Festo Контроллер позиционирования CPX-CMAX User Manual
Page 412
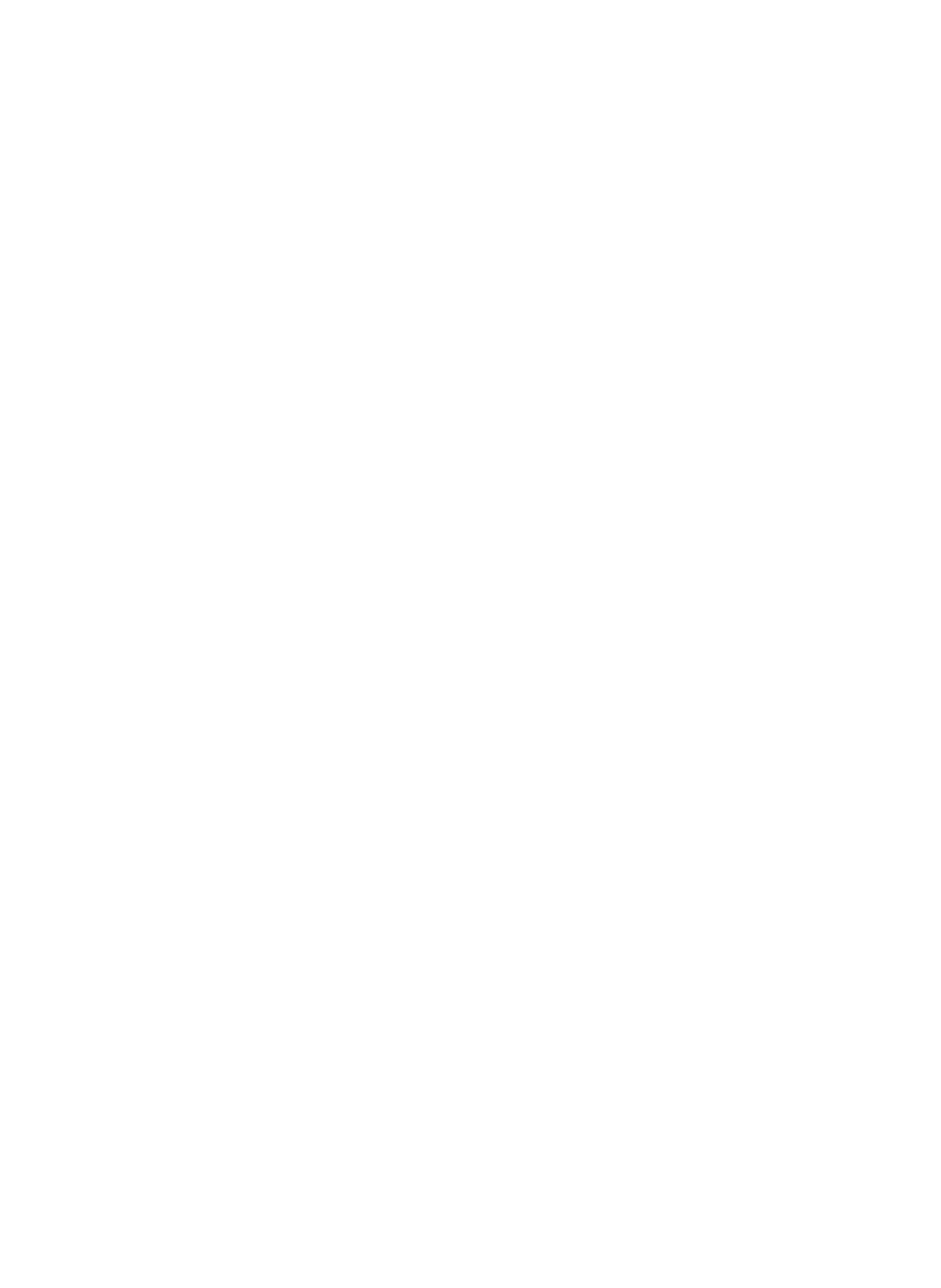
C. Configuration with CPX node
C−14
Festo P.BE−CPX−CMA X−CONTROL−EN en 0908NH
Sequence:
1. Ensure that the command box is currently not being used.
In case several modules are parametrised via the comĆ
mand box in a PLC program, you must apply an appropriĆ
ate method to ensure that only one module is accessed at
a time. Since the command box is set permanently", a
PLC program should allocate data to the box, transfer the
data and then enable it again. A global flag may be suffiĆ
cient for this purpose.
2. Allocate data to the command box. Mark the box as alloĆ
cated within the PLC. Then transfer the slot number of the
module, the index of the module parameters and the
offset of the data to the command box.
3. Compile the task (byte 8 to 61) according to the function
number. Bytes that are not used must also be transferred,
they should be set to zero.
4. Write the task data into the Write Box. These are then
automatically transferred to the module.
5. Read the data from the Read Box. If the status byte PSB
does not equal 0, the task is performed. Check for possĆ
ible errors (PSB <0)!
6. If the PSB = 0, another status must be requested −> (5).
7. If another task is to be performed: −> 3.
8. If all the tasks have been performed, the command box
must now be enabled.
The data in the command box should be deleted, i.e. set
to 0. This is not mandatory, but prevents the possibility of
module data being overwritten due to a faulty access to
the Write Box.