Rockwell Automation 8520-ARM2 9/Series CNC AMP Reference Manual Documentation Set User Manual
Page 663
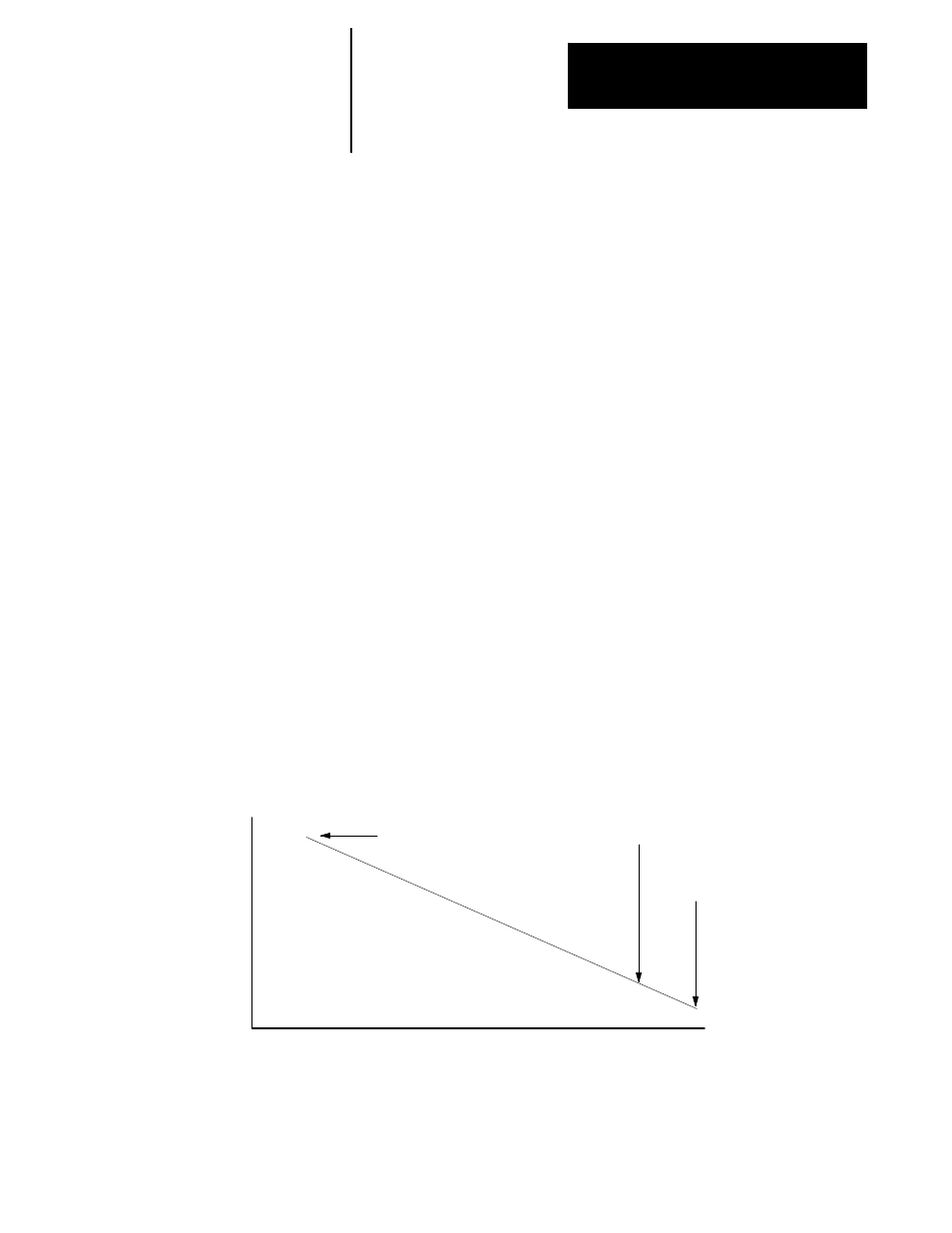
Miscellaneous Parameters
Chapter 37
37-23
Determining System Scan TIme
Once you have determined your system foreground time, you can use the
timer function on the control to determine the total part program time.
With this information, you can calculate the optimum system scan time for
your system. Use this procedure:
1.
Set the system scan time well above the expected final setting. Since
you know the system foreground time from the system timer screen,
you only need to estimate how long it will take the control to
complete background tasks and decode the part program. Add this
estimate to the system foreground time to set the system scan time.
2.
Press the {TIME PARTS} key and run your program as described in
your programming and operation manual.
3.
When the program finishes, note the CYCLE TIME value. This value
is how long it took the control to decode the part program.
4.
Lower your system scan time. This can be done with either Offline
AMP or Online Patch AMP.
5.
Run your program again and note the cycle time. It should be
slightly lower than the previous time.
6.
Repeat the sequence of lowering the system scan time and observing
the cycle time. As you lower the system scan time, the cycle time
decreases until the error message “Hardware Error #13” or
“Foreground Overlap” appears as shown in Figure 37.3. The point at
which you have the lowest cycle time and lowest system scan time is
when your system is running most efficiently.
Figure 37.3
Determining System Scan Time
Cycle Time in minutes
System Scan Time in ms
1:17
1:15
1:12
1:09
1:07
22
20
18
16
14
12
10
8
6
Optimal System Scan Time is when the
Cycle Time and System Scan Time are the
lowest before error messages appear.
Begin tracking the cycle time
when the system scan time is set
at the highest estimate.
”Foreground Overlap“ appears.
”Hardware Error #13“ or