Rockwell Automation 8520 9/Series CNC Integration Maintenance Manual Documentation Set User Manual
Page 692
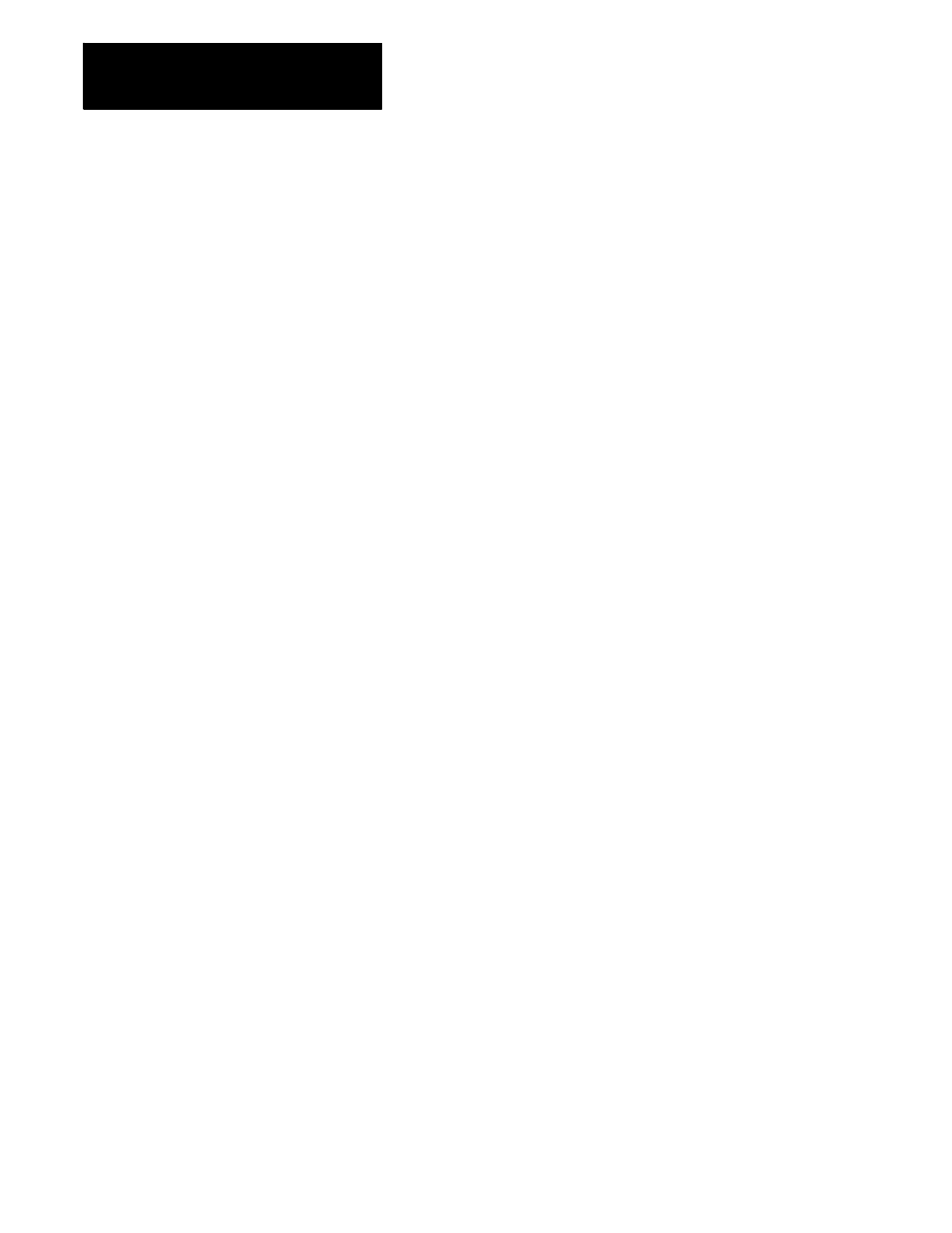
Section 14A
System Start-Up
14A-4
Important: The control will not come out of E-Stop if there is no PAL
program available for execution.
11. If the error message “SERVO POWER UP SEQUENCE ERROR” is
displayed on the operator panel CRT, verify that the AMP parameters
match the servo cabling.
12. Verify polarity of position feedback. Access the axis monitor page.
Feedback should count up when the axis is moved in the positive
direction and count down when the axis is moved in the negative
direction, when the encoder/resolver is installed. This is all relative
to axis direction assignment, rotation direction changes through
gearing, and encoder phasing.
Manually rotate the feedback device, check the axis direction and
corresponding feedback count. If the feedback count is counting up
when it should be counting down or counting down when it should
be counting up, then the value of AMP parameter SIGN OF
POSITION FEEDBACK should be changed to Minus.
13. Verify polarity of velocity feedback. On analog systems and digital
systems with one feedback device, the AMP parameter SIGN OF
VELOCITY FEEDBACK should always be the same as SIGN OF
POSITION FEEDBACK. On the system with more than one
feedback device, velocity feedback polarity should be determined by
turning the motor shaft and watching the sign of axis monitor display
parameter for Average Velocity Error.
14. Do a position calibration check. With the control in E-Stop, rotate
the servo until the marker found is indicated on the monitor page.
Record the position. While remaining in E-Stop, rotate the servo
until the axis moves a measured distance. Record the monitor
position. If the difference in monitor readings did not reflect the
correct axis displacement, AMP must be adjusted. Typically this is
the result of either axis calibration errors, incorrect number of
position feedback counts/rev entered, or incorrect gear ratio between
gear on motor shaft/lead screw thread pitch, etc...
15. If no error messages are displayed on the operator panel CRT, push
the E-Stop Reset button on the MTB panel. Check the CRT for
messages and watch for motor rotation. There should be no error
messages or motor rotation. If a motor rotates without a command,
immediately push the E-Stop button and check the motor and encoder
wiring for correct phasing.