Rockwell Automation 8520-ARM2 9/Series CNC AMP Reference Manual Documentation Set User Manual
Page 725
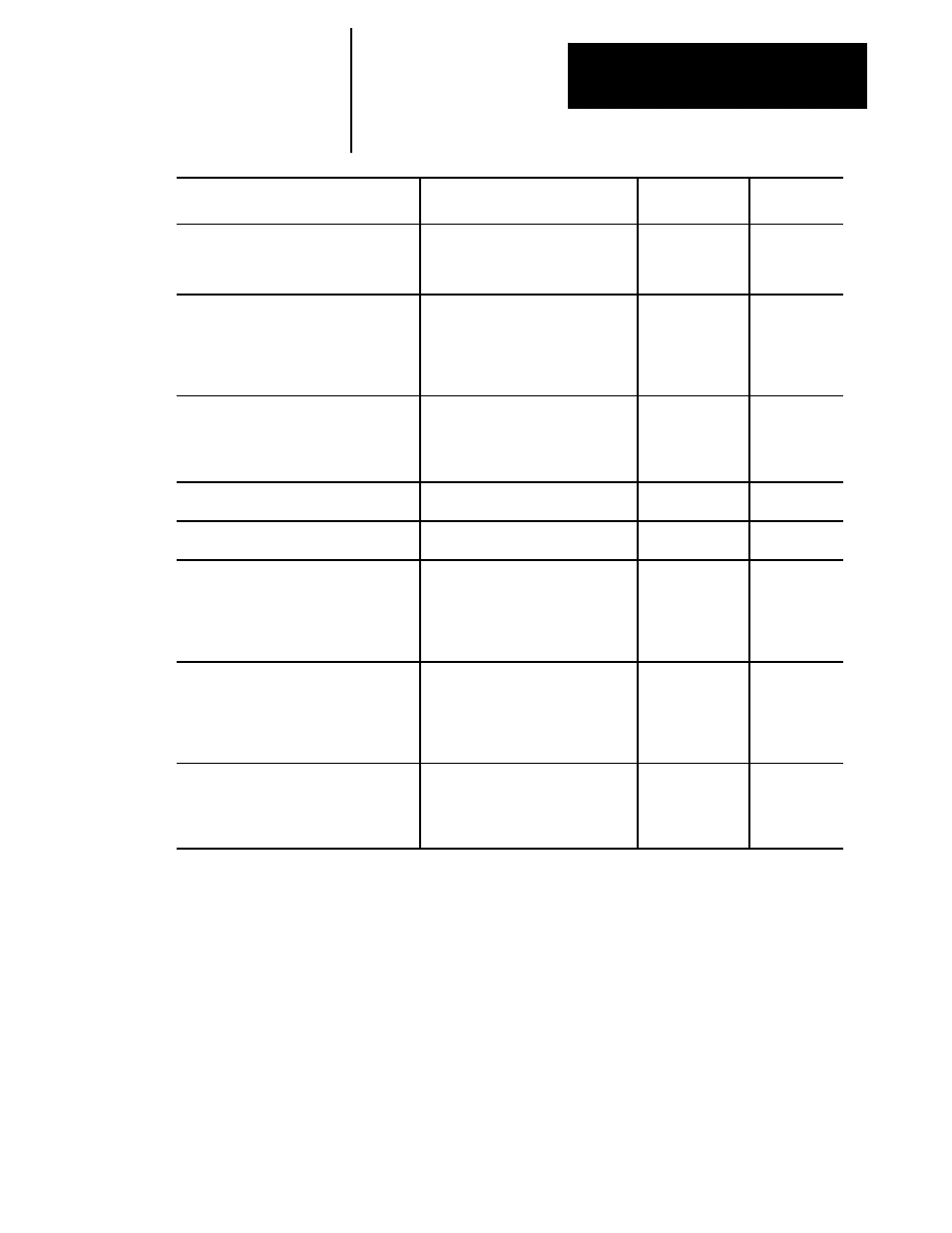
Tuning a Digital or Tachless Analog System
Appendix A
A-3
AMP Parameter
Page
For Tuning
Procedure:
Description
VE Integrator Discharge Rate
This parameter is used when a large
variation in load may occur on a moving
axis. It reduces velocity overshoot and
flattens the servo response curve.
Set to 1 (one)
7-75
Torque Offset Percentage
Use this parameter when there is a
continuous static load in one direction.
This parameter tells the control the
percentage of the servo’s maximum
torque which must be applied to
compensate for this load.
Set to 0 (zero)
7-80
Torque Offset Direction
Use this parameter when there is a
continuous static load in one direction.
This parameter tells the control the
direction to apply the torque offset
percentage.
Set to Plus
7-81
Max % rated torque (--)
Indicates the maximum torque limit for
the servo in the negative direction.
Set to final value
7-78
Max % rated torque (+)
Indicates the maximum torque limit for
the servo in the positive direction.
Set to final value
7-79
Analog Servo Pos. Voltage
Indicate the servo motor’s maximum
rated current in the positive direction
relative to amplifier output (what voltage
the servo card should signal the
amplifier to reach maximum motor rated
current).
Set to final value
7-58
Analog Servo Neg. Voltage
Indicate the servo motor’s maximum
rated current in the negative direction
relative to amplifier output (what voltage
the servo card should signal the
amplifier to reach maximum motor rated
current).
Set to final value
7-59
Peak Current as a % of RMS
Indicate the percent of the servo motors
nominal rated current (continuous duty)
the Analog Servo Pos. Voltage or
Analog Servo Neg. Voltage generate
(which ever is higher).
Set to final value
7-77