Rockwell Automation 8520-ARM2 9/Series CNC AMP Reference Manual Documentation Set User Manual
Page 620
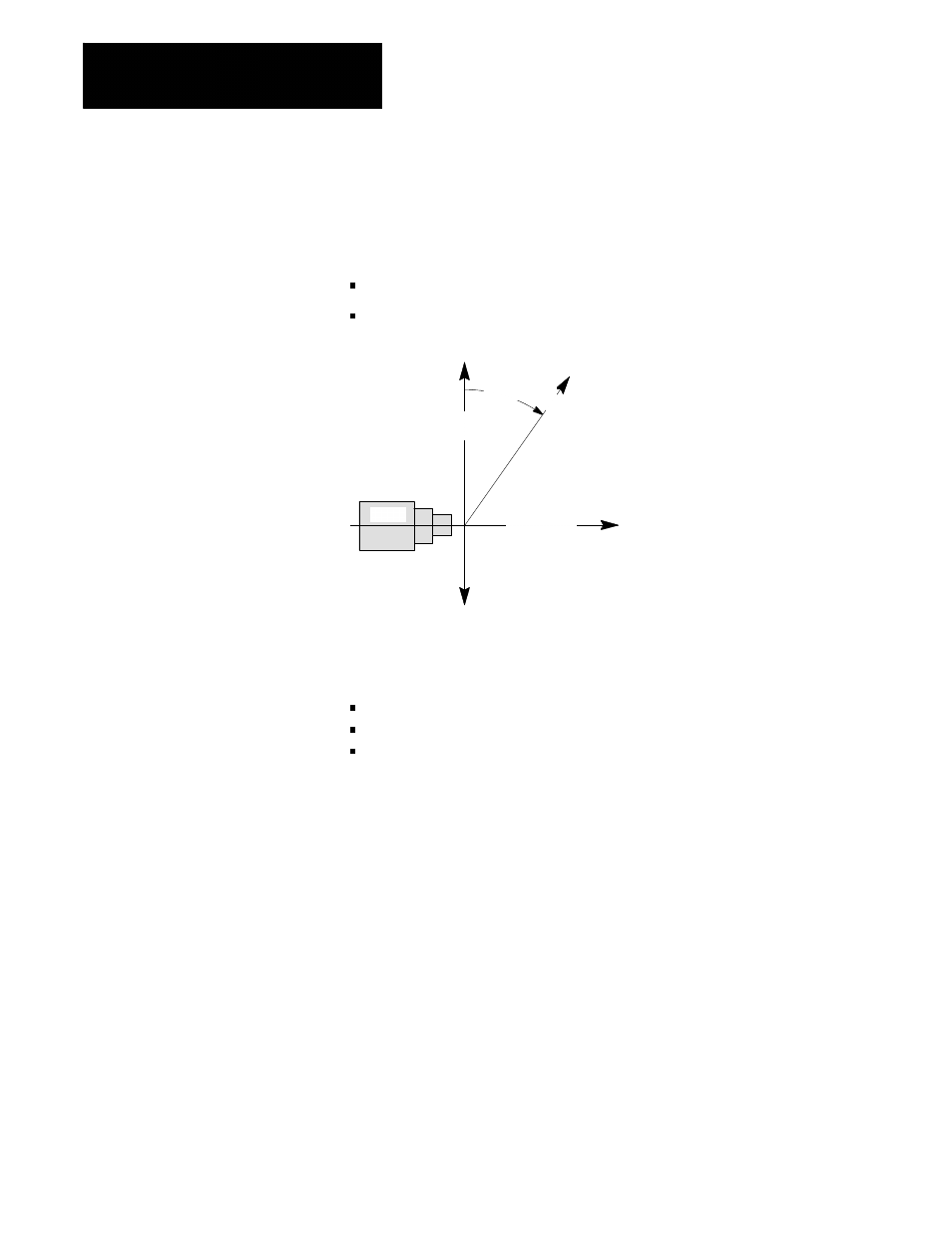
Angled Wheel Parameters
Chapter 35
35-8
Notes
Configure this rotary axis so that when positioned at angle zero the wheel
axis is at 90 degrees to the part spindle centerline. Accomplish this by
either:
physically moving the home limit switch or
offsetting the home position on the rotary axis using the parameters
Home Calibration and Axis Position After Homing.
Virtual Axis
(typically X)
Part
Wheel Axis
(typically W)
Wheel Axis
Angle +q
Axial Axis
(typically Z)
+X
--X
180°
0°
90°
The position of this rotary axis should range from 0 to 180 degrees. An
error is generated if you attempt to activate angled-wheel mode and the
wheel axis angle is:
less then 0 degrees
greater than 180 degrees
approaching an angle of 90 degrees
The closer the wheel axis angle is to 90 degrees, the more transformed
motion must occur on the axial and wheel axes to perform virtual axis
moves. Depending on the axis display resolution for your system, wheel
axis angles approaching 90 degrees can result in transformed axis moves
larger than can be displayed on the position registers. When this occurs the
position registers change to dashes.
This angle is checked by the control only when angled-wheel mode is
entered. This angle can not change during angled-wheel mode (the rotary
axis is disabled for programmed motion, PAL axis mover, and jog moves).
You must home this rotary axis before you can enter the angled wheel
mode, and before the X, Z, and W axes can be positioned.
The resolution of the wheel axis angle is determined by the rotary axis
resolution. This resolution is determined with the AMP parameter Axis _
Word Format found in the Axis Program Format group.
This is a global parameter. The value set here applies to all axes.