Rockwell Automation 8520-ARM2 9/Series CNC AMP Reference Manual Documentation Set User Manual
Page 150
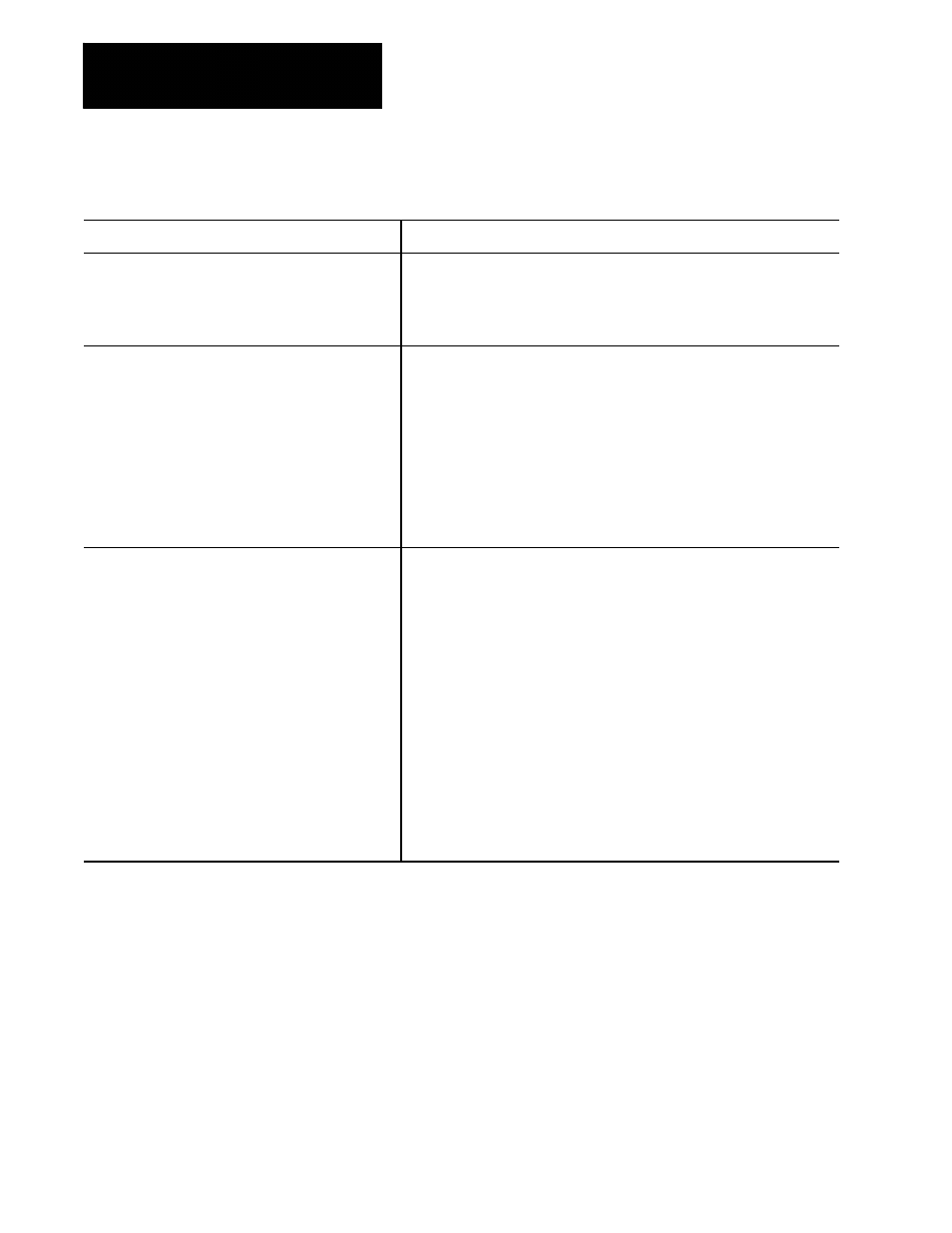
Servo Parameters
Chapter 7
7-4
The loop types supported include:
Servo Loop Type
Description
Position or Analog Spindle
Two feedback devices
This is the most common analog configuration. With this method, the velocity
feedback is generated by a motor--mounted tachometer and the velocity loop is
closed by the motor drive system. Position feedback is generated by an encoder
either mounted on the motor shaft or at some other point on the axis and the
position loop is closed by the CNC.
Position/Velocity
One feedback device
This is the most common digital configuration with standard AB digital motors,
though it can also be used for analog systems. Use this selection when the CNC is
to close the position loop and velocity loop (also motor commutation for digital
systems). With this method, the control derives position and velocity feedback
from the same feedback device. This is selected by assigning the same feedback
port for both position and velocity feedback. When this is done, all parameters to
configure velocity feedback must be identical to the parameters configuring
positioning feedback, i.e., Velocity Feedback Counts/Cycle, Velocity Feedback
Type
, should be the same as Position Feedback Counts/Cycle, Position
Feedback Type
, etc. This option may also be selected when using an
Allen--Bradley 1394 digital servo drive as a spindle.
Important:
This selection is not applicable to the 9/440 high--resolution CNC.
Digital
or Digital Spindle
Two feedback devices
With this method, the control derives positioning feedback from one feedback
device and velocity data from a second feedback device. This requires that the
velocity and positioning feedback return to different feedback ports. When this is
done, the positioning and velocity feedback parameters must be assigned
independently for the two different feedback devices. Velocity feedback must
come from the feedback device mounted on the servo motors.
An example of where a two-feedback device system might be used is an axis that
has a high-precision feedback device mounted directly on the ball screw or
machine bed, providing positioning feedback, and a separate encoder mounted on
the motor shaft, providing the velocity feedback. The positioning feedback would
provide increased positioning accuracy because it would be unaffected by
mechanical “slop” through the motor and drive train. Motor stability could be
managed by the control because the velocity feedback would be coming directly
from the motor shaft.
Important:
Analog systems can not use a tachometer for velocity feedback to the
control. Only encoder signals can be used for feedback to the 9/Series CNC.
Both the velocity feedback and positioning feedback for an axis must be returned
to the same servo module as the servo’s output port.