GE Industrial Solutions DV-300 DC Drive Users Manual User Manual
Page 356
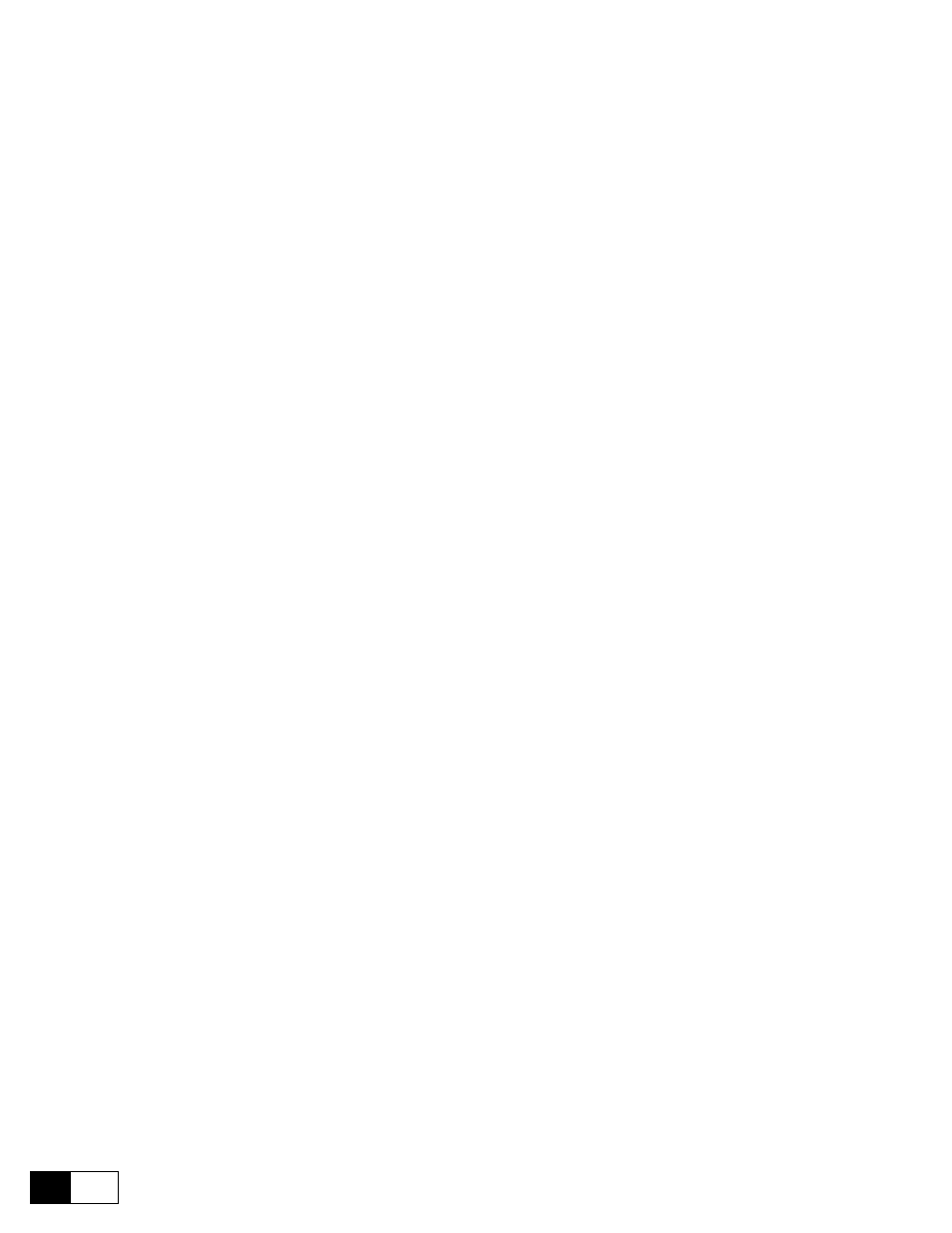
GEI-100332Ga
——— TROUBLESHOOTING ———
8
6
FAILURE
POSSIBLE CAUSES
The motor reaches the maximum speed immediately
Reference value set via terminals: Check whether the value varies from min. to max. value.
Potentiometer used for reference value setting: is there a 0V connection present?
Encoder/tachometer not connected, or incorrectly connected or not supplied:
Preset the Actual spd parameter in the DRIVE STATUS menu.
With the regulator disabled turn the motor clockwise (viewed from the front of the
shaft). The value indicated must be positive.
If the indicated value does not change or if inexplicable values are shown, check the
power supply and the cabling of the encoder/tachometer.
If the indicated value is negative, reverse the encoder connections. Exchange channel
A+ and A- or B+ and B-. Using a tachometer change the conductor polarity.
The motor accelerates too slowly
Ramp set incorrectly
Motor running at max. current
Motor overloaded
Converter too small
The motor decelerates too slowly
Ramp values and times incorrectly set
Braking current too low
With twoquadrant drives: moment of inertia too high.
The motor turns slowly even though the reference value = zero
Minimum speed selected
Interference due to unused analog input. Remedy: set unused analog inputs to OFF
Disconnect reference value on used analog input
If drive now stands still, the effect is due to the cable resistance
of the 0V cable.
If the drive is still turning: check if the speed reference is zero.
If it is not zero set Offset input xx parameter so that the drive
stands still. If it is zero set Spd offset parameter.
The motor thermic is active
Overloaded motor
Motor thermic protection relay incorrectly scaled
The motor is not supplying the max torque and the max power
Drive working at current limit
Check whether the value for Full load curr in the CONFIGU-
RATION menu is set correctly
Check the value for the current limitation