B.8.6 position control during a force task, B.8.6, Position control during a force task – Festo Контроллер позиционирования CPX-CMAX User Manual
Page 389: B−47
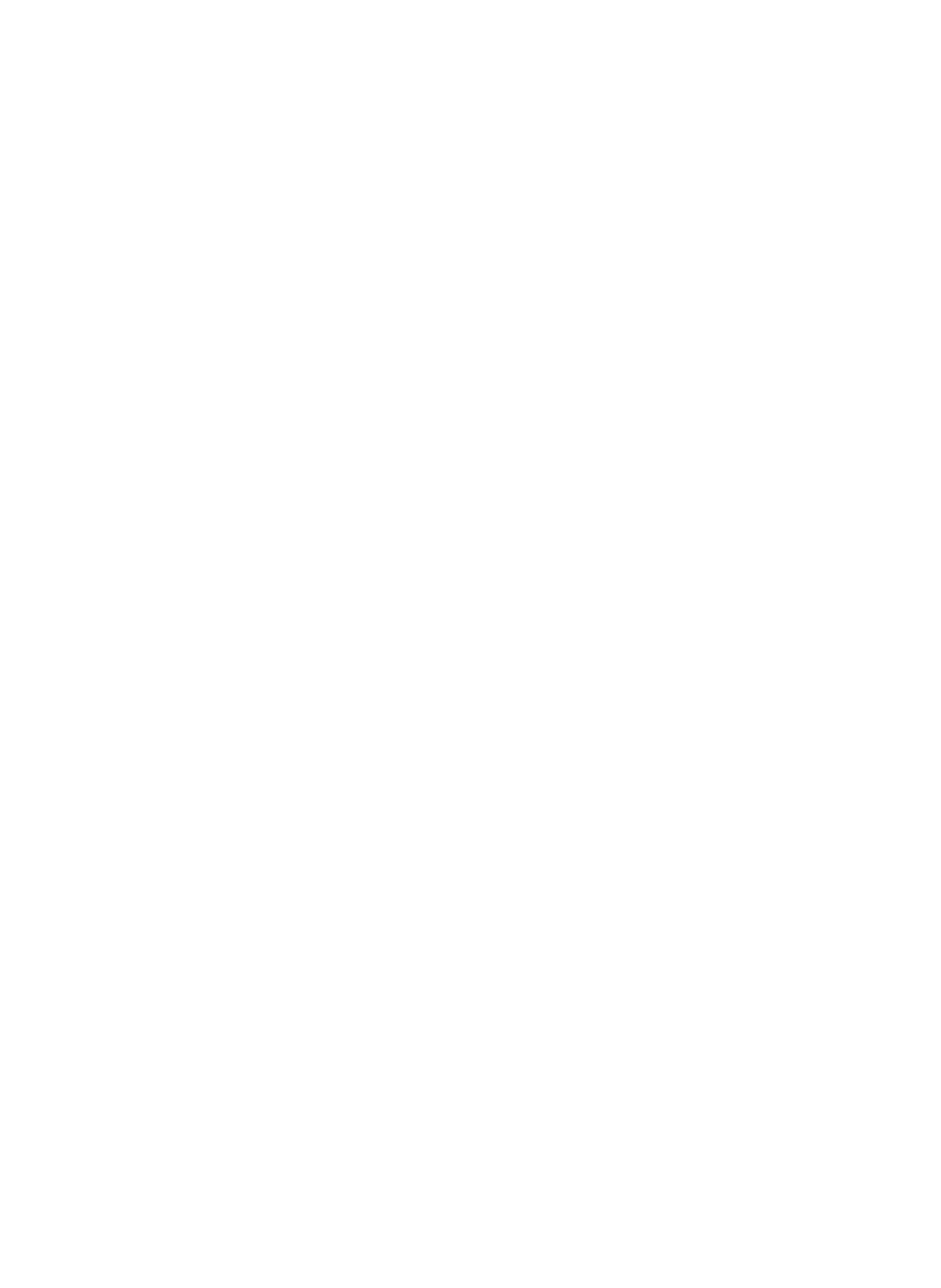
B. Basic controlling principles
B−47
Festo P.BE−CPX−CMA X−CONTROL−EN en 0908NH
B.8.6
Position control during a force task
If during a force task the drive exceeds the setpoint speed
V
vor
in the active direction of the force, e.g. because the drive
is still at a small distance to the workpiece and the drive
starts to move due to the missing counteracting force, then
the system switches to position control. This occurs indepenĆ
dently of an MC being available or not. In this the hardware
end position in the direction of active force direction is used
as the setpoint position and the setpoint speed of the record
or the speed parameter in direct mode (PNU 406 or 554) is
used as the speed V
vor
. The drive then moves at speed V
vor
until high braking acceleration occurs (drive stops at a workĆ
piece), a standstill is recognised (speed in force direction is
smaller than 0.004 m/s for 20 ms) or the actual force reaches
the specified target force after a delay time of at least 10 ms
after reversing to position control. Then the force controller is
again activated, the force is (further) built up with the set
force ramp.
The monitoring functions configured for the force task
(stroke, speed, software end positions) are active also during
position control.
Position control is activated at the earliest 30 ms after the
force task starts (as a result of positive edge at CPOS.START
or start due to record sequencing). This time is required for
transient effects. Until then the force controller is always acĆ
tive.
Preventing position control
If the user wants to prevent reversing to position control, the
setpoint speed must be set to 0.000 m/s. This deactivates the
position control during a force task.