Rockwell Automation 8520-ARM2 9/Series CNC AMP Reference Manual Documentation Set User Manual
Page 197
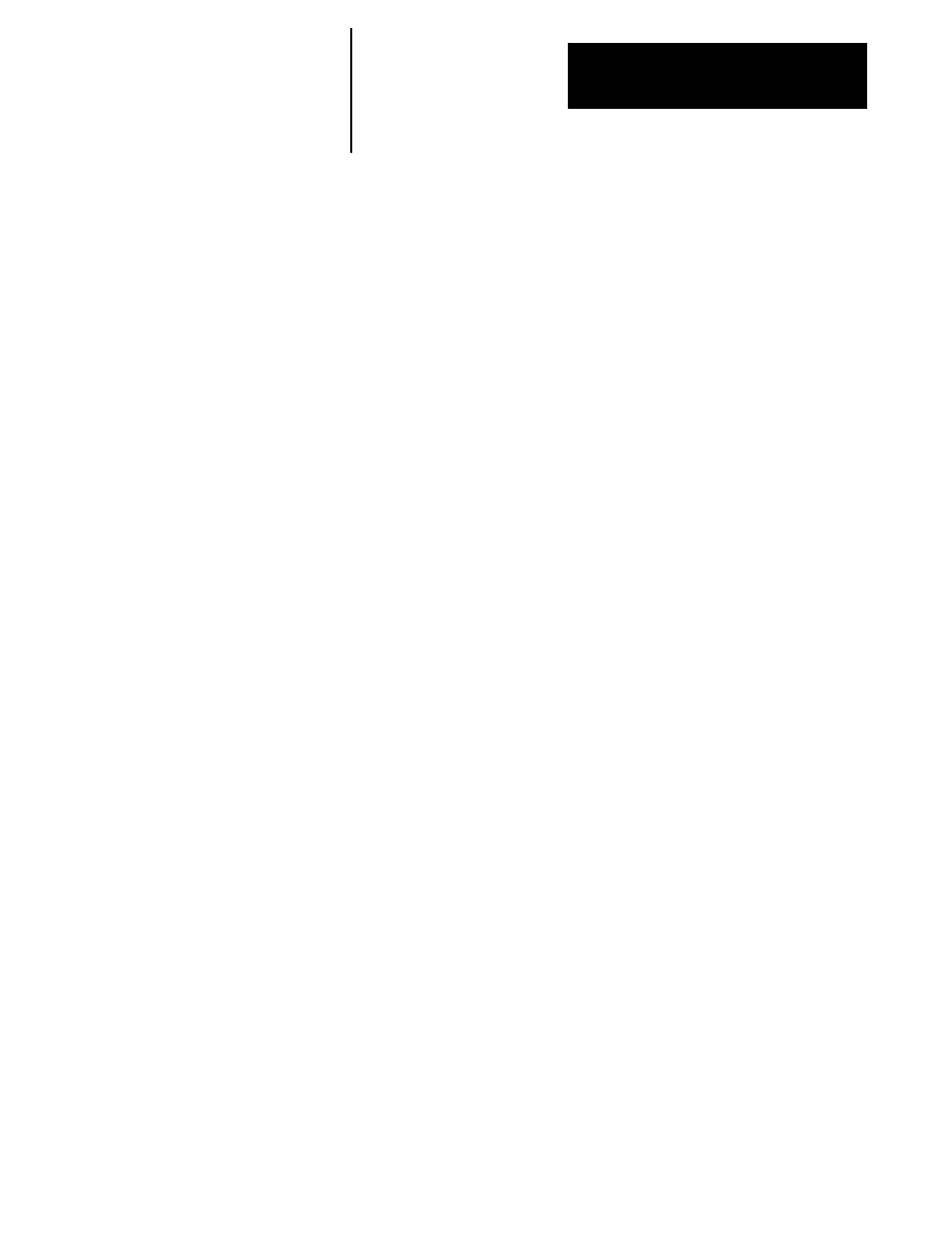
Servo Parameters
Chapter 7
7-51
Function
Position Feedback Counts/Cycle specifies the number of counts that are
produced by the encoder for each electrical cycle. For encoders with one
marker, an electrical cycle is one revolution. For encoders with two
markers, an electrical cycle is one half revolution.
Important: For single and no marker linear scales, enter the number of
counts expected per lead screw revolution (pitch) to establish the proper
number of counts per unit of travel. Use the parameters Position
Feedback Counts/Cycle and Lead Screw Thread Pitch to enter the
number of counts returned by the device per revolution of the lead screw.
The ratio between Teeth on Gear for Position FB and the parameter
Teeth on Lead Screw for Position Feedback should be one to one. For
example if the linear device has 5000 lines per .5 inch enter 5000 as the
Position Feedback Counts/Cycle and .5 inch as the Lead Screw Thread
Pitch. Both Teeth on Gear for Position Feedback and Teeth on Lead
Screw for Position Feedback can then be set to one.
Important: Encoders on spindles must have one marker per revolution
and must rotate on a 1:1 ratio with the face of the spindle.
Encoders are generally labeled with the number of lines they have per
electrical cycle. Since encoders used with the control must have 2
feedback channels (A and B) positioned in quadrature, the number of
counts produced is actually 4 times the number of lines.
Position Feedback Counts/Cycle = 4 x lines/elec. cycle
Important: If configuring an adaptive depth probe see page 32-7.
Important: If your position loop is closed through the resolver of a 1326
motor connected through a 1394 drive or you are configuring a 9/440
resolver based system, you must set this parameter to either 32,768 or 8192
counts. Refer to your Integration and Maintenance Manual for details.
7.2.13
Position Feedback
Counts/Cycle