AMP in
backup, but works from the copy of AMP in RAM memory.)
BAD DAC MONITOR PATCH AMP ENTRY
An invalid value was entered into patch AMP parameter #86 or #87. Either parameter allows
the axes to be monitored through the servo module (DAC) analog output. See documentation
provided by Allen-Bradley on patch AMP, or contact Allen-Bradley customer support service.