GE Industrial Solutions DV-300 DC Drive Users Manual User Manual
Page 273
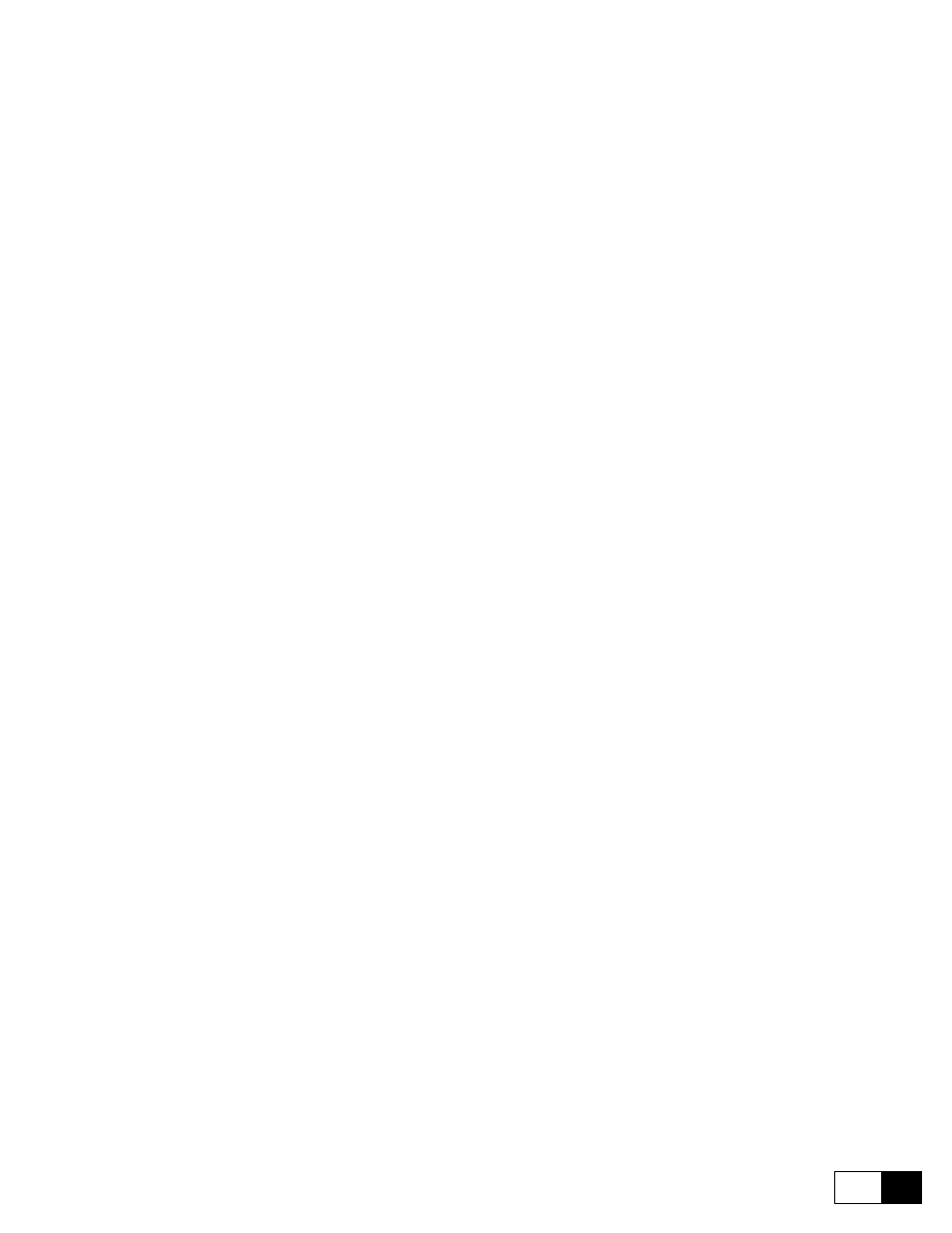
DV-300 Adjustable Speed Drives
——— FUNCTION DESCRIPTION ———
6
145
PI steady delay
Time for which the gains P init gain PID and I init gain PID have been kept operative
after overcoming the feed-forward PI steady thr threshold.
The delay time PI steady delay and the resulting function of initial gains changing also,
operate on the transition L to H of the Enable PI PID parameter.
P init gain PID
Initial proportional gain. P init gain PID operates when feed-forward is less than PI
steady thr and at its overcoming, for the time set in PI steady delay or on the transition
L to H of Enable PI PID for the same time.
I init gain PID
Initial integral gain. I init gain PID operates after the threshold PI steady thr has been
overcome or on the transition L to H of Enable PI PID for the time set in PI steady
delay.
PI central v sel
Output selector of the starting PI block. PI central v sel (0...3) selects between the 4 possible
settings of the initial value of the regulator integral component (corresponding to initial
diameter).
PI central v sel can be set directly from keypad, serial line or through two digital inputs set respectively as PI
central v S0 and PI central v S1.
Selecting PI central v sel = 0, when PI block is disabled (Enable PI PID = Disable), the last value of the integral
component calculated (corresponding to roll diameter) is stored. This value is displayed in PI output PID. When
enabled again, the regulation restarts again from that value. The same functionality is used when switching off
the drive . This kind of operation can be used when controlling a winder and it is necessary to stop the machine
and disable the drives or even remove AC incoming power from the electrical cabinet.
Selecting PI central v sel = 1-2-3, when PI block has been disabled, the value of PI output PID will be set at
what is programmed in the correspondent parameter (x1000). When the drive is restarted after a power off, the
precalculated value will be automatically set only if, when powering up the drive, the digital input programmed
as Enable PI PID is already set at a high level.
PI central v 1
Setting of the first initial value of the regulator’s integral component (corresponding
to initial diameter 1). The PI central v 1 value must be included in the limits set in
PI top lim PID and PI bottom lim PID.
PI central v 1 will be selected by setting PI central v sel = 1.
PI central v 2
Setting of the second initial value of the regulator’s integral component (corresponding
to initial diameter 2). The PI central v 2 value must be included in the limits set in
PI top lim PID and PI bottom lim PID.
PI central v 2 will be selected by setting PI central v sel = 2.
PI central v 3
Setting of the third initial value of the regulator’s integral component (correspondent
to initial diameter 3). The PI central v 1 value must be included in the limits given by
PI top lim PID and PI bottom lim PID.
PI central v 3 will be selected by setting PI central v sel = 3.
PI top lim
It defines the higher limit of the adapting block of the PI correction.
PI bottom lim
It defines the lower limit of the adapting block of the PI correction.
The output of the PI block represents the multiplier factor of feed-forward, whose value must be adapted from
the regulator in the max. limits included between +10000 and -10000 and defined by PI top lim and PI bottom
lim. The value of these parameters will be defined according to the system that has to be controlled. For a better
understanding please refer to the paragraph “Examples of application”.