A.5 tuning the drive – Rockwell Automation 8520-ARM2 9/Series CNC AMP Reference Manual Documentation Set User Manual
Page 733
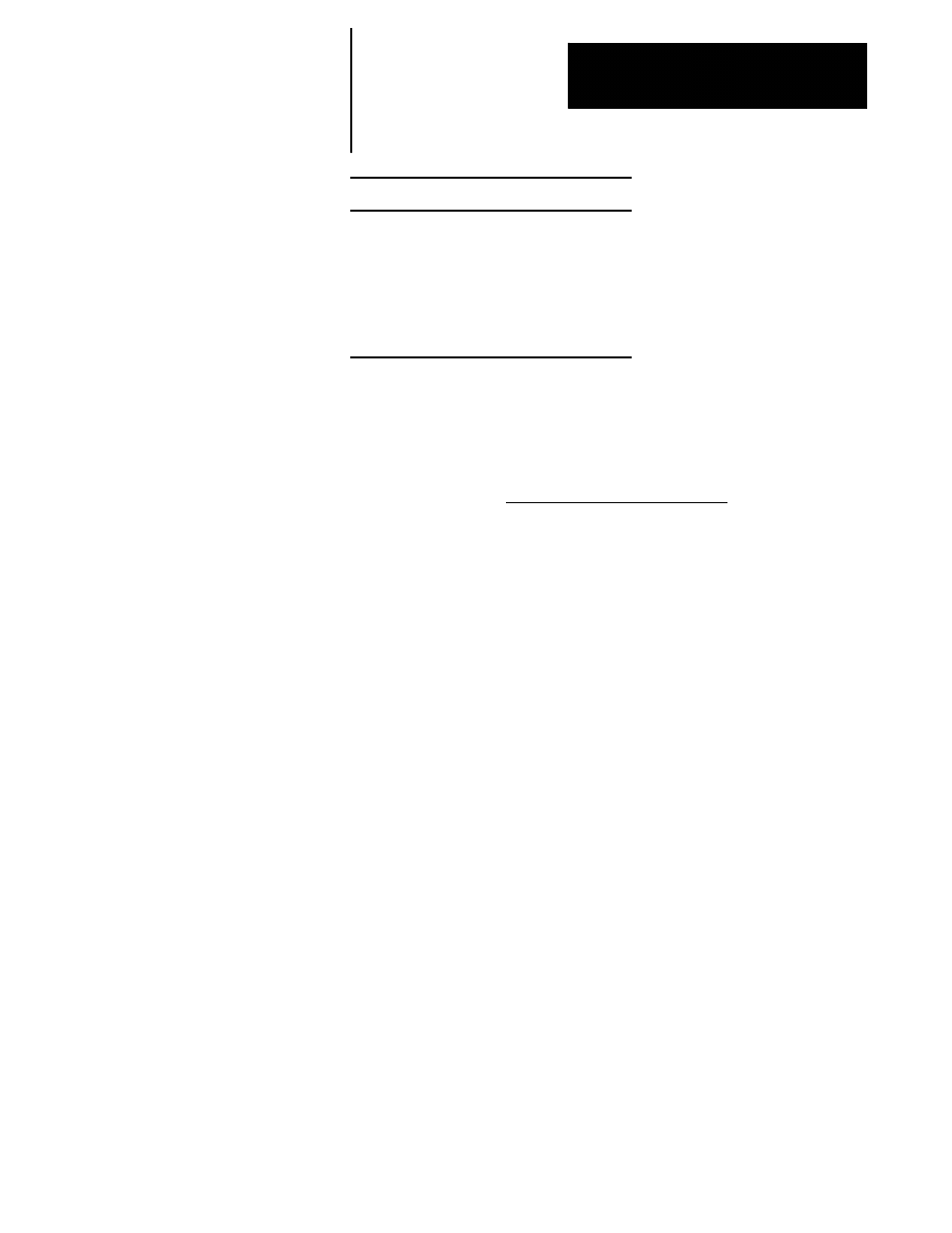
Tuning a Digital or Tachless Analog System
Appendix A
A-11
Example Tuning Part Program
N00001 G20 G94 G91 G94;
N00002 #100=0;
N00003 G01 X5 F1000;
N00004 G04 P1
N00005 X--5;
N00006 G04 P1;
N00007 #100=#100+1;
N00008 If [#100 LT 6] GOTO 3;
N00009 M02;
This procedure assumes you have AMPed your system as described above,
have the DAC monitor on and outputting velocity feedback for the axis
you are monitoring, and have your strip chart recorder connected.
You should have your velocity integral gain set to zero and your
proportional gain set at around 1500 (you can adjust these using online
AMP see page 40-13). Tuning is performed on a cutting move (G01) at
the maximum cutting feedrate. You should not actually be cutting material
for this procedure. A G01 cutting move is used so that the control uses
linear acceleration for tuning instead of the exponential acceleration that is
used for rapid moves.
We also recommend that for the purpose of tuning you disable the Torque
Filter Cutoff Frequency that you may have enabled using AMP (set it as
high as possible to disable) and set the VE Integrator Discharge rate to 1.
You can add these features once the optimal acceleration curve is found.
You can tune the velocity loop with the position loop open or closed. We
recommend tuning with the position loop closed since better servo
performance can be obtained in this fashion.
A.5
Tuning the Drive