Yokogawa Data Acquisition with PID Control CX2000 User Manual
Page 162
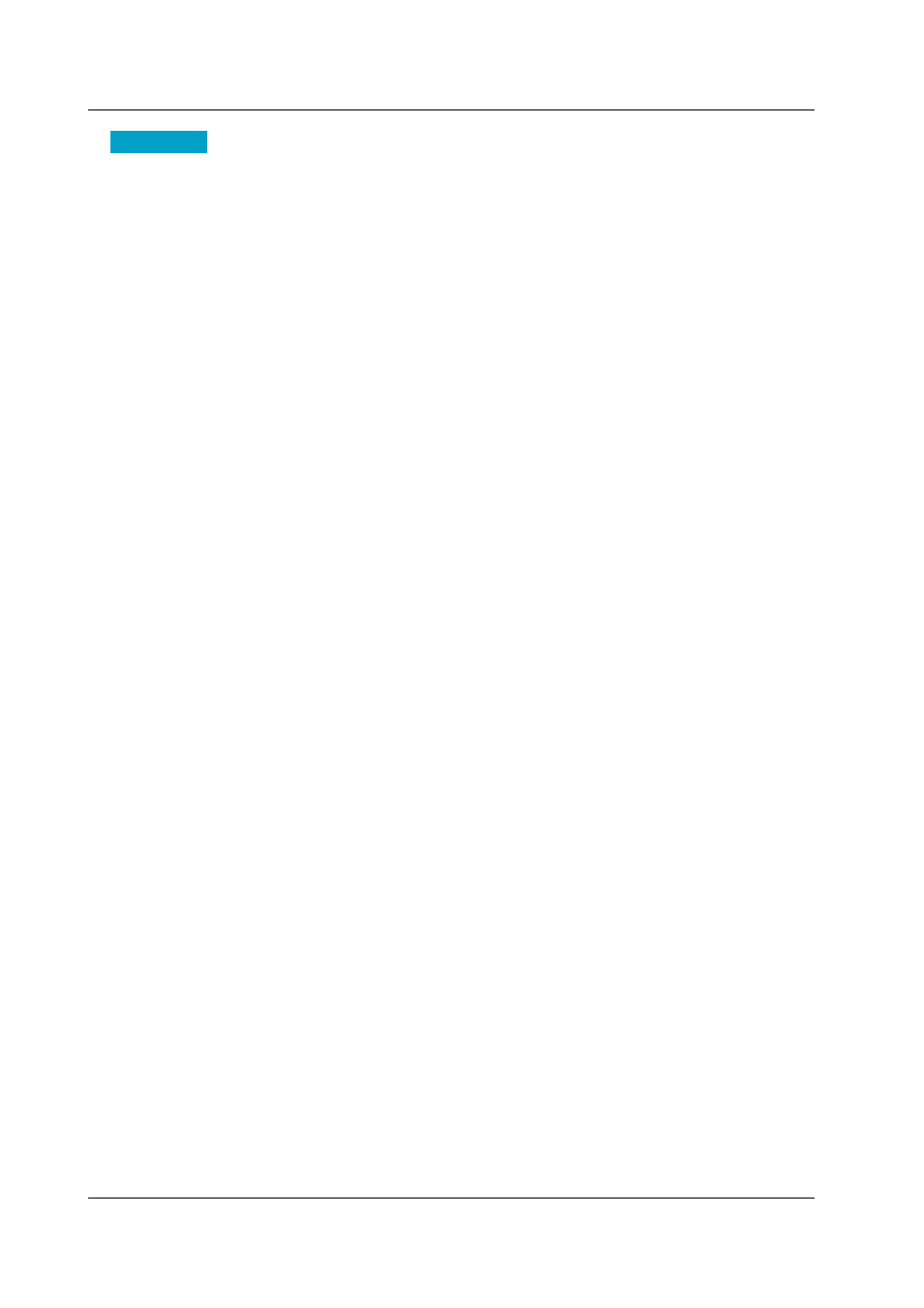
4-2
IM 04L31A01-01E
Setup Items
Setting Control Action Related Parameters
• PID number
Set the maximum control parameter group number to be used in the range of [1] to [8]
(initial value is 8).
• Control period
Select the control cycle from [250ms], [500ms], and [1s] (initial value is 250ms). However,
if basic setting mode > [#1 Alarm, A/D, Temperature] > [A/D Integrate] in basic setting
mode is set to [100ms], the control period is fixed to [1s] and is not selectable.
• Zone PID
Set the PID selection method by turning [Off]/[On] the Zone PID.
Off (initial value): Target setpoint selection
If program control is ON on models with the program control option,
this becomes “segment PID.”
On:
Zone PID
For the procedure in setting the reference point of the zone PID,
see section 4.8, “Operation-related parameters/Zone PID.”
• Restart mode
Select the action of the fixed-point control loop after recovering from an extended
power failure from [Continue], [Manual], [Auto] (initial value is Continue).
Continue: Continue the operation before the power failure occurred.
Manual:
Start from a manual operation condition (control output is set to preset output).
Auto:
Start from an auto operation condition (start the control output from preset
output and resume control computation based on the preset output).
• Restart mode (Program)
← Only on models with the program control option
Select the restart mode (recovery behavior) the CX2000 will enter when recovering
from a power failure when program operation is performed. Select [Continue],
[Manual], or [Reset] (initial value is Continue).
Continue: Continue the operation before the power failure occurred.
Manual:
Start from a manual operation condition (control output is set to preset output).
Reset:
Start program operation from a reset condition (control output is set to
preset output).
• Initial PID
Select [Temp] or [Press+Flow] (initial value is Temp) for the initial value of the PID
constant (see page 4-24). Below are the initial values of PID constants. The PID
constant is also initialized to the following value when [Initial PID] is changed.
Initial values for temperature: P = 5.0%, I = 240 s, and D = 60 s.
Initial values for pressure flow: P = 120.0%, I = 20 s, and D = 0 s.
• 6/4 loop select
(set only on 6-loop models)
Select [6loop] or [4loop] (initial value is 6loop) for the number of loops used.
• Auto tuning
Select [On] (initial value is Off) to enable the auto-tuning function of the PID constant.
• Loop number
The [Control mode], [Program control], and [PID control mode] parameters are set for
each loop. When changing these parameters, this setting is used to select the target
loop number [1] to [6] (initial value is 1). The loop number is displayed up to the
number of loops you specified at the time of purchase.
• Control mode
Select a control mode of [Single], [Cascade], [PVSwitching] (initial value is Single), or
[Retrans] (Style Number S3 or later). Select [Off] for the loops that are not to be controlled.
Different control modes (except for [Retrans]) cannot be specified on the two loops
within the single control output terminal block. If you specify [Cascade], both loops
are set to [Cascade]. You cannot select [Cascade] or [PVSwitching] for loop [5] or [6].
4.1 Control > Control action, Input setting