Rockwell Automation 8520 9/Series CNC Integration Maintenance Manual Documentation Set User Manual
Page 267
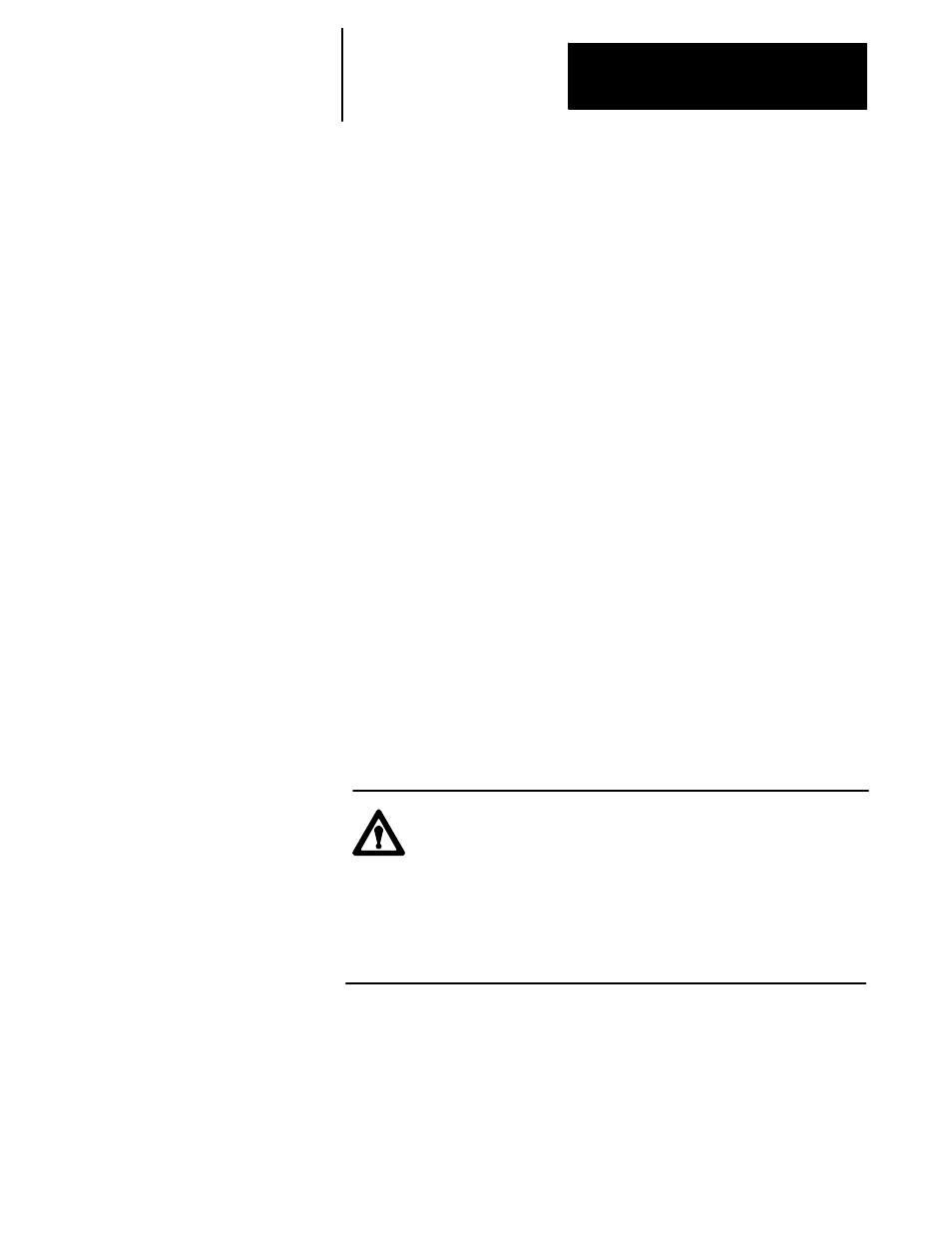
Section 5A
9/440 Resolver--based CNC/Drive System
5A-21
The time delay between the 9/440 resolver--based control receiving the
touch probe trigger and latching the current axis position is negligible.
However, you should be aware of any external delays that may introduce
position “staleness” in the probing operation, especially at high probing
speeds.
It is a good idea to establish an offset for the distance between the actual
location, as sensed by the probe at a very low speed, and the location
sensed by the probe at the intended probing speed. The offset can then be
added or subtracted to any future values obtained through probing. This
helps make sure that if there are any external delays in the trigger signal,
the position staleness shows up as a constant position offset error and is
removed from the measurement (assuming the external delay is
repeatable).
The touch probe interface is intended for use with units that offer 5V dc
compatible solid state relay outputs (see Figure 5A.8). Other
configurations can be supported as long as the user operates within the
published electrical specifications.
The touch probe circuitry resident on the 9/440 resolver--based control
only responds to the trigger probe edge changes. Polarity transition (high
to low or low to high) is selectable through the AMP parameter Probe
Transition. Specify the probe transition in AMP as rising edge or falling
edge. Once the active edge occurs, position data is captured by the
module, and additional occurrences of the trigger signal have no effect
until the probe is re-enabled under program control.
Refer to the 9/Series CNC AMP Reference Manual, publication 8520-6.4,
for more information.
ATTENTION: It is preferred, from a safety standpoint, that the
touch probe relay be closed at rest and open when the touch
probe stylus deflects. Then, if a wire breaks or shorts to ground,
it will appear to the system as a probe fired and the probing
cycle in process will stop commanding motion towards the part.
The user should make every effort towards the fail-safe
operation of the touch probe. Not all vendor’s touch probe
control units conform to this safety consideration.