Rockwell Automation 8520-ARM2 9/Series CNC AMP Reference Manual Documentation Set User Manual
Page 159
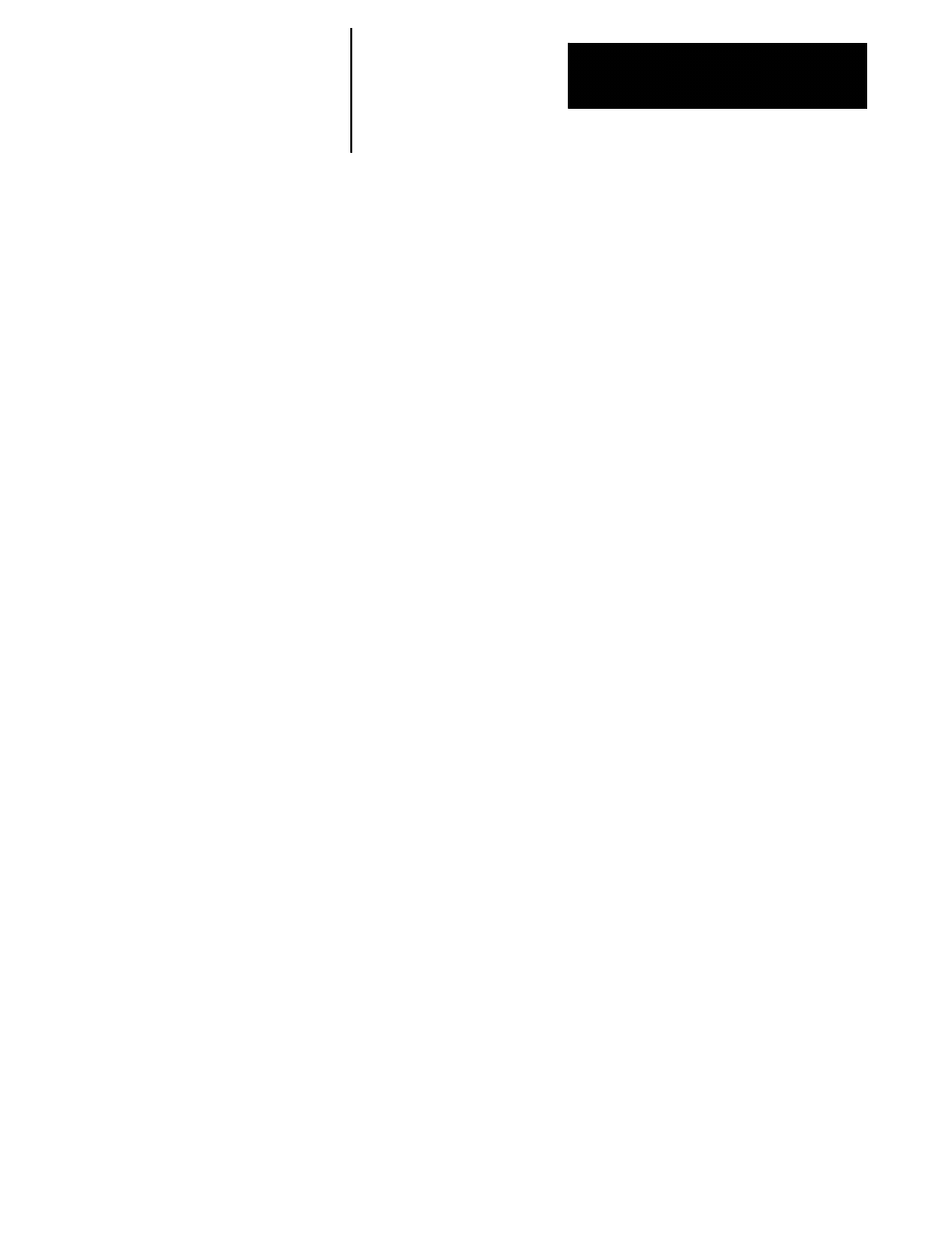
Servo Parameters
Chapter 7
7-13
Notes
A typical application of this parameter would be as follows:
1.
When you finish setting AMP on the ODS workstation, and have
selected standard motors wherever they are to be used, enter all
appropriate data for the motors, except the parameters Motor Rated
Current, Velocity Proportional Gain, and Velocity Integral Gain.
2.
Set this parameter to “Yes.”
3.
Download AMP to the control and test each axis that uses a
standard motor.
4.
If axis performance is acceptable, leave this parameter set at “Yes”.
5.
If axis performance is not acceptable, upload AMP to the ODS
terminal to view the gain values that the control calculated
and entered.
a.
Set this parameter to “No” and modify the gain values as
recommended in their parameter descriptions.
b.
Download AMP to the control and test each axis that uses a
standard motor.
c.
Turn the control off when instructed to do so after downloading
or changing AMP. When the control is turned back on, the
parameters modified in step 5 retain their modified value.
d.
Test the axis again, and continue modifying parameters as in
step 5.
6.
When motor performance is optimized, upload and/or backup the
final AMP file (leaving the Standard Motor Table Values parameter
set to “No”).
If problems are encountered during fine tuning, the original table values
for that particular motor can always be restored by downloading AMP with
this parameter set to “yes.” When power is turned on again, the control’s
internal motor tables are read.
Important: You can use patch AMP to modify this parameter and other
gain parameters to simplify tuning. Online AMP screens are also available
that allow you to change gain values real time. Adjusting the gain values
using online AMP will force this parameter (Standard Motor Tables) to
“NO”.
This parameter is global; the value set here applies to all axes.