Rockwell Automation 8520-ARM2 9/Series CNC AMP Reference Manual Documentation Set User Manual
Page 735
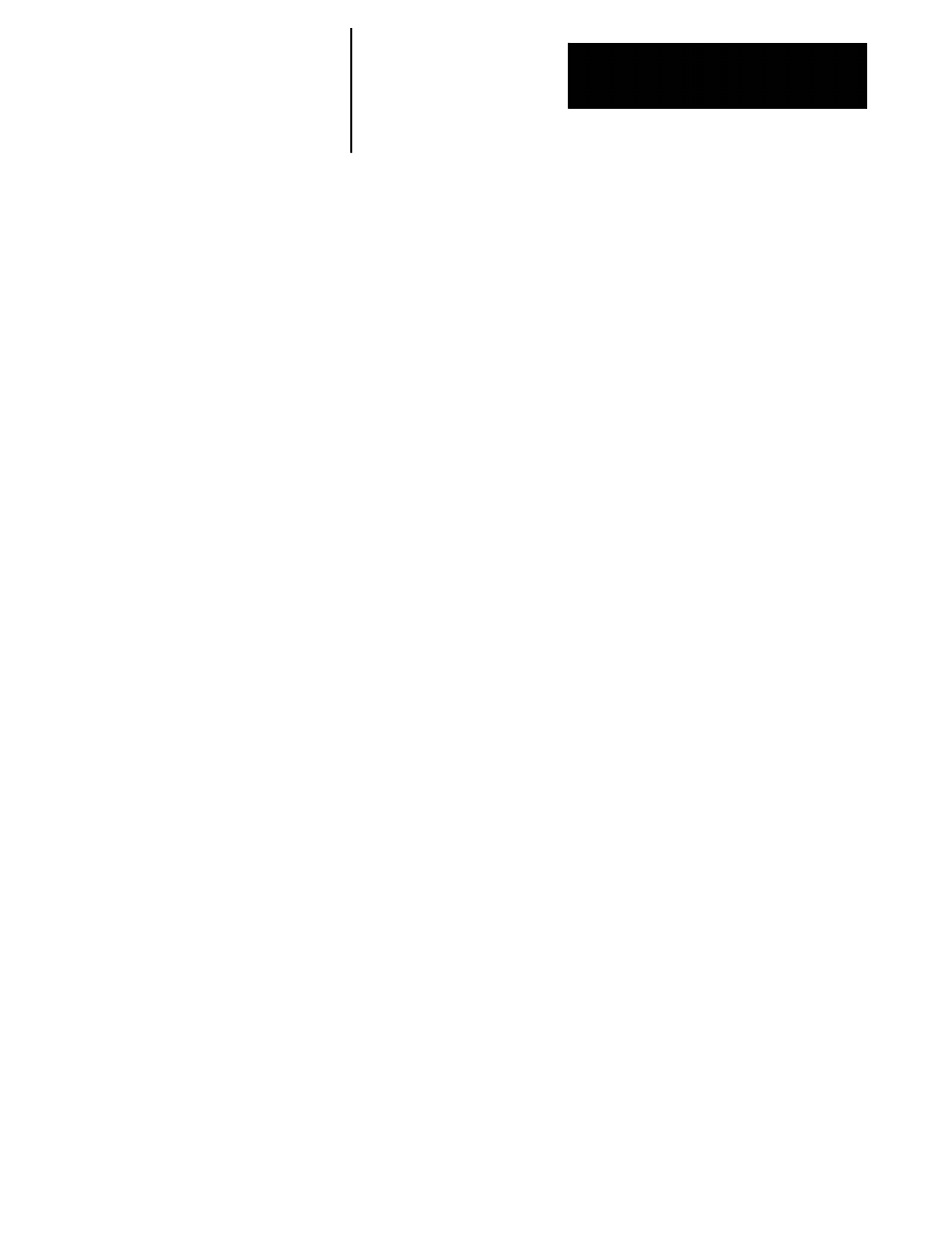
Tuning a Digital or Tachless Analog System
Appendix A
A-13
Smaller lighter systems may become very unstable. Chatter can
occur instead of the smooth overshoot curve shown in Figure A.1
which is typical of larger systems. With no integral gain, it is
doubtful you will see a stable curve on any type of system.
4.
Lower the velocity proportional gain to the highest value possible at
which only a slight velocity overshoot (or chatter) occurs. This is
your maximum velocity proportional gain value.
Tuning for Optimal Acceleration
Now that you know the maximum value for velocity proportional gain, you
can begin fine tuning the drive for optimal performance as follows:
5.
Up to this point the velocity integral gain has been at its minimum
value. Raise the velocity integral gain (see page 40-13).
6.
Lower the velocity proportional gain until the sharp overshoot occurs
again.
Continue raising the velocity integral gain by small increments.
Each time you raise the integral gain you should create a velocity
overshoot that can be detected on your strip chart recorder. Remove
the created velocity overshoot by lowering the velocity proportional
gain (strip chart recording performance as described previously while
running your tuning part program). Typical final velocity integral
values are between 5 and 10 times smaller than the velocity
proportional gain value.