Rockwell Automation 8520 9/Series CNC Integration Maintenance Manual Documentation Set User Manual
Page 691
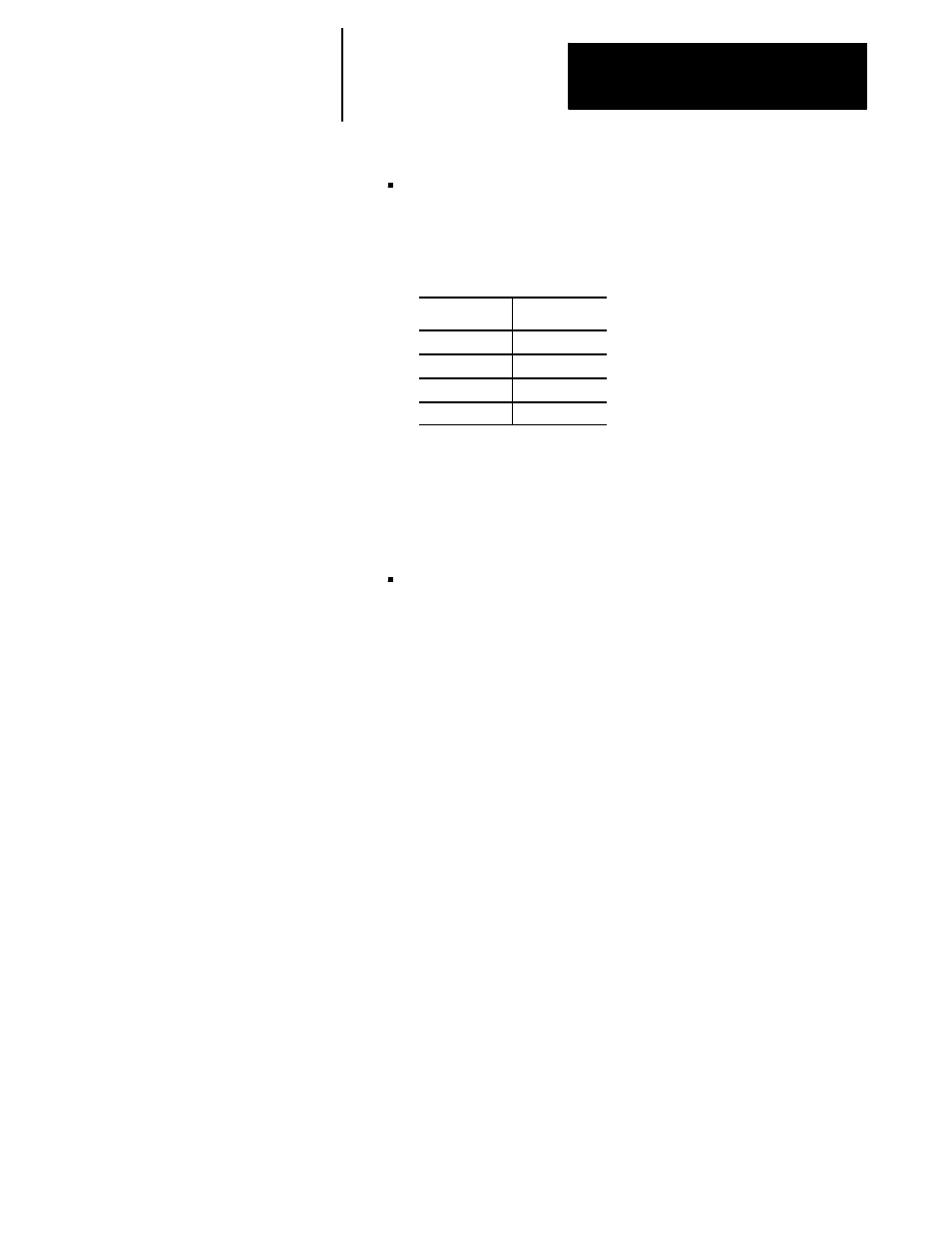
Section 14A
System Start-Up
14A-3
1394 Drive
Power terminal block
W1 and W2
24 V ac or dc
and check test points on the wiring board:
TB3 Test Point Voltage
TB3-1
+5V dc
TB3-2
Common
TB3-3
+15Vdc
TB3-4
--15Vdc
The status LEDs on the axis modules should flash red and green
alternately, indicating the system is ready and waiting for full bus
voltage. The Status LED on the system module should be red.
The system module LED only illuminates when a fiber optic ring
fault occurs. It should be off anytime the CNC is powered up.
9/440 CNC/drive systems
Assuming you wired your 9/440 as discussed starting on page
5A-28, power should be applied to your on/off control assembly
but no drive power should be present. Both 24 V logic power and
three phase should not be available to the system module at this
point.
After performing the above checks:
7.
Make sure the E-Stop button is depressed. Using the “ON” button on
the MTB panel, turn on power to the control. The main menu screen
should appear after the CRT warms up. For 1394 systems, the system
module LED should turn off provided the fiber optic ring is
functioning correctly. On 9/440 CNC systems, the status LED as
well as the Xilinx and Watchdog LED should all be on.
8.
If using a 1394 digital drive (not available for 9/440 CNC) check the
1394 I/O device monitor page to check fault status and addressing
(see page 15A-29).
9.
Using ODS, assign the AMP parameter values for each axis, then
download the prepared AMP file to the control. Refer to the
download section in the AMP manual for more information on
downloading AMP files.
10. Download a “minimum” PAL program to the control. Refer to the
download section in the PAL manual for more information on
downloading a PAL program. This program should contain basic
rungs to handle MTB panel, E-Stop, axis unclamp, etc.