GE Industrial Solutions DV-300 DC Drive Users Manual User Manual
Page 291
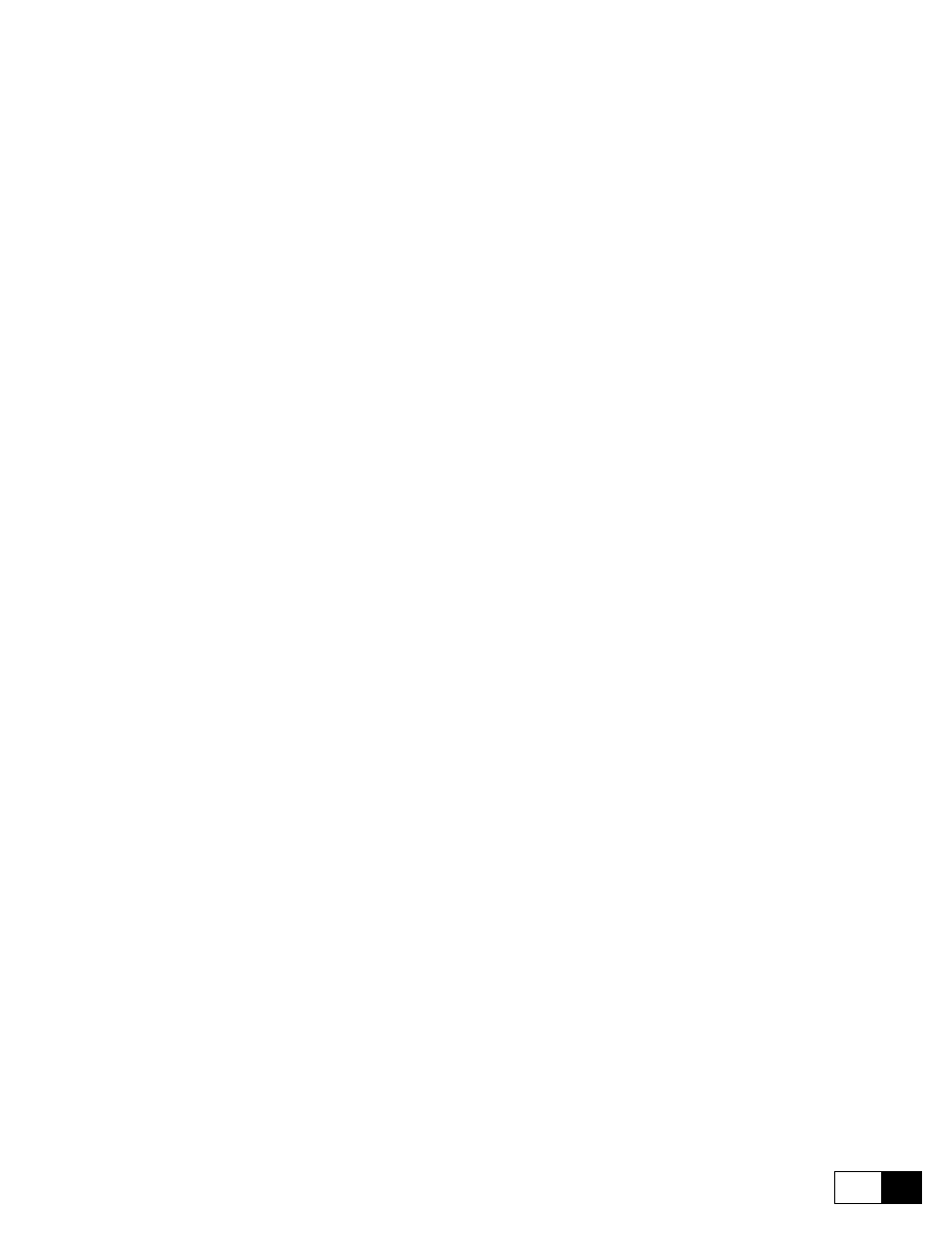
DV-300 Adjustable Speed Drives
——— FUNCTION DESCRIPTION ———
6
163
Mantaining a 15% margin as to the saturation limit of the regulator (10000 count), it is necessary to set PID
source Gain so that Feed-fwd PID reaches, along with the max. analog value on Analog input 2, 85% of its
max. value.
When an analog input is set on a PAD parameter , this will have a max. value +/- 2047.
So:
PID source Gain = (max Feed-fwd PID x 85%) / max PAD 0 = (10000 x 0.85) / 2047 = 4.153
The speed reference of the motor is set in RPM x 4, so program as follows:
PID out scale = (2550 x 4) / (10000 x 0.85) = 1.2
Set PID target as 1 Speed ref 1.
n
ote
:
When the ramp function has been enabled, Speed ref 1 is not available. To keep it available
it is necessary to set the parameter Enable ramp = Disable.
For PID target set the parameter number to which it will be associated, choosing it from the list of paragraph
10.4. “List of high-priority parameters” (Speed ref 1 has the decimal number 42).
To obtain the correct value it must be added the decimal number 8192 (fixed offset):
PID source = (8192 + 42) = 8234
Set PI central v sel = 0.
With this configuration, having a correction proportional to the line speed, the PI block is not able to position the
dancer at speed = 0. In order to do the drawing in stop conditions, it is necessary to use the PD block.
As previously stated, the procedure determines the theorical multiplier factor (PI output PID) of feed-forward
as relation of the diameter calculated. In order to send to the drive the correct speed angular value.
n
ote
:
When PI central v sel = 0 has been selected and the the PI block has been disabled, the system
keeps in memory, or reset automatically in case of switching off, the last value calculated
for PI output PID. If it would be necessary to set the value in order to have at the output an
incorrect reference and so equal to the feed-forward, it is possible to configure a digital input
as correction reset.
So configure:
Digital input 4 = PI central v S0
PI central v 1 = 1.00
Bringing the digital input to logical high level, the PI output PID will be reset.
Set PI top lim and PI bottom lim according to the ratio diameters coil.
Parameters PI top lim and PI bottom lim can be considered as multiplier factors, respectively max. and min.
of the feed-forward.
Considering that the angular speed of the motor and the corresponding reference, change inversely to the un-
winder/winder diameter;
Set: PI top lim = 1
PI bottom lim = Φ
min
/ Φ
max
= 100 / 700 = 0.14
Below is an explanation of above settings.
Calculation of the angular speed of the motor:
ω
max. = Vl / (π x Φ
min
x R)
and
ω
min
= Vl / (π x Φ
max
. x R)